Smooth functioning requires correct
speed sensor operation
An active magnetic bearing system (AMB) is based
around a noncontacting position servo control system.
The role of the position sensors and the position
servo control loop has been extensively studied and
reported elsewhere.
In this article we look at the role of a separate sensor,
which is generally included with an AMB system — the rotational
speed sensor. The article will examine design considerations
for obtaining a reliable speed signal, together
with the types of sensors that are used and then look at the
functionality within the AMB system that is dependent on
the resulting signals.
Overview of sensor hardware
There are a variety of speed sensor types used within
rotating machinery that can be categorized as either:
- Generating a once (or other multiple) per revolution
pulse that is derived by looking at a nonuniform target
on the rotor (typically a cutout in the target surface or
a colored band on the rotor). This is also commonly
known as a keyphasor sensor.
- An encoder-type system that directly measures angular
position. Rotational speed can then be inferred by taking
the derivative of angular position.
The reader should understand that rotational speed is different
from the lateral “velocity” (or rate of change of gap) associated
with the position servo loop of the magnetic bearings.
The majority of AMB applications use the notched target
to generate a once per revolution pulse. A schematic of
such a system is shown in Figure 1 (a circumferential target
surface). Alternate configurations can use an axial target
surface and rather than a slot, a permanent magnet insert
in a nonmagnetic target surface can be used. Depending
on the sensor type, the detection may be either on the absolute
level of the gap or may be by detecting the rate of
change of gap associated with the edges of the slot.
For a magnetic bearing with a moveable rotor, it is important
that the geometry of the cutout on the rotor and the
sensitivity of the sensor and working range of the sensor are
such that radial or axial movement within the auxiliary bearing
is not incorrectly interpreted as pulses due to rotation. It
is also important for there to be sufficient mechanical clearance
between the speed sensor and the target to prevent
mechanical damage due to contact.
Consequently, when selecting a speed sensor for a
magnetic bearing application it is important to have a good
understanding of the likely movement of the rotor and if
the sensor bandwidth will be adequate for the effective
frequency associated with the width of the resulting speed
pulse waveform.
A two-sensor scheme set apart in angular position will allow direction to be determined as shown in Figure 2. The pulse signals from two sensors are overlapping and there-fore the two outputs are used for indication of four states or angular positions. Effectively the resulting output is a two-bit Gray code, i.e., only one of the two sensors detects a change at any moment.
The sensor and target used in a particular application will depend on the requirements of the application. For general purpose AMB applications, a simple eddy current position sensor will provide sufficient bandwidth to give a good pulse waveform over the operating speed range (provided the tar-get is of sufficient width — i.e., the resulting pulse width is within the bandwidth of the output circuit of the sensor).
These may either be procured from third-party vendors or custom designed by the AMB vendor to fit within the machine geometry. Where third-party sensors are used, they will need to have the clearance set accurately. Such sensors typically have a threaded body, and adjustment is made by screwing the sensor body in or out and locking the position with a lock nut. If the gap is set too large, then the sensor may come out of its working range when the rotor moves away from the sensor (within the auxiliary bearing clearance). If the gap is set too small then contact may occur when the rotor moves toward the sensor.
Waukesha Magnetic Bearings (WMB) has also supplied custom-designed sensor rings. Similar to inductive position sensors, such components typically come pre-assembled and do not require the gap to be setup in the field, since this is done during manufacture of the sensor ring and during the final machining of the rotor target.
One such example uses five opposed pairs of eddy current sensors mounted onto a metal carrier ring. Eddy cur-rent sensors work with solid targets, and, in this particular case, rather than a notch, the target was an offset cam, resulting in a sinusoidal output from the sensor. The cam offset must be at least three times the auxiliary bearing clearance to obtain an accurate detection of the “zero” angular position.
A typical requirement is a pair of sensors for direction indication capability within the user’s system and a single speed signal for the magnetic bearing system. For high-reliability systems, sensor redundancy is often a requirement. For the offset cam target described earlier, two additional sensors would bring the total to five. The output for the five sensors is shown in Figure 3. Any two sensors selected would produce an overlapping output and thus be capable of direction of rotation indication.
