The environmental laws keep changing. How is a retail fuel site supposed to remain compliant and competitive?
Canadian fuel marketers are facing increasingly strict environmental compliance regulations that require additional monitoring technologies at their fuel sites.
As recently as 2013, the Technical Standards & Safety Authority, which administers Ontario’s public safety programs and services, mandated in its Liquid Fuels Handling Code that all under-dispenser sumps and dispenser pans in Ontario must be electronically monitored by tank-gauging systems. The regulation calls for the installation of under-dispenser sump liquid sensors that will signal the attendant and shut down the dispenser when any product or high level of liquid is present in the sump. Prior to this mandate, however, many Canadian fuel sites never deployed sensors in their tank-monitoring systems.
These new regulations pose a challenge for many Canadian fuel sites, which, up until now, have utilized only a minimal amount of monitoring technology (or are relying on obsolete tank monitoring equipment) to support their compliance management needs. Although becoming compliant isn’t necessarily cheap or easy — installing new monitoring equipment can result in undue downtime and significant installation costs — innovations in tank monitoring equipment and infra-structure can significantly simplify new installations.
Currently, the regulations for Canadian provinces and territories are not consistent. As the regulations become stricter and expand to include fuel sites in other provinces, Canadian fuel site operators need to implement fuel monitoring systems that will provide cost-effective compliance monitoring for their needs now, and flexibility for the future. In order to achieve this, however, site operators must first understand the fundamental role that installation nuances play in equipment costs and the long-term application of their monitoring equipment in the future.
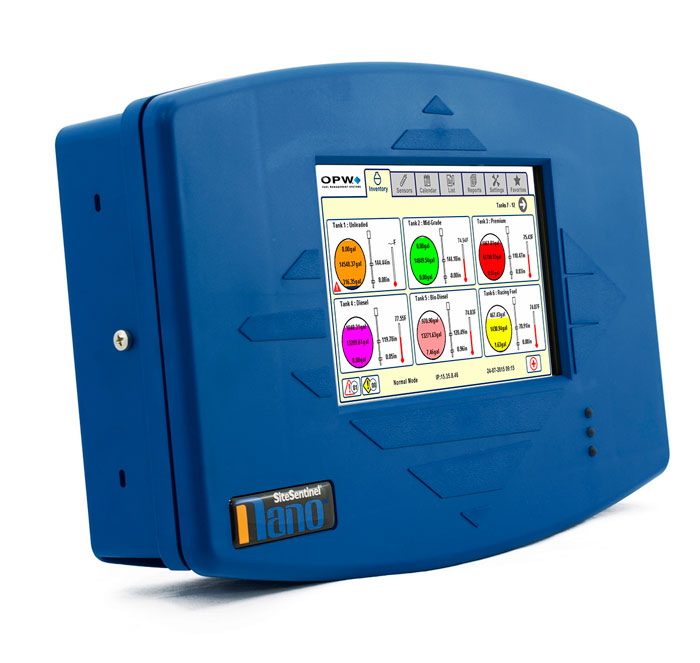
OPW’s SiteSentinel® Nano® Console supports OPW’s Mixed Multi-Drop Technology, which enables probes and sensors to be installed on the same wire.
How Inefficient Wiring Increases Costs
Most tank gauges require probes and sensors to be installed on individual, separate wires. This inefficient configuration results in a high number of expensive “home runs” being wired back to the tank gauge, which significantly increases the amount of wire and time needed to complete a new tank gauge installation. Fortunately, new technologies make this no longer necessary.
For example, a fuel site with four dispensers and three tanks that is utilizing an older wiring configuration is likely to need 10 or more home run cables back to the tank gauge. Whereas tank gauges that support a stream-lined wiring configuration significantly lower the amount of cable needed for installation — in some cases reducing the number of home runs to just two or three. This reduction in home runs decreases the amount of wire needed by hundreds of meters.
