By Ed Kammerer
We will now have a reading from the First Book of Retail Fuel Storage and Dispensing: “In the beginning, there was steel….” Specifically, more than 100 years ago, and for most of the ensuing century, steel was the only material used (admittedly, because there really wasn’t another viable alternative) to construct the storage tanks, piping, containment units, valves and most other components that were integral cogs in commercial and retail refueling systems.
That began to change when it became apparent that hydrocarbons coupled with the underground environment had a corrosive effect on steel, while the bumps and bruises that underground steel storage, transfer and containment equipment would be subjected to over many years of service could also lead to environmentally harmful fuel leaks, many of which could go undetected for decades.
Rising to the Challenge
Prompted by the need to create better fuel-storage and transfer equipment, much of which was driven by regulatory mandates in the United States and Canada, the incredibly intelligent and talented men and women who work for the equipment manufacturers put on their thinking caps and went back to their drawing boards. The result was a dizzying array of innovations that simultaneously made fuel storage and dispensing environmentally safer and the equipment used to conduct the process more cost-effective to install, operate and maintain.
Looking in particular at fuel-transfer piping, the improvements came fast and furious. Steel begat fiberglass, which was non-corroding and durable, with a seemingly limitless life span. But while fiberglass eliminated corrosion problems, fiberglass piping was still required to be buried underground with glued joints where one piece of pipe was connected to another. These buried joints soon became problematic.
That begat the next innovation – corrosion-free flexible pipe that could be used as part of an integrated fuel-transfer system without requiring rigid connection points. These integrated “loop” systems were specially designed to place all of the valves, fittings and pipe connections within a polyethylene or fiberglass box (dispenser sump) that was accessible from grade level at the fueling site, eliminating the need to break concrete if the system needed maintenance or repair. The final step in this evolution of a retractable piping system contained between two sumps was in the dispenser sump itself. This change occurred when the dispenser sump was made “conduit-less.” Conduits could be run outside the sump and into the frame of the dispenser, eliminating the need to drill holes in the sump for electrical conduit entry fittings. This practice solved multiple water-intrusion issues inside the dispenser sump.
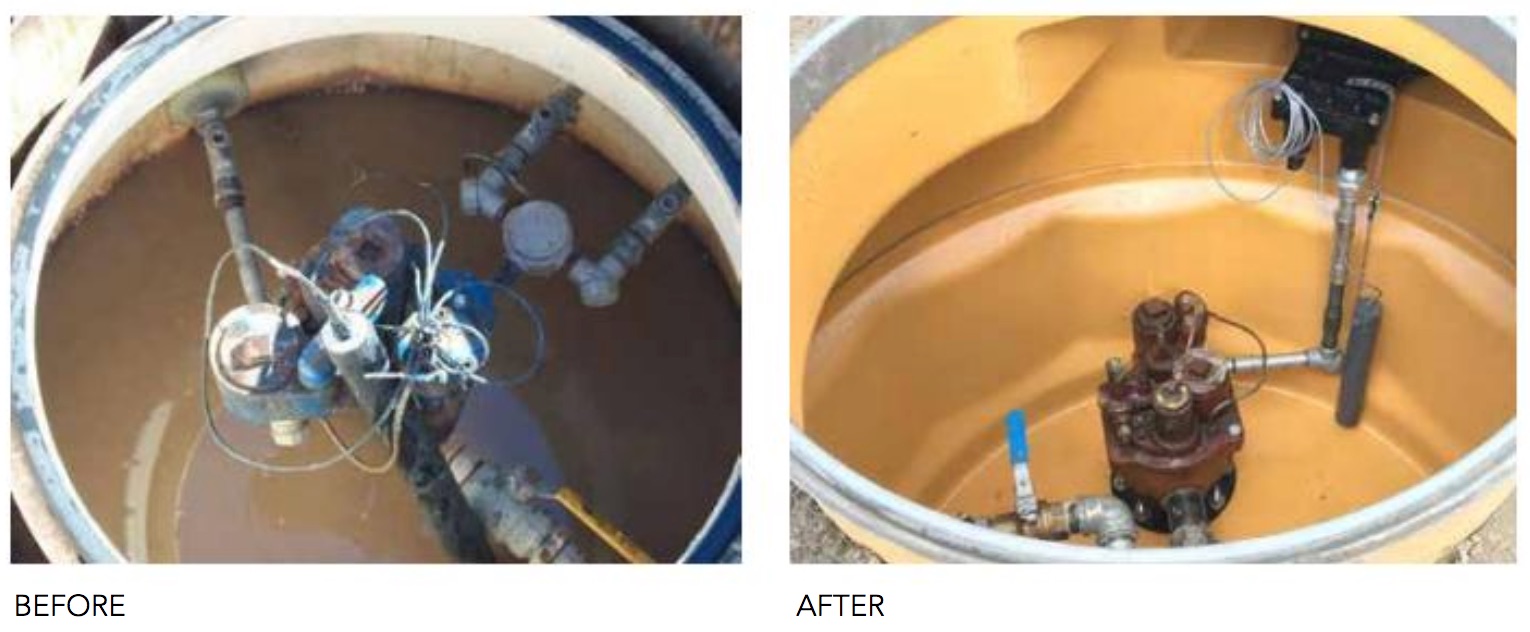
“Tanks” for the Memories
The improvements in fuel-storage and transfer systems and components also set the stage for the development of new pieces of equipment. Chief among them was the submersible transfer pump, or STP. The earliest STPs were mounted on the tank and simply buried under backfill, which made accessing them and their components problematic as there was no easy access path for the operator. This practice also allowed fuel to leak directly into the environment.
