By Bobby Hayes
Compliance management is becoming increasingly demanding for today’s retail and commercial fuel site operators as regulatory agencies continue to implement more stringent compliance requirements. For instance, the U.S. Environmental Protection Agency recently revised its underground storage tank regulations, adding secondary containment, maintenance, operation and training stipulations. Failure to meet compliance regulations such as these can be extremely costly; EPA penalties for UST violations can reach up to $37,500 per day of noncompliance.
However, maintaining site compliance isn’t necessarily cheap or easy. Installing new monitoring equipment can result in undue downtime and significant installation costs. As the regulations become stricter, U.S. fuel site operators need to implement fuel monitoring systems that will provide cost-effective compliance monitoring now and flexibility for the future. Fortunately, innovations in tank monitoring equipment and infrastructure can simplify new installations and reduce installation costs.
Wiring is Expensive
Most tank gauges require monitoring devices such as probes and sensors to be installed on individual, separate wires. This type of wiring configuration is both inefficient and expensive because it requires a high number of “home runs” to be wired back to the tank gauge. The higher the number of home runs that are needed, the more wire and time that are required to complete a new tank gauge installation.
For example, a fuel site with four dispensers and three storage tanks that uses a conventional wiring configuration is likely to need 10 or more home run cables back to the tank gauge. Advancements in tank monitoring technologies make this no longer necessary. Today, there are tank gauges on the market that support a streamlined wiring configuration, which significantly lowers the amount of cable needed for installation — in some cases reducing the number of home runs to just two or three. This reduction in home runs decreases the amount of wire needed by hundreds of feet. Older tank gauging systems and wiring configurations also waste a larger amount of the wire purchased. That’s because, for almost every spool of wiring purchased for a fuel site monitoring system, there is a length of wire at the end of the spool that cannot be used at installation. Spools are available in lengths of 500 feet and 1,000 feet of wire. Runs can often be 150 feet to 200 feet in length. As a result, there are often extra 100- to 200-foot lengths of wire remaining at the end of spools that cannot be used for home runs. The more spools the installation requires the more wire that is wasted.
Fortunately, advancements in tank monitoring technologies make inefficient wiring configurations no longer necessary. Today, there are tank gauges on the market that support a streamlined wiring configuration, which significantly lowers the amount of cable needed for installation – in some cases reducing the number of home runs to just two or three. This reduction in home runs can decrease the amount of wire needed by hundreds of feet.
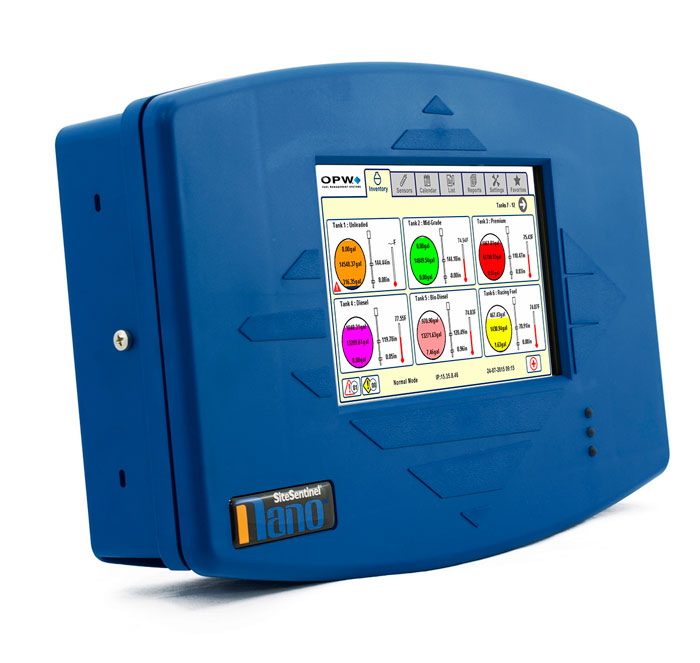
Some equipment manufacturers, such as OPW Fuel Management Systems, have engineered efficient wiring configurations for their tank gauges.
