The challenges are many in the production of biopharmaceuticals. The only way that critical mixing applications can be completed successfully is if the proper equipment, from pumps to bags to hoses to connectors, is utilized. Learn about a single-use mixing system which combines special quaternary (four-piston) diaphragm pumps with the biopharmaceutical expertise of single-use systems.
Two decades ago, friends and colleagues, Mark van Trier and John van der Veeken, set out to form their own biopharmaceutical trade company, the result of which was JM Separations, which they headquartered in Tilburg, The Netherlands. Over the years, the company’s mission has evolved and JM Separations has become an engineering and design firm for the biopharmaceutical industry. “Over time we had more and more of a passion to have our own manufacturing, our own products, our own engineering team and supply the customer with process solutions,” said van Trier, and “We really want to help customers with our solutions,” added van der Veeken.
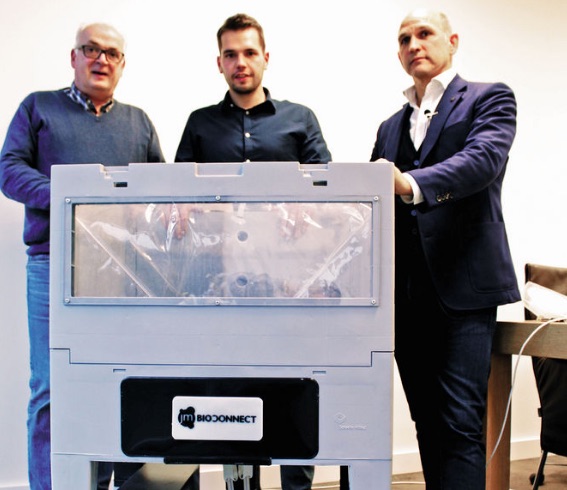
The JM Separations team — John van der Veeken, left, Tom van der Veeken, middle, and Mark van Trier, right — are filling a niche in the batch-mixing world with the Quattro Mix Single-Use Mixing System.
In recent years, the duo observed the industry-wide growth of single-use equipment and especially pumps in biopharmaceutical processes and identified that as an enabling technology that they could offer their customers. They believed these pumps were a better manufacturing solution because of the low cost compared to permanent stainless-steel pumping systems and the simultaneous ability to ensure the necessary level of high-purity production that is required. Specifically, they felt they could fill a niche where batch-mixing operations could be performed and enhanced through the use of single-use pumping equipment.
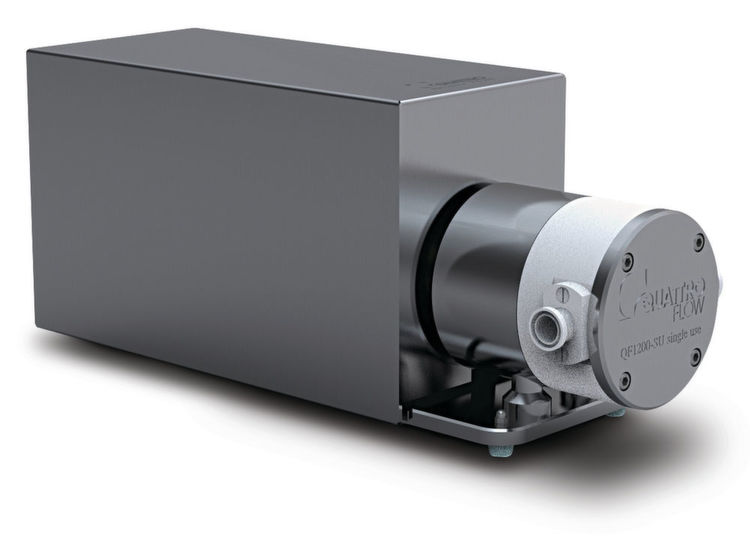
Quattroflow single-use quaternary diaphragm pump
For a solution, they reached to the past, in this case, to former colleague Frank Glabiszewski, who had worked with van Trier and van der Veeken in the early 1990s. Since then, however, Glabiszewski had, with partner Josef Zitron, invented the positive displacement quaternary (four-piston) diaphragm pumping principle and founded Quattroflow Fluid System in Germany. In 2012, Quattroflow was acquired by the Dover Corporation’s PSG. PSG has subsequently integrated the manufacture of Quattroflow pumps into the operations of its Almatec subsidiary, which is headquartered in Kamp-Lintfort, Germany.
