In fact, considerations regarding health and safety, aesthetics, materials of construction and the atmospheric conditions in which they are used play a prominent role as the access cover has evolved over the years.
Traditional access covers were usually made of metal, but steel covers were found to have a number of inherent drawbacks for the site operator. Among them are:
- Heavy Weight — makes them hard to remove and can lead to site-personnel injuries
- High Maintenance — they will rust and corrode, necessitating the need for repainting, etc.
- Permanent Set — over time the lid deflects and maintains a “bowl shape”
- Slip Hazard — steel covers become very slippery when wet or with ice
An initial solution to these concerns was found in the creation of smaller steel access covers that were easier to handle and maneuver, which resulted in a reduction in injuries. However, in Canada especially, the drawbacks regarding corrosion and expansion remained even with the smaller steel covers. Winter weather conditions require the use of salt to keep the forecourt clear of ice and snow. This results in the inevitable corrosion of the steel, while extreme cold temperatures lead to expansion of steel access covers.
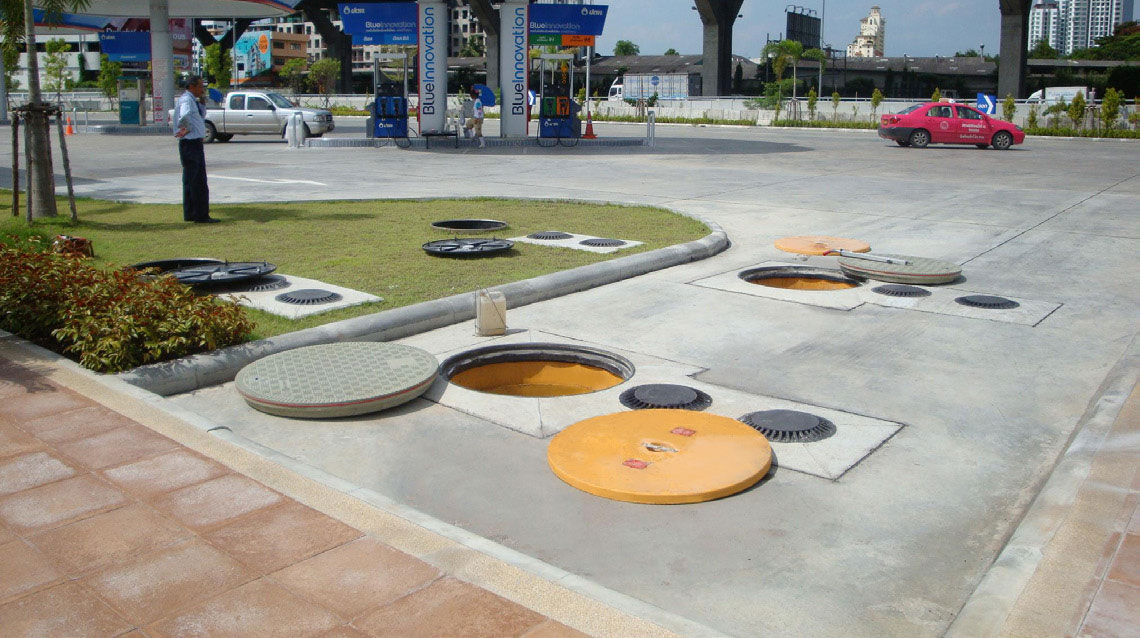
In Canada specifically, composite covers are being used in roughly 70% of forecourt installations and at fueling sites from the country’s southern border all the way to the Arctic Circle.
Acceptance of Composites
Recognizing the shortcomings of steel covers, the industry has experienced growing acceptance of access covers that are constructed of highly engineered glass-reinforced plastic (GRP) composites. These covers weigh only one-third that of its steel counterparts, while maintaining a strength-to-weight ratio that allows them to absorb the abuse that occurs on the forecourt. Also, composite covers don’t corrode when exposed to the elements and have a low coefficient of expansion. Therefore, the shape of composite covers is not affected as weather conditions change. In addition, they can be manufactured in any color that the forecourt operator requires with no need for additional painting or upkeep, which helps achieve consistent branding at the site. Non-slip materials and tread patterns can be molded into the cover to resist slipping of people or skidding of vehicle tires.
Composite covers were an immediate hit with operators in the petroleum- and convenience-retailing industries. Almost 90% of large diameter covers (those 36 inches and up) found on the forecourt are now made of composite materials, with more than half of all other access covers constructed of composites. In Canada specifically, composite covers are being used in roughly 70% of forecourt installations and at fueling sites from the country’s southern border all the way to the Arctic Circle.
Continued Improvements
A noteworthy advancement in recent years in the design of the access cover and spill containment has been the addition of composite materials to the multiport system. A multiport system has two small composite spill containment covers located on a larger composite cover. The smaller covers can be removed in seconds, which allows easy access and quick connection of hoses to fuel-delivery and vapor-recovery piping. Water intrusion was a big issue with the original steel multiport designs. Composite multiport systems are engineered to prevent water intrusion into the fueling system, which is a critical consideration for the operators of retail and commercial fuel sites.
About the author:
Ed Kammerer is the Director of Global Product Management for OPW, based in Cincinnati, OH, USA. He can be reached at ed.kammerer@opwglobal.com. OPW is leading the way in fueling solutions and innovations worldwide. OPW delivers product excellence and the most comprehensive line of fueling equipment and services to retail and commercial fueling operations around the globe. For more information on OPW, please go to www.opwglobal.com.