An Ink manufacturer increases efficiencies while reducing energy costs with its new pump installations.
Fluid leaks were halting production at Chimigraf's ink-manufacturing facilities several times a week. For many years, gear pumps transferred raw materials and finished products, but now the Barcelona, Spain-based manufacturer was facing maintenance costs, downtime and operational efficiency loss.
The solution for the four production factories — one each for water-based inks, solvent inks, blending inks and digital inks — would ultimately come in the form of a new kind of pump. Last year the company produced 12,000 tons of inks for use in flexography, rotogravure and digital printing systems and exported 15 percent of it to Europe, North Africa and South America. With ink sold in more than 60 countries, operational inefficiencies needed to be resolved quickly.
A pump solution
For a solution Chimigraf president Ugo La Valle reached out to Alberto Maestre Hoffmann, managing director at Barcelona pump distributor Tecnica de Fluidos (TDF Group). The companies have worked together for 33 years.
"We had wear problems and had to maintain them a lot because every month we had some kind of problem we had to repair: said La Valle. "It was a lot of added expense, and we had to stop working, which was another problem.”
Hoffmann's suggestion for a cure came in the form of 100 Wilden air-operated double-diaphragm (AODD) pumps to replace the 20 gear pumps in 2014. La Valle said they chose the brand for its technical service and price point.
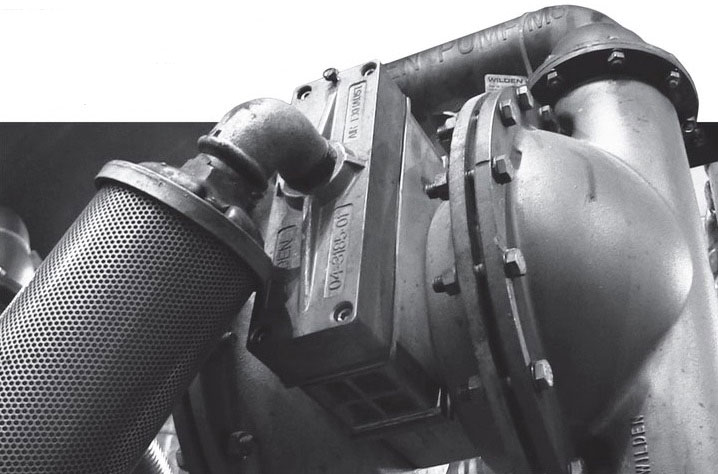
AODD pumps replaced the ill-performing gear pumps at the Chimigraf facilities.
An energy-efficient replacement
Following this replacement, La Valle upgraded six pumps with Wilden's Pro-Flo SHIFT Air Distribution System, which was introduced in 2013. The system can reduce air consumption by up to 60 percent by using an air control spool to eliminate the loss and waste of air that would naturally occur at the conclusion of the pump stroke.
"[It] addresses the problem we are facing today, which is the issue of energy consumption: said Hoffmann. "In Europe and, I think, all over the world, companies and individuals are getting more and more aware of energy efficiency. We have seen how dramatic the reduction in air consumption is with this solution.”
The plant has found that the pumps enable them to save air while seeing the same or better results. "The use of electricity in air is very expensive, so if we can do the same work with half of the energy it is very important: said La Valle. "For me, this pump is a very good choice, and I am sure that the results will demonstrate that.”
To spread the word on the importance of reducing air consumption, Hoffmann is having a test skid constructed to take to potential customers for on-site demonstrations.
"We can explain it very well, but it's something different when the customer can see it..." said Hoffmann. "We believe the difference is so important that we really want to show our customers with their own eyes how dramatic the savings are.”
Conclusion
Starting with the AODD pumps, Chimigraf has worked with TDF Group to replace the pumps in its facilities. This partnership allows the manufacturer to maximize the cost and operational efficiencies of its global ink-manufacturing operations.
Michelangelo Branconi is the EMEA regional sales manager, South Europe for Wilden and PSG. He may be reached at michelangelo.branconi@psgdover.com. Wilden is a brand of AODD pumps from PSG, a Dover company. Headquartered in Oakbrook Terrace, Illinois, PSG is comprised of several pump brands, including Abaque, Almatec, Blackmer, Ebsray, EnviroGear, Griswold, Mouvex, Neptune, Quattroflow, RedScrew.