“In 2010, we started working with Frank Glabiszewski of Quattroflow to build a mixing system,” said van Trier. In 2013, he said, “I think I have the solution for you.” That solution, which would come to be called the Quattro Mix Single-Use Mixing System, and also prompted JM Separations to create a new division named JM Bioconnect, features a Quattroflow Quaternary (Four-Piston) Diaphragm Pump used to circulate the liquids and solids in a mixing bag in order to achieve the necessary mix and dilution rates, all within an optimized time frame.
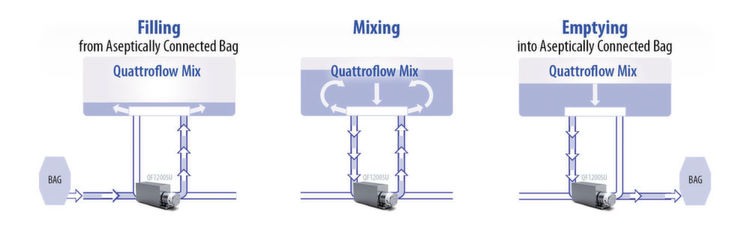
Ein Vorteil des Quattro-Mix-Systems besteht darin, dass alle Arbeitsschritte zum Befüllen, Mischen, Entleeren und Filtern nach dem Mischen mit einer einzigen Quattroflow-Pumpe ausgeführt werden können.
Human Heart as Model
The main benefit of using Quattroflow pumps in biopharmaceutical-mixing applications is its form of operation: the four-piston diaphragms are driven one after another by a connector plate, which moves back and forth out of its central position in a stroke that is generated by an eccentric shaft, with the length of the stroke determined by the angle of the eccentricity. In other words, the Quattroflow technology has been modeled on the operation of the human heart with its four pumping chambers and check valves keeping product flow constantly moving forward.
The Quattroflow’s pump chambers contain no rotating parts that can be subject to friction, meaning that there is minimal operational heat buildup that can compromise the product. This mode of operation also means that the pumps can run dry, are self-priming and produce little shear because of low slip. In addition, they offer low-pulsation and leak-free operation. Quattroflow pumps also have some of the highest turndown capabilities in the industry, which ensures that the pump’s operation does not adversely affect repeatability and production rates.
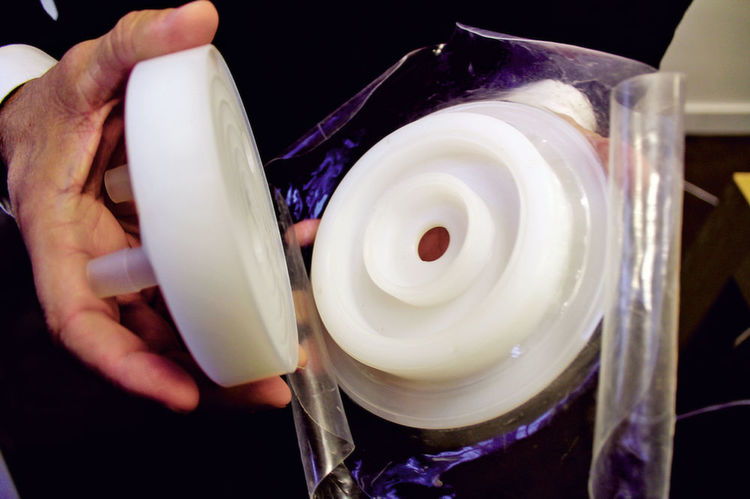
The Quattro Mix system has a very basic, easy-to-understand operating principle and includes a single-use mixing bag, a Quattroflow pump (with single-use pump head which is pictured above), and a 16-hole mixing plate that is built into the bag.
All That, And So Much More
“What makes this unit so nice is that we can work directly with the pumps from Quattroflow,” said van Trier of the Quattro Mix. “We like them because the pumpheads minimize particle shedding, which is very important for biopharmaceutical companies.”