For other applications, three of the sensors can be used in a two-out-of-three voting system.
For a canned active magnetic bearing application, a simple eddy current sensor is no longer applicable since this type of sensor is not able to look through the metallic liner typically used in canned magnetic bearing systems. Either a nonmetallic window must be created in the can (which will give rise to sealing problems), or a sensor that is able to operate through the can must be used.
WMB has good experience using inductive pickups looking through nonmagnetic metallic cans. These sensors are in principle a permanent magnet circuit, which includes the rotor, with a coil wound around the magnetic circuit.
As the notch passes the sensor, a pulse is generated by the sensor as each edge of the target passes the sensor. The sign of the pulses is different for the two edges, and the amplitude of the pulses is dependent on the rotational speed of the shaft. For this reason, the signal conditioning associated with this type of sensor will generally include an automatic gain controlled (AGC) amplifier at the front end of the circuit to work with the change in signal amplitude as shown in Figure 4.
A keyphasor sensor will generate its pulse at a defined angular position of the rotor. By timing the interval between adjacent pulses, the AMB controller is able to calculate the rotational speed. The output from the keyphasor also allows the AMB controller to identify the zero degrees angular position.
Given that rotational acceleration is limited, the AMB controller can also estimate the current angular position be-tween pulses. This ability to infer angular position is what underlies many of the algorithms to be covered later.
Because the angle-based algorithms are dependent on a good quality speed signal, the input signal conditioning of the AMB controller may have extra logic to allow for detection and ride through of both missing pulses and additional noise pulses.
Use of rpm within the AMB controller
The rotational speed within the AMB controller can be used for a wide range of purposes:
- Detection of rotation
- Display and recording of rotational speed
- Overspeed detection
- Special trip algorithms
- Speed scheduling of control law gains
The behavior of the AMB supervisory logic may depend on whether the machine is rotating. Typically the AMB control system will only de-levitate the rotor when the rotational speed is below a minimum speed threshold. This “zero speed detection” can also be used with other logic signals for detection of shaft rotational stall and together with a “start rotation” signal from the drive system for detection of speed sensor failure.
The display and recording of rotational speed can be either directly on the user interface of the AMB controller, or through a data transfer interface to other plant systems that may record or display the data. Recording of data within the AMB controller interface can be either for long-term trend analysis or for high-speed black box type capture.
In principle, over-speed detection could be derived from the AMB rotational speed; however for a certified over-speed trip system a SIL (safety integrity level) rated sensor and AMB system would be required.
Speed scheduling allows the gains within the position servo control law to be manipulated as the rotational speed changes. Typically parameters are either configured based on banded values or based on linear interpolation in a table of values versus rotational speed. A simple use of this might be to manipulate the stiffness control of the AMB system to “avoid” a natural frequency. In this scenario, the stiffness is set at a high value at low speed. This results in the natural frequency of the rigid body modes of the rotor being at a high frequency. Then once the speed reaches a higher level (but below the natural frequency noted above), the stiffness is set to a much lower value, reducing the natural frequency to a value below the current rotational frequency. The effect of this is that the rotor passes the critical speed without the associated response (Figure 5). This type of approach is particularly well suited to rotor systems that are subject to large changing levels of unbalance.
Use of angular position in the AMB controller
The reader may have been surprised by the wide range of uses of rotational speed within the AMB controller, but the use of angular position is even more surprising in its variety. The uses include:
- Tracking notch filters
- Runout compensation
- Capturing and recording of the harmonic components of signals such as position and current
- Open-loop, feed-forward control, also known as ONEX
AMBs are able to employ tracking notch filters that eliminate all (or a defined portion) of the stiffness at a given multiple of the shaft rotational frequency. Although a range of harmonics can be (and have been) applied, the most common use is where a first harmonic notch filter is employed. The resulting effect will allow the rotor to spin around its inertial axis rather than its geometric axis, thus eliminating all vibration transmitted to the machine casing (at the rotational frequency). This capability is unique to AMBs (compared to other bearing types) and has been widely deployed.
