Heineken Finds The Perfect Pump For Its Yeast-Food And Hop-Color Dosing Applications At The ’s-Hertogenbosch Brewery In The Form Of Mouvex® SLS Series Eccentric Disc Pumps
Beginning in 1864, when Gerard Adriaan Heineken founded his eponymous brewery in Amsterdam, The NetheHeineken brewery has steadily grown to the point that today the company can confidently claim to be the “world’s most international brewer.”
The facts present a strong foundation for that claim as Heineken currently operates 176 breweries in more than 70 countries and, in addition to its iconic flagship brand, produces more than 250 other international premium, regional, local and specialty beers, including such famous labels as Amstel, Murphy’s, Moretti, Tecate, Tiger and Zywiec. Also, with annual beer production of 181.3 million hectoliters (18.3 billion liters/4.8 billion gallons), Heineken ranks as the third largest brewer in the world based on sales volume, behind Anheuser-Busch InBev and SABMiller.
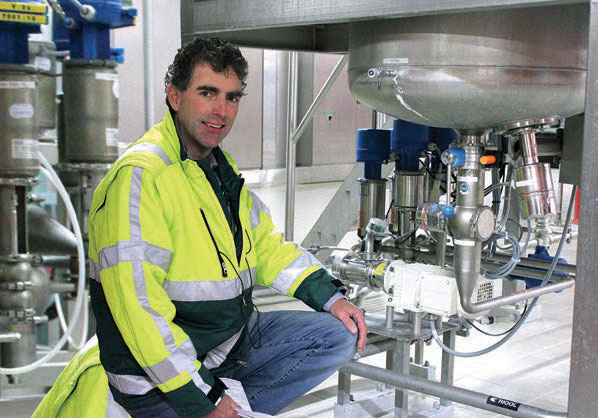
When the Heineken brewery located in ‘s-Hertogenbosch, The Netherlands, began to experience a wide variety of shortcomings in the operation of the gear pumps that were tasked with performing important dosing operations, they knew that they had to find an alternative. Tasked with finding this solution was Rini van Son, the plant’s Senior Mechanical Engineer, and he found the perfect solution in SLS Series Eccentric Disc Pumps from Mouvex®.
In 1991, Heineken halted production at its brewery in Amsterdam and converted the facility into a museum that was renamed the “Heineken Experience” in 2001. Despite that, Heineken currently operates three breweries in The Netherlands, one of which is located in the southern city of ‘s-Hertogenbosch, which is colloquially known as Den Bosch. The sprawling facility currently produces around six million hectoliters (600 million liters/159 million gallons) of beer annually, which is exported to more than 150 countries.
“The malt comes in by boat, is stored in silos, then goes to the brewhouse to the fermentation cellars where it is mixed with hops and water before the yeast is added, and finally is sent to the fermentation room where the beer is created,” explained Rini van Son, the plant’s Senior Mechanical Engineer, who has worked at the facility since 1987. “From the filtration room it goes down to the beer cellar where it is pumped to the fillers in the bottling hall. There, we have six fillers for glass bottles, three canning lines and one keg line. After palletizing it goes out to the world through our own container terminal one kilometer west of the brewery.”
Stuck In First Gear
Ultimately, Heineken is successful because it has struck on a recipe, no matter the brand, that is pleasing to the beer consumer, resulting in loyal customers and repeat sales that keep the brewer thriving. That circle of life, however, is only sustainable if the one-thousandth bottle has the same taste, look and quality as the first. This is why ensuring production consistency is van Son’s No. 1 priority.
A critical stage in guaranteeing product quality takes place in Cellar Block 2. It is there that the yeast-food dosing applications take place. It is in this process that yeast food is blended with fresh “wort,” which is the liquid that is obtained during the brewing process; wort contains the sugars that will be fermented by the yeast food to produce alcohol.
“We prepare the yeast food in two tanks and we dose it through pipelines with a pump, then to the fresh wort lines,” said van Son. “The pump is very important to ensure proportional dosing at this stage; it must run very accurately or the brew will not be to our expected standards.”
For this crucial dosing process, van Son had been using a gear pump, but the performance was not up to his expectations, due to mechanical breakdowns, leaks and the need for excessive cleaning and maintenance becoming more prevalent and problematic.
“The gear pumps had a lot of maintenance, they were not hygienic, not very cleanable and the reliability was bad, so we had to find a much better pump,” said van Son. The search for a solution took van Son to Eddy Louwerens, a Regional Manager with Spin Pompen, an Assen, The Netherlands-based distributor of pumps and related equipment for use in the food and beverage, cosmetic and pharmaceutical industries.
“To make Rini successful we had to select the right pump from the right place and respect the specifications Heineken needed,” said Louwerens. “We talked not only about the actual pumps, but the total process that they were to be used in.”
Brewing Up A Sustainable Solution
Those discussions led Louwerens to one solution: the best pump for van Son and Heineken’s requirements would be the SLS Series Eccentric Disc Pump from Mouvex®, Auxerre, France, which is a product brand of PSG®, a Dover company, Oakbrook Terrace, IL, USA.