In addition to requiring more wire for installation, older tank monitoring systems and wiring configurations waste a larger amount of the wire purchased due to the limited lengths of cable that are available per spool of wire. Spools come in lengths of 152 meter and 309 meters (500 feet and 1,000 feet) of wire. Runs can often be 46 meters to 61 meters (150 feet to 200 feet). As a result, there are often extra 30- to 61-meter (100- to 200-foot lengths) lengths of wire at the end of spools that cannot be used for home runs. For almost every spool of wiring purchased for a fuel site monitoring system, there is a length of wire at the end of the spool that cannot be used at installation. The more spools the installation requires, the more wire that is wasted.
Inefficient wiring configurations also increase labor costs and the site downtime needed to complete the installation (the more wiring runs there are to install, the longer it will take a contractor to complete the job). For station operators in northern Ontario, who have voiced concerns about meeting the TSSA’s piping and sump compliance requirements due to the region’s short construction season and limited availability of certified fuel contractors, an efficient wiring design can mean the difference between project completion and persistent delays.
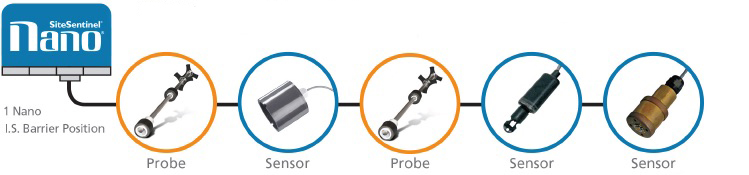
OPW’s SiteSentinel® Nano® Console can hold probes and sensors on the same I.S. barrier position.
Market Solutions
OPW Fuel Management Systems, based in Hodgkins, IL, recognizes the tank monitoring challenges faced by Canadian fuel site operators, including changing compliance requirements and rising operating costs. To help fuel marketers and distributors streamline compliance management and optimize their equipment investments, OPW has engineered an end-to-end tank monitoring system that provides state-of-the-art compliance monitoring, minimizes site downtime that typically results from installation/equipment upgrades, and provides operators long-range flexibility to adapt their system to changing compliance requirements.
At the heart of OPW’s end-to-end tank monitoring system is a cost-saving tank gauge and wiring configuration that allows probes and sensors to be run back to the gauge on the same wire. OPW first pioneered multi-drop technology in 2007 with its SiteSentinel® iSite™ tank gauge, which allowed up to 4 probes or 16 sensors to be installed on the same I.S. barrier channel. OPW has further enhanced this innovative technology, engineering a tank gauge wiring configuration called Mixed Multi-Drop that, when used in conjunction with OPW’s SiteSentinel® Nano® tank monitoring console, enables multiple probes and multiple sensors to be installed on the same wire (up to 12 probes or 24 sensors per gauge can be mixed and matched in combination on the same gauge). This efficient wiring configuration complements the streamlined nature of the Nano, which supports a wide range of sensors. The Nano with Mixed Multi-Drop enables Canadian fuel sites to meet the dispenser pan and dispenser sump monitoring requirements of the TSSA in an extremely flexible, cost-effective manner.
For a Canadian retail site that currently has 3 tanks and 4 dispensers, OPW’s Mixed Multi-Drop can reduce the amount of wire needed for installation by as much as 60 to 70 percent. The Mixed Multi-Drop achieves this efficiency by limiting the cable runs from the tank gauge to the equipment (at a small site, home runs can be reduced to just two or three runs). With a Mixed Multi-Drop wiring con-figuration, a small site could install three tank probes, three STP sump/annular sensors and 4 dispenser pan sensors, and plan for additional tank monitoring sensors and dispenser pan sensors to be added in the future. Site operators who deploy OPW’s Mixed Multi-Drop at their station also will save money on the amount of conduit or Teck cable needed to complete the installation and the amount of wire that is wasted. Operators can expect to save between 45 percent and 55 percent on these expenses.