The tracking filter relies on a technique common in signal analysis, whereby the signal of interest is convolved with the sine and cosine of a waveform at the frequency of interest. The angular position is an essential component in the algorithm, since this is required in order to generate the values for sine and cosine.
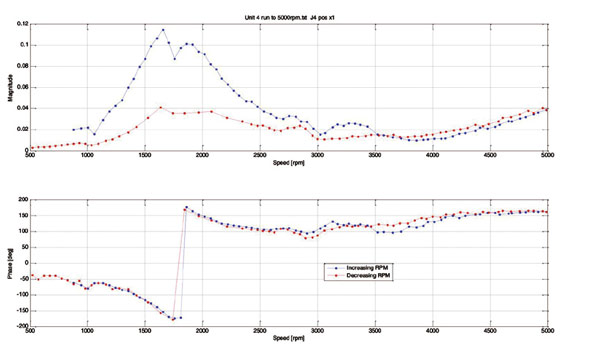
Figure 7. The output of Waukesha’s harmonic capture function.
The tracking notch filters are deployed in the forward path of the AMB feedback control loop (Figure 6). Because they are within the control loop, such filters must be switched off when traversing resonances. Where they can be used they are a very effective way of reducing transmitted vibration and also of increasing the effective dynamic capability of the AMB system.
Runout compensation allows irregularity in the sensor target surface to be compensated for (and consequently less stringent machining requirements to be specified). Runout compensation applies a rotating correction vector to the position signals associated with a bearing. The rotating vector is typically at rotational speed (or an integer multiple of this). This algorithm also relies on the sine and cosine signals to construct the rotating vectors and so is fundamentally dependent on angular position.
Runout compensation modifies (reduces) the system response, but it does this without modifying the dynamics of the AMB control loop. Consequently, runout correction at more than one harmonic frequency can be applied to a given position signal. Runout correction can also be applied while traversing natural frequencies (unlike the tracking notch filters).
The harmonic capture function allows signals such as position and current to be separated into their complex (magnitude and phase) harmonic components with respect to rotational frequency. The algorithm used to perform this analysis is similar to the techniques used in the tracking notch filters, where convolution with a sine and cosine at the desired frequency is required — consequently angular position is again a fundamental requirement.
The harmonic capture function within WMB’s AMB controller allows for up to three harmonics to be captured for all position and all current signals. These signals will typically be sampled at defined increments of either time or rotational speed. This allows a vibration response plot for the machine to be viewed and saved. Example plots can be seen in Figure 7.
ONEX provides attenuation of all types of vibration that is synchronous with the rotating frequency. Of course, rotating imbalance is the most common cause of synchronous vibration. ONEX is able to attenuate response to imbalance by a factor of 10 times. In rotor strings with more than two radial bearings, shaft misalignments and shaft bowing is an-other source of synchronous vibration that can be attenuated with the ONEX software function.
All feedback based AMB control systems have gain limits imposed by required stability margins. The gain limits impact the maximum values of equivalent stiffness and damping the bearing can achieve. ONEX functions with a feed forward principle, so increased maximum values of equivalent stiffness and damping of the bearing can be achieved.
The operation of both the ONEX and tracking notch filter algorithm is more fully described in a series of videos that can be found on the Waukesha Bearings web site: www.waukeshabearings.com.
The correct operation of the speed sensor is essential for smooth operation of an AMB-equipped machine, and consequently the speed sensor needs to be considered at an early stage in the design of a machine equipped with magnetic bearings.
Richard Jayawant is director of engineering for Waukesha Magnetic Bearings. He graduated from the University of Cambridge with a master’s, specializing in control engineering. Following work in a variety of control system application areas, he has been working in the field of active magnetic bearings for 27 years. His current focus is on the control systems applicable to this technology. Contact him at: rjayawant@waukbearing.com. Roy Leung is the principal engineer of Waukesha Magnetic Bearings, Worthing, U.K. He has been in magnetic bearing development for more than 25 years. Currently he supports the design and development of sensors for magnetic bearings. He has a bachelor’s degree from Imperial College, London, and a doctorate from Plymouth University. Contact him at: rleung@waukbearing.com.