Learn how a producer of specialty chemicals optimizes the safety and reliability of polymer-emulsions manufacturing with the assistance of special eccentric disc pumps.
Any student can tell you that receiving a red mark on a project, test or report card is a bad sign, an indication that performance did not meet expected standards. Believe it or not, such a rudimentary grading system is also used to signify less-than-acceptable performance in the world of industrial manufacturing. Just ask Rob van Oostveen. “I only have one main KPI (Key Performance Indicator), and that is no loss of production,” explained van Oostveen. “Every time I have loss of production, I get a red mark under my name.”
Of course, any red marks van Oostveen receives have a much farther-reaching effect than a student’s failed math or science test. That’s because van Oostveen is the Maintenance Manager and a member of the Leadership Team for Organik Kimya’s facility in Rotterdam, The Netherlands.
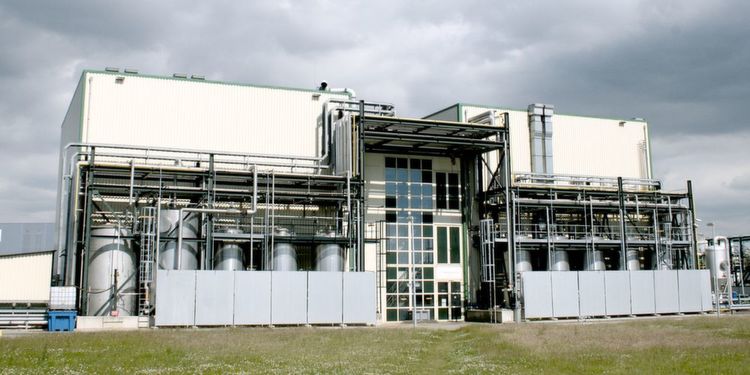
Located in the huge Botlek chemical complex in Rotterdam Harbor, The Netherlands, the manufacture of polymer emulsions is Organik Kimya’s most prominent business globally.
Organik Kimya, with international headquarters in Istanbul, Turkey, is a globally recognized producer of polymer emulsions and specialty chemicals for use in a wide array of industrial manufacturing processes.
In 2007, Organik Kimya opened its facility in The Netherlands, which is located in the huge Botlek chemical complex on Rotterdam Harbor. This facility most prominently produces polymer emulsions for the paint and coatings industry and for adhesive tapes, compounds that van Oostveen refers to as “sticky products.”
The manufacture of polymer emulsions is Organik Kimya’s most prominent business globally, with more than 250,000 metric tons (551 million pounds) produced a year, with 80,000 metric tons (176 million pounds) coming from the Rotterdam facility. Organik Kimya’s product portfolio includes more than 150 different types of polymer emulsions that are supplied to more than 1,000 customers operating in a total of 85 countries.

The production of monomers is dangerous business because they can be toxic and flammable. Therefore, breakdowns and leaks can not only be harmful to Organik Kimya’s bottom line but can also cause injury to site personnel and the environment.
Staying Out Of Harm’s Way
“What we do is make polymers,” said van Oostveen. “We have emulsion vessels where we put together different types of monomers. From those vessels we pump to the reactor vessels where the monomers start reacting and forming polymers.”
Critical to the successful operation of the Rotterdam plant is not only that there are no production-halting breakdowns — which result in those pesky red marks on van Oostveen’s resume — but that all of the raw and finished products are always safely contained since many of them can be toxic or hazardous to both humans and the environment.
“Monomers are dangerous because they can be toxic and flammable,” continued van Oostveen. “The most important thing is if the pumps fail during the middle of an operation we have to get the monomers out because they can react and you do not want a lot of harmful materials sitting in the pump for a long time. Also, if we have too much maintenance on the pumps, every time we have to open the system with dangerous materials it can be harmful to people and the environment, so every time we don’t have to open a pump it’s better because you protect everyone and the environment.”
Breakdowns and leaks can be harmful to Organik Kimya’s bottom line not only in lost in-service time and injury to site personnel and the environment, but in the amount it costs to actually clean up the leak and the pump. “If we have to open up a pump, we have to flush it every time and flushing takes time and a lot of money, and also creates a lot of safety issues,” said van Oostveen. “We have to flush the complete system, remove the pump and flush it again to make sure there are no chemicals inside it before we can even open up the pump; it takes a lot of work. Even a very small spill, you can smell it, and every time we have a spill, you have to take the people out of the area, someone has to investigate it and every time that happens it can take half an hour, which is not good because it is costing us money.”