Although understanding all of the costs associated with installing a tank monitoring system can be somewhat intimidating, the effort usually pays off. When the costs for all of the materials and labor needed for a wiring installation are factored in, a fuel site that is wired with efficiency in mind can realize substantial installation cost savings. OPW’s Nano console, when compared to other gauges that don’t offer Mixed Multi-Drop technology, can save Canadian fuel sites an average of 50 percent to 60 percent. Consulting with a qualified fuel equipment representative to review installation costs and to identify potential cost-saving technologies for your site will likely improve your bottom line.
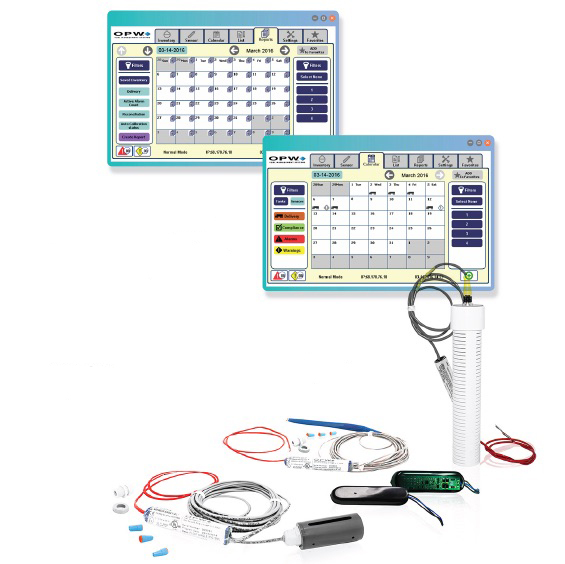
OPW’s SiteSentinel® Nano® streamlines inventory management and compliance reporting through an easy-to-use interface.
OPW’s SiteSentinel® Nano® Console supports an array of sensors, including discriminating sump and dispenser pan sensors.
Why an Upgrade Path is so Important
In addition to implementing a tank-monitoring system that deploys a cost-saving wiring strategy for new equipment installations, Canadian retailers would be wise to align themselves with an equipment brand that is designed to adapt to changing compliance needs.
For example, site operators who are currently using OPW’s SiteSentinel® iTouch™ tank gauge can upgrade to OPW’s Nano tank gauge, add Intelli-Sense modules to their existing sensors and multi-drop monitoring devices on the existing home-run wiring. This not only preserves their investment in their original home-run wired sensors, it allows operators to combine monitoring devices on the same wire. As a result, more devices may be installed within the original wiring framework. In addition, the Nano will provide remote connectivity and user-friendly compliance reporting tools. What’s more, this upgrade can be achieved with minimal disruption to operations. Should more stringent regulations become mandated in Canada, OPW’s SiteSentinel® family of fuel monitoring equipment offers an upgrade path from the Nano that would enable the site to retain its existing probes and sensors and only require changing out the tank gauge console.
Conclusion
As provincial and federal authorities continue to shape energy policies, regional fuel site compliance regulations will expand and become more stringent. As a result, Canadian fuel sites need to position their operations to meet the compliance requirements of today and tomorrow in order to minimize their equipment costs over the long-term. Fuel equipment manufacturers who are vested in their customers’ bottom line develop their product portfolio around this premise. Deploying a tank-monitoring system — such as OPW’s Nano — that is engineered to streamline compliance management, reduces installation costs and provides flexibility for changing needs will help Canadian fuel sites be both compliant and competitive for years to come.
Author: Bobby Hayes is the Domestic Sales Manager at OPW Fuel Management Systems in Hodgkins, IL. He can be reached at (770) 605-9611 or
robert.hayes@opwglobal.com.
OPW is a global leader in fully integrated fluid handling, management, monitoring and control solutions for the safe and efficient handling of critical petroleum-derived fluids from the refinery to the commercial and retail points of consumption. OPW is an operating company within the Fluids segment of Dover Corporation. For more information about OPW, please visit www.opwglobal.com.