The Quattro Mix system has a very basic, easy-to-understand operating principle. A single-use mixing bag is filled via a Quattroflow pump through a 16-hole mixing plate that is built into the bag. After the proper amount of mixing agent is injected into the mixing bag, the Quattroflow’s pumping action through the mixing plate forces the liquid from the bottom of the bag, up around the outer walls and back down through the mixing plate in the center, where it is recirculated through the pump.
“Together with PSG we have invented a very nice mixing system that’s based on the technology of the Quattroflow pump with the mixing plate inside, and the technology from JM Bioconnect that has all of the parts together to make a nice single-use piece of process equipment,” said van Trier. “Since the Quattroflow pumps have a nice capacity, they can run up to 1,200 liters an hour (or 317 gph), we can mix very well. We can mix liquid/liquid solutions as well as liquid/powder solutions.”
The unique, impeller-free operation of Quattroflow pumps also gives them distinct operational advantages over competitive types of mixing systems. “The challenge for other suppliers of mixing technologies is that most of the mixing systems have a magnetic part on them or they have an impeller,” said van Trier. “Some mixing solutions have magnetic beads so a magnetic part will not work with that application. If you have a mixer inside the bag, that creates the chance for contamination on the impeller since the impeller has to go through the bag. This is something that you don’t have with this type of installation. You have a pre-packed complete unit with the pumphead next to it. You install it as a complete unit, install the disposable pumphead to the motor and start filling with water; basically it’s a plug-and-play unit.”
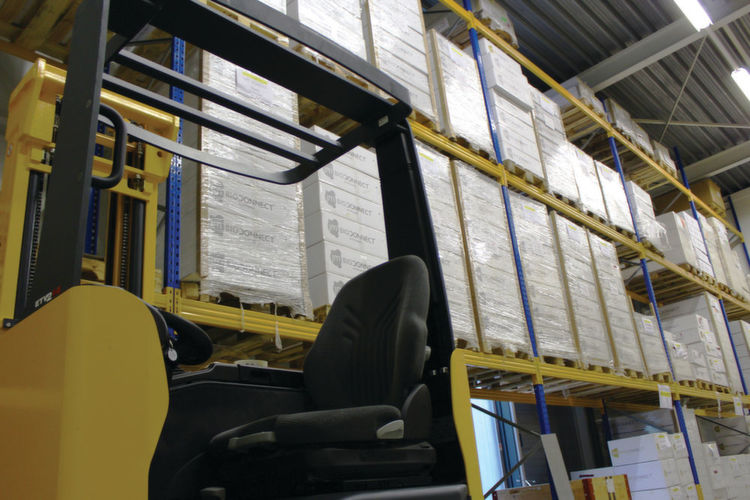
Since the Quattro Mix system has come on the scene, the JM Bioconnect customer base has rapidly grown to include such global pharmaceutical giants as Johnson & Johnson, Pfizer and Novartis.
Reduced Risk of Contamination
The Quattroflow pump is also versatile enough that it can be used to transfer the newly mixed solution from the mixing bag to a storage unit without the need to utilize another pump. This decreases the chance that product contamination will occur.
“In the biopharm industry, single-use has become more and more popular because we want the product to come to market as quickly as possible,” said van Trier. “They don’t want to spend time cleaning because cleaning and validation take a lot of time and also a lot of labor goes into the cleaning cycle. With single-use you don’t have to clean anymore, your operators can just make the product, get a new bag, put it in place and go forward. It’s also cheaper when compared to stainless steel, and after 30 minutes the customer has his liquid perfectly prepared; that’s the aim of the system.”
On top of all that, JM Bioconnect has turned to another Dover company, CPC, for the connectors that link the mixing systems to the mixing bag and pump. Specifically, the Aseptiquik line of connectors help the Quattro Mix become a completely sterile system with no additional sterilization procedures required.
Currently, JM Bioconnect is offering the Quattro Mix system with mixing-bag capacities of 50, 200, 500, 1,000 and 1,500 liters (13 to 396 gallons). “With this integrated system featuring Quattroflow pumps we eliminate a lot of problems other suppliers have,” van Trier summarized. “Minimal particle generation, elimination of the chance of contamination, elimination of a magnetic field inside the bag, elimination of an extra pump to transfer the fluid to another place. All these things are built into the design of the system.”
The author is Applications Manager Biotech/Biopharma for Quattroflow Fluid Systems, Almatec, Kamp-Lintfort, Germany.