The SLS pumps were the best choice because they checked all the right boxes, namely that they are seal-less, highly reliable, volumetrically consistent, easy to clean and require low maintenance. Additionally, they are fully drainable, conforming to the operational tenets of the European Hygienic Engineering & Design Group (EHEDG), which is a consortium of equipment manufacturers, research institutes and public-health authorities that was founded in 1989 to “enable safe food production by providing guidance as an authority on hygienic engineering and design.”
“The Mouvex pumps were chosen, first of all, because they are EHEDG certified, which is a must according to our specifications, and also because they have very good cleanability, require much less maintenance and are very reliable,” said van Son.
Mouvex SLS pumps can deliver these operational advantages because they are constructed without any mechanical seals, packing or a magnetic drive. Instead, they offer a unique seal-less design equipped with a disc and cylinder driven by an eccentric shaft protected by a double stainless-steel bellows that ensures long life and product safety.
Due to the Mouvex pump’s hermetic form the pump can generate very high suction and discharge pressures; this enables the pump to self-prime and fully strip lines, maximizing product recovery reducing product losses and enhancing production capacity. The eccentric disc principle of operation provides consistent, pulse-free and accurate flow rates over an extended period of time, which is critical in dosing applications. It also helps guarantee a low-shear rate.
The pump’s ability to strip lines is especially important to Heineken because they are focusing on the product quality and on a sustainable production processes. The actual cleaning process itself is also easier and kinder with SLS pumps.
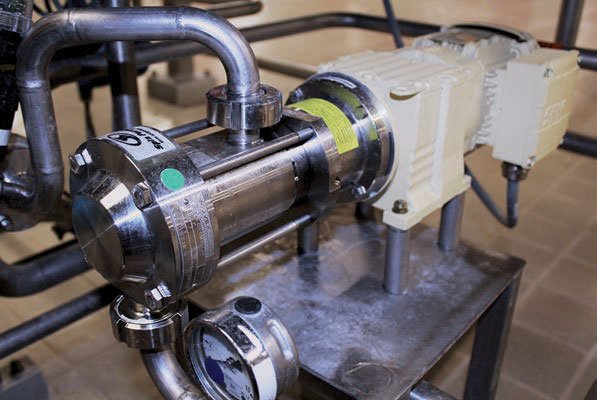
The Mouvex® SLS Series is the pump of choice for the ‘s-Hertogenbosch brewery because they are sealless, highly reliable, volumetrically consistent, easy to clean and require low maintenance.
“During CIP, the rinsing water is transferred through the suction side of the pump, which is not rotating, and transferred to the drain and everything is totally clean,” said van Son. “When cleaning a gear pump, it must rotate very fast in order to get enough flow through the lines and get them clean, which is a very difficult task for the pump.”
As it also turns out, the globally recognized color of its bottles is not the only “green” that Heineken is concerned with.
“Our engineering and production must be as sustainable as possible, that’s our job,” said van Son. “We want to be a green brewery, much greener than we are now, so energy savings are very important. If the pump costs a few euros more, that’s not a problem if it saves energy and resources; that’s important for us.”
That’s another box the Mouvex SLS pumps check because the eccentric disc operating principle is extremely energy-efficient, which results in lower utility costs and a healthier bottom line.
After seeing the SLS pumps in action in Cellar Block 2, van Son has also chosen them for another link in the production chain: the dosing of hop coloring into the beer. The hop coloring gives the beer its bitterness and flavor, and while it has a low viscosity and is easy to pump, it will become very sticky if exposed to air, which makes the SLS pump’s seal-less and airtight operation perfect for the application.
Conclusion
When food-and-beverage companies hit upon a successful recipe or formula they take great pains to ensure that their production processes remain consistent, lest the taste or flavor changes, resulting in disappointed consumers. Over the more than 150 years since its founding, Heineken has stuck with a successful recipe, one that has made it one of the world’s most significant brewers and suppliers of beer. That success is only sustainable if that formula remains consistent, and transfer pumps play a crucial role in maintaining that consistency.
However, when Rini van Son and Heineken began to notice shortcomings in the operation of the gear pumps that were tasked with performing important dosing operations, they knew they had to find an alternative. Working with Spin Pompen, they identified the perfect solution: the SLS Series Eccentric Disc Pump from Mouvex. Incorporating the SLS pumps into the yeast-food and hop-coloring dosing lines at the ‘s-Hertogenbosch brewery has given van Son the confidence that the beers produced there, no matter the brand, will live up to the high taste and quality standards that have been demanded since Gerard Adriaan Heineken entered the brewery business in 1864.
“They had problems with gear pumps breaking down too much, and also with the cleaning,” said Louwerens. “We talked about Mouvex because the pump is seal-less, has constant and accurate flow and EHEDG certification, which for cleaning is the most important part. When you look at the complete package, the Mouvex was the right pump to put in at the brewery and support the company’s green mission!”
For more information on Mouvex or PSG, please go to www.mouvex.com or www.psgdover.com