US trucking companies aren’t alone in facing ever stricter vehicle emission rules. The same is true for the carriers operating in the European Union countries.
The Schmidt Group, based in Heilbronn, Germany is one of those European carriers, and its management team has been very proactive in addressing the EU emission directives. It’s all part of the dry bulk transportation specialist’s focus on providing customers with the most efficient service.
A member of the Responsible Care Program of the European Chemical Association (CEFIC), The Schmidt Group has become one of the leading dry bulk logistics groups in Europe. The company operates 800 dry bulk transports, 5,000 intermodal containers, and a network of storage and warehouse facilities. The group annually delivers 4.6 million metric tonnes (10.1 billion pounds) of dry bulk materials.
“We run state-of-the-art tractors with engines meeting the current European standards,” says Michael Hoyer, Schmidt Group fleet manager. “We also operate some of the most efficient dry bulk equipment in Europe. All of this is to give our customers the best possible service.
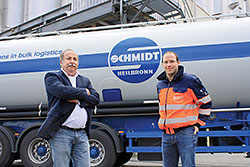
Michael Hoyer [left], fleet manager for The Schmidt Group, and André Saam, dry-bulk fleet manager for The Schmidt Group, have optimized the weight and driver comfort in its dry-bulk fleet by switching to MH6 Series screw compressors from Mouvex and Hydrocar.
“Engine emission limits have made our job more challenging. We faced significant changes when the Euro 5 emission systems came, followed by Euro 6 in 2014. Truck tare weight increased between 200 and 300 kilograms (400 to 660 pounds). Therefore, Schmidt was looking for a technical solution to having the same payload while not reducing the benefits of the application or the size of the system. The main point was to find out how a 25-tonne (55,115-lb) payload could be realized without exceeding the overall gross combination weight.”
Fleet operations
The Schmidt Group has been serving the dry bulk sector since 1948, hauling a wide range of dry bulk cargoes, including, but not limited to, plastic pellets, cement, lime, starch, powder, sugar, and animal food.
Road tanker operations are conducted from locations in Germany, Belgium, Great Britain, Poland, Romania, Spain, Italy, Austria, Hungary, and the Czech Republic. Shipments are directed through eight regional dispatch centers that are linked to drivers and vehicles by The Schmidt Group’s state-of-the-art Transportation Management System software and the new Astrata telematics System in the trucks.
A significant advantage of the new telematics system is the removable, tablet-based operating unit DriverLinc+, which features an integrated navigation system, several communication applications, presentation of data originating from the digital tachograph in graphic format, as well as driver assistance applications. All drivers can individually select their language of operation. Still to come are improvements, such as remote tachograph data download options, picture capturing of CMR documents with the integrated camera, as well as a digital version of the Schmidt Group driver manual as an application on the tablet.
Many of The Schmidt Group locations have fleet maintenance facilities. Thirteen Schmidt logistic centers are equipped with tank cleaning systems, including drying lanes. Tanks are automatically cleaned under high pressure via spray heads and warm water. Cleaning agents are used as needed.
Schmidt Group runs Mercedes-Benz and Scania cabover tractors, a typical configuration for Europe. Dry bulk silo trailers and intermodal containers are supplied by Spitzer Silo-Fahrzeugwerke GmbH. Most of the silo trailers in the fleet range from 57 to 60 cubic meters (2,012 to 2,118 cubic feet). Silo container capacity ranges from 42 to 56 cubic meters (1,483 to 1,977 cubic feet).
Emission challenges
Hoyer and his team have responsibility for the entire fleet of rolling stock, including ensuring that all vehicles meet the tenets of the various EU diesel-emission directives.
It has been more than two decades now since new European Union (EU) directives began regulating the amount of emissions that on-road diesel-powered trucks can expel into the atmosphere. The first, Euro 1, came into being in 1992, and the EU has now progressed to Euro 6, which governs all trucks that have been manufactured for on-road use in European countries since the beginning of 2014. With that being said, most of the trucks that currently traverse European roads are of the Euro 4 or Euro 5 variety, whose regulations came into effect in 2005 and 2008, respectively.
Specifically, these European Union directives, no matter their stage, put limits on the amount of carbon monoxide (CO), nitrogen oxides (NOx), hydrocarbons (HC) and particulate matter (PM) that can be expelled into the atmosphere through the exhaust of diesel-powered trucks. Over the years, these limits have gotten stricter as the members of the European Union have looked for ways to lower the amount of impurities that find their way into the continent’s air.
For example, in Euro 1 the CO, HC, NOx and PM thresholds were 4.5, 1.1, 8.0 and 0.612 grams per kilowatt hour (g/kWh), respectively. By comparison, the specifics of the Euro 6 regulation place the amount of CO emissions at 1.5 g/kWh, HC at 0.13 g/kWh, NOx at 0.40 g/kWh and PM at 0.01 g/kWh.
These constantly changing emission thresholds have caused truck fleets to reexamine how their vehicles are specified. In addition to new engine models that are designed to reduce emissions, an ancillary consequence regards the actual weight of the vehicle and its payload, both of which are governed by EU regulation.