Additionally, the pumps must also be Atex-certified since they are handling potentially flammable materials. This also means that the pumps cannot generate any excessive heat when they are operating, as this heat could ignite the flammable materials, which could lead to a whole other set of problems for the facility.
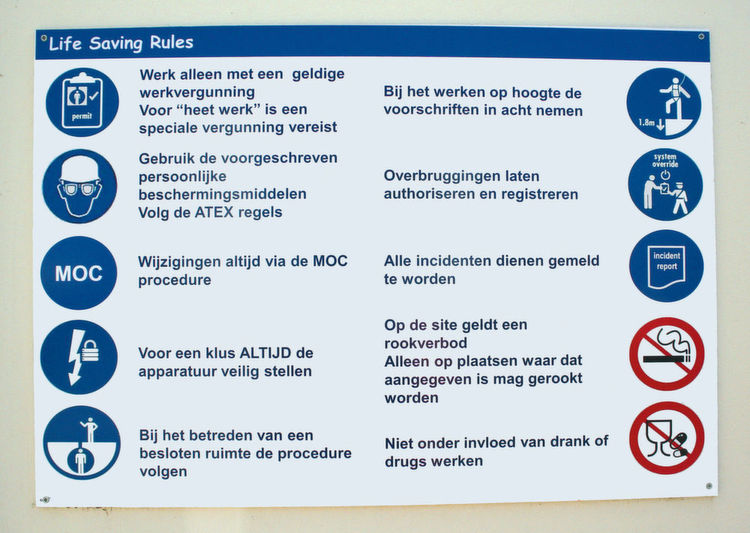
Rob van Oostveen (right), Maintenance Manager for Organik Kimya, doesn’t worry about production loss thanks to the Mouvex eccentric disc pumps he deploys to manufacture the company’s polymer emulsions. Recommended by Rob Blok (left) Account Manager at Verder, the Mouvex distributor, the pumps provide Organik Kimya with the safety, reliability and dependability the company needs to keep the facility up and running.
No Convincing Needed
Since 2007, the process of transferring a blend of monomers and water from the immersion vessels to the reactors has been handled by a quartet of C24i Series eccentric disc pumps from Mouvex. The pumps were supplied to Organik Kimya by Verder. For more than a century, Verder has been a distributor of positive displacement pump technologies for use in various industries, including chemical processing, food and beverage, and water/wastewater.
The Mouvex C24i pumps are ideal for Organik Kimya’s needs because they feature a seal-free design that does not require a mechanical seal, packing or magnets, which eliminates leakage and reduces maintenance and downtime. They also operate via the unique Mouvex eccentric disc operating principle, which allows for consistent flow rates and improved energy savings. They are dry-run capable and can handle both low- and high-viscosity liquids, while their strong suction power allows them to successfully clear pipes of expensive materials and useable end products. The C24i model is specifically capable of delivering a flow rate of 24 m3/h (6,340 gph) at differential pressures to 9 bar (130 psi) and at speeds up to 460 rpm.
“Downtime in these types of plants costs a lot of money, a lot more money than the actual price of the pump,” said Rob Blok, Account Manager for Verder, which operates offices in every country in Europe, including four in The Netherlands. “If downtime is one or two hours, that can be € 50,000 to € 100,000 (US$ 54,500 to US$ 109,000). That’s why they chose the Mouvex pumps, for the reliability and the low maintenance costs. In the beginning, it is sometimes difficult to convince the customer, but they had experience with other pumps with a lot of cost and a lot of downtime, but with this pump we just say try the pump and if it is not working we’ll take it back, but we have never had to take it back. This pump, it sells itself, and that is what’s good about the pump.”
You won’t have a hard time convincing van Oostveen of that! “We could probably be using an AODD (air-operated double-diaphragm) pump for this application, but we prefer Mouvex because it’s fully enclosed,” he said. “A normal pump has a lot of wear parts, a lot of soft parts, and this pump has no soft parts inside, that’s why it’s very low maintenance. Also, with its system of pumping, it doesn’t matter if the clearance is one micron or one millimeter (equivalent to 1,000 microns), it’s still pumping.”