Tank Monitoring Solutions That Reduce Costs
Manufacturers of fuel management equipment recognize that fuel site operators face numerous challenges when it comes to managing their storage tank environments, including rising operating costs and changing compliance requirements. To help fuel site managers maximize their equipment investments and simplify compliance management, manufacturers are engineering tank monitoring solutions that not only provide state-of-the-art compliance monitoring, they also minimize the site downtime that occurs during typical installation and equipment upgrades. Fuel management equipment manufacturers are also designing tank monitoring systems with flexibility in mind, so fuel site managers can more easily – and cost-effectively – adapt their systems to changing compliance requirements.
For example, there are tank monitoring solutions on the market that pair a cost-saving tank gauge with an innovative wiring configuration that allows probes and sensors to be run back to the gauge on the same wire. Recent advancements to this technology now enable multiple probes and sensors to be mixed and matched on the same wire, which significantly reduces the amount of wire needed for a new tank gauge installation.
For a fuel site with three tanks and four dispensers, a tank monitoring system that permits an efficient wiring installation can reduce the amount of wire needed for installation can reduce the amount of wire needed for installation by as much as 60-70 percent. At smaller sites, the wiring technology can enable a number of home runs to be pared to just two or three runs. By using a tank monitoring system that supports a lean wiring configuration, a 3-tank 4-dispenser site could initially install three tank probes, three STP sump/annular sensors, four dispenser pan sensors and plan for additional tank monitoring sensors and dispenser pan sensors to be added in the future (in the event the site needs to expand its monitoring capabilities).
And it’s not just the amount of wiring that is reduced – the amount of wire that is purchases but ultimately goes unused and the amount of conduit needed for installation are also reduced. Fuel site operators can save between 45 and 55 percent on these infrastructure costs by installing a tank gauge that supports an efficient wiring configuration.
Although modern tank gauges are being engineered with efficiency in mind, it doesn’t mean they are sacrificing functionality for efficiency. In fact, today’s tank monitoring systems offer feature sets that are more powerful than their predecessors. These features include remote management, user-friendly compliance management tools and comprehensive report packages. All of these tools help fuel site managers streamline their daily compliance procedures.
While there is a degree of nuance involved with installing a tank monitoring system for the particular needs of each site’s application, the fundamental financial challenges associated with an installation remain fairly ubiquitous. A fuel site that is wired with efficiency in mind can realize substantial installation cost savings through reduced labor and wiring expenses. Compared to older model gauges that don’t support a lean wiring configuration, today’s state-of-the-art consoles can save U.S. fuel sites an average of 50-60 percent on installation costs. Consult with a qualified fuel equipment representative to review installation costs for your site and to identify potential cost-saving technologies that will likely reduce your capital expenditures.
Prepare for Future Compliance Needs Now
While investing in cost-saving technology innovations is certainly one way that fuel sites can reduce their expenses, investing in equipment that supports an upgrade path effectively increases the service life of that equipment. In many cases, this flexibility enables both existing and new fuel sites to comply with evolving environmental regulations for years to come.
For instance, fuel sites that currently have a SiteSentinel® iTouch™ tank gauge from OPW installed at their site can upgrade to OPW’s Nano tank gauge, add IntelliSense modules to their existing sensors and multi-drop monitoring devices on the home-run wiring that was originally installed with the iTouch. This approach provides many benefits to fuel site managers: a Nano upgrade can be achieved with minimal disruption to operations, the upgrade path preserves their investment in their original home-run wired sensors and it allows operators to install different monitoring devices on the same wire. By upgrading the console, more devices may be installed within the original wiring framework.
In this era of evolving environmental compliance, fuel site operators can expect that regulations will expand and become increasingly strict. Fuel site managers need to position their operations to meet today’s compliance needs as well as those of the future. Deploying tank-monitoring solutions — such as OPW’s Nano and Mixed Multi-drop Technology — that are engineered to streamline compliance management, reduce installation costs and provide flexibility for changing needs is a cost-effective approach. Fuel sites that align their operation with an equipment manufacturer who is vested in these needs will find themselves leveraging their equipment investment over the long-term, ensuring they are optimized to meet compliance requirements for years to come.
About the Author:
Bobby Hayes is the Domestic Sales Manager at OPW Fuel Management Systems in Hodgkins, IL. He can be reached at (770) 605-9611 or robert.hayes@opwglobal.com. OPW is a global leader in fully integrated fluid handling, management, monitoring and control solutions for the safe and efficient handling of critical petroleum-derived fluids from the refinery to the commercial and retail points of consumption. OPW is an operating company within the Fluids segment of Dover Corporation. For more information about OPW, please visit www.opwglobal.com.