“Euro 6 is a regulation for limiting exhaust in Europe, and we are really taking care of pollution,” explains Sascha Pachnicke, product manager for Dienstleistung Warenwirtschaft Spedition (DWS) GmbH, Heppen-heim, Germany, since 2006 a distributor of compressor equipment for use on dry-bulk trucks, trailers and silo containers.
“Through these regulations to control exhaust there is less space on the truck left because the exhaust system on a Euro 6 truck is much bigger and heavier than on the Euro 5, for example. The Euro 6 regulation was created to have cleaner air coming out of the exhaust, yet you are only allowed to carry 40 tonnes (88,184 pounds). If the truck is heavier, you have to reduce some of the weight.”
Balancing act
That has created a balancing act for the trucking fleets that transport dry-bulk materials and products across the continent. Specifically, most truck chassis that are outfitted with transport tanks have a maximum weight limit of 14 tonnes (30,864 pounds). Meanwhile, most customers request from their shippers the ability to handle a minimum payload of 25 tonnes (55,115 pounds). Much more than the upper limit of either threshold, and a carrier is bumping up against the 40-tonne (88,184-lb) regulatory ceiling.
The trick, then, is to use a truck and trailer that is as light as possible, allowing it to not only carry at least 25 tonnes, but oftentimes more. This is a benefit for both the end-user, who gets more product shipped at one time, and the shipper, who realizes an economic benefit from being able to ship larger payloads.
To meet the limits Hoyer and his team at The Schmidt Group targeted potential weight reduction in the truck-mounted product compressors that were being used to load and unload the tanks and silo containers. The compressors used by The Schmidt Group were rather complicated to install and maintain, and required a mounting frame and bracket, and special shaft, which added to the overall weight of the system.
As luck would have it, a trip to a trade fair in 2013 led to the discovery of the perfect compressor solution.
“We were attending a trade fair and DWS presented us with the new MH6 technology from Mouvex and Hydrocar,” Hoyer says. “A standard compressor has a weight of around 300 kilograms, but the MH6 has a total weight of 80 to 100 kilograms (177 to 220 pounds), which delivers the required weight savings.”
Specifically, the “MH6” is the MH6 Series Screw Compressor, which Auxerre, France-based Mouvex, part of PSG, a Dover company in Oak Brook Terrace, Illinois, developed in conjunction with Bologna, Italy-based power takeoff (PTO) manufacturer Hydrocar in 2010. The MH6 is an all-in-one screw compressor/PTO unit, and was developed as a weight-saving answer to the new Euro 6 regulations. DWS has been the official distributor for Mouvex equipment in southwest Germany since 2009 and was one of the first companies to put an MH6 compressor in the field.
Less weight
In addition to the upwards of 70% weight reduction offered by the MH6, other operational benefits include the absence of free-turning drive parts, which increase operator safety; no need for additional installation space; no need for separate oil changes since the system is integrated into the truck’s gearbox; no need for mounting brackets and frames, or cardan shafts; quieter operation; and compatibility with a wide array of truck configurations, from 4x2 short wheelbase to larger 6x2 and 6x4 designs. Flow rates range from 325 m3/h to 600 m3/h (85,850 to 158,500 gph), and the MH6 can handle solids up to 15 mm (0.6”) in diameter and 60 mm (2.4”) in length.
The Schmidt Group tested an MH6 compressor on one of its vehicles throughout 2013 and the results spoke for themselves: “At the end of the year, the MH6 showed in the day-to-day testing that what was promised was reached,” says Hoyer. “The conclusion was that during the one year of testing we were very well supported by Mouvex and DWS, and had real communication with our drivers and fleet management on how the MH6 works, and at the end of the day, it was a good relationship and we came to the conclusion that this was the way to move forward, with the MH6.”
The reduced weight of the MH6 also holds ancillary benefits for The Schmidt Group’s fleet drivers. “With the weight benefit, it was possible for Schmidt to increase the size of the cabin, the comfort of the cabin, to give more benefits to the driver to feel more comfortable, more safe for long-distance driving with no risks in using the MH6,” says Hoyer. “It was a target of ours to support the employees and motivate them for the global benefit of the organization and our customers.”
The most successful weight-loss programs are those that target specific areas to trim, then identify the best ways to reach those weight-reduction goals without adversely affecting the whole organism. In that way, the MH6 Series Screw Compressor is the perfect weight-loss solution for dry-bulk haulers like The Schmidt Group.
From his perspective, Hoyer is looking forward to the day when every Schmidt Group truck is outfitted with an MH6 compressor—and has even offered to help Mouvex and Hydrocar field test the next-generation MH Series compressor, the MH10, which is currently in development.
“Schmidt is always looking for the newest technical solution for all of its equipment and because of the capabilities of the MH6 we are proud to work with the Mouvex and DWS organizations,” Hoyer says. “The target is clearly to work with Mouvex in the future, to standardize The Schmidt Group on these compressors.”