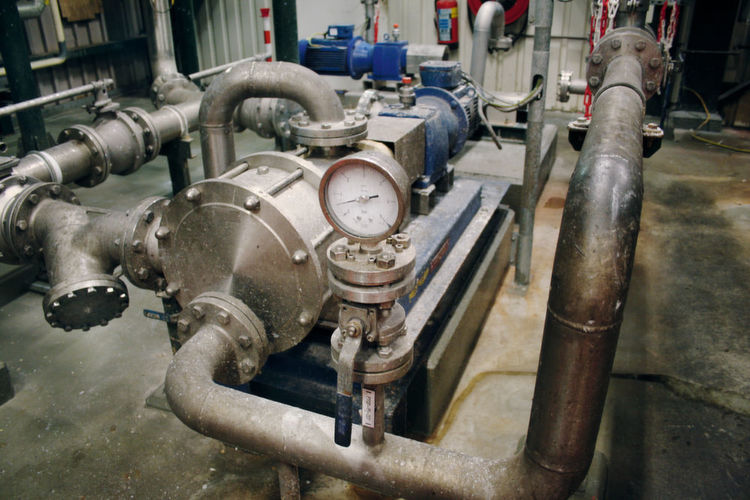
Organik Kimya has a long list of demands for its pumps, and Mouvex C24i Eccentric Disc Pumps check all the right boxes for the company.
“They are very pleased with the C24i pumps because in the past they have had a lot of problems with mechanical seals and these pumps don’t have a seal,” added Blok.
The C24i’s leak-free design also goes hand-in-hand with Organik Kimya’s commitment to sustainability and environmental awareness in its polymer-production processes. The company ensures that all of its production activities are undertaken while adhering to the most stringent environmental safeguards and since the 1990s has allowed audits to be performed by insurance companies with possible risks evaluated and eliminated or minimized through the implementation of environmentally conscious technologies like the C24i eccentric disc pumps.
The only shortcoming in the relationship between Verder and Organik Kimya falls into the “good problem to have” category and that is that van Oostveen and Blok don’t get to see each other very often because, except for yearly maintenance, there is no need for the distributor to come to the plant to check on the Mouvex pumps.
“We do not do a lot of business with Verder and they do not sell a lot of Mouvex pumps to us because we keep them running,” van Oostveen chuckled. “We rely on Verder for the specialization of maintenance and inspection because they know exactly how the pump works, they know exactly what to check during an inspection and they know exactly what to replace, if needed. We’ll buy new pumps from them if we need them, but not because these pumps have failed.”
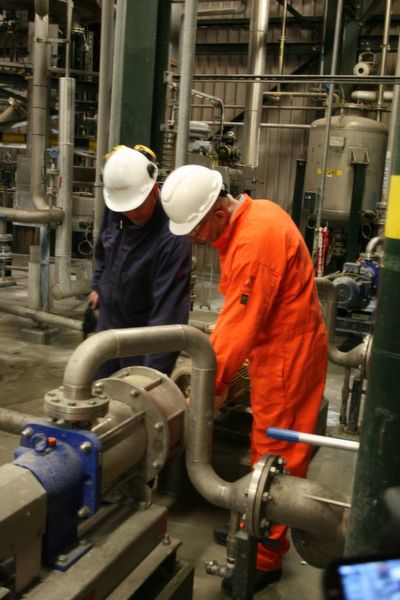
Unfortunately, van Oostveen and Blok don’t get to see each other very often because, except for yearly maintenance, there is no need for the distributor to come to the plant to check on the Mouvex pumps.
Conclusion
Because van Oostveen dreads ever getting one of those ugly red check marks on his work report, he has a long list of demands for the pumps that are charged with manufacturing Organik Kimya’s polymer emulsions: they must be reliable, dependable, easy to operate and, most important, safe for site personnel and the environment. The Mouvex C24i Series Eccentric Disc Pumps that Organik Kimya deploys at its Rotterdam facility check all the right boxes for van Oostveen.
“A leaking pump is not part of our business, a leaking pump is a bad deal, a leaking pump causes trouble in matters of fire-safety risk and also in toxic risk,” he said. “What’s important for me is that we do the first time right. We do not have a lot of time to play around with pumps and pump failures. We need the pumps running — running, running over and over again. We use Mouvex pumps because of their simple and safe way of operation. If I had to choose pumps for another application, I would choose Mouvex again.”
The author is the EMEA-Director of Sales for Mouvex and PSG.