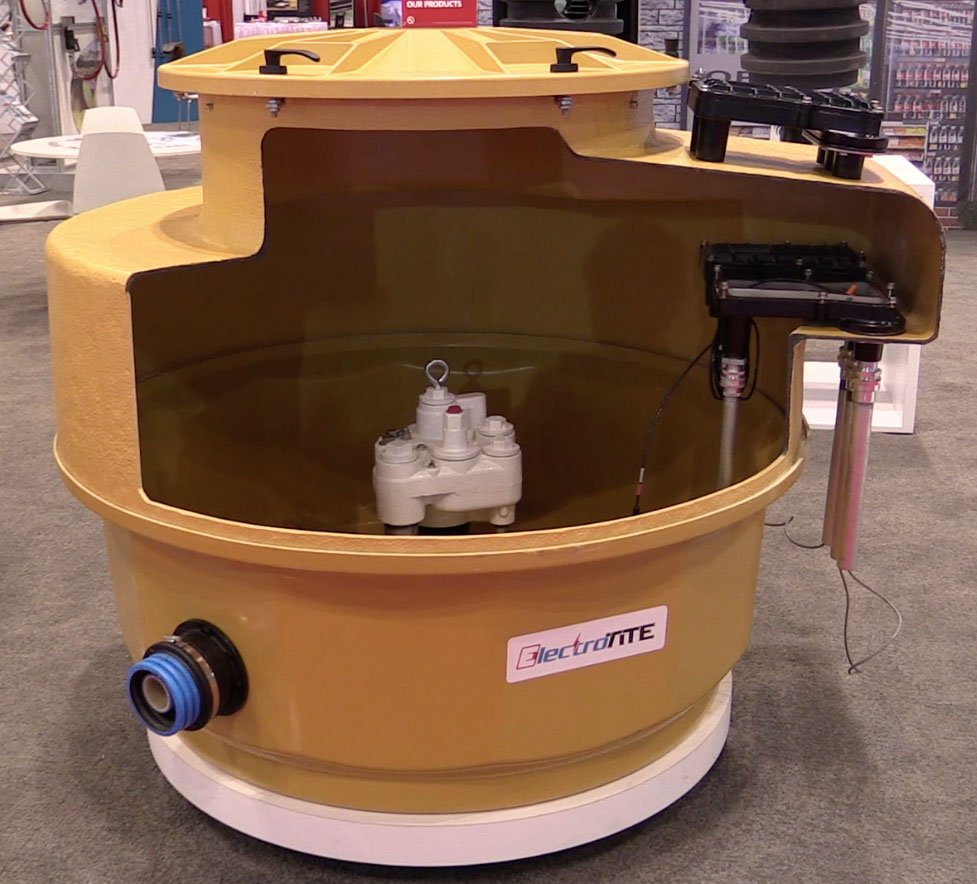
The new ElectroTite sump features an integrated electrical junction box that no longer requires contractors to cut holes in the sump and fabricate field installed electrical conduit penetrations.
The initial means to gain access to an STP was to simply create a barrier from the backfill with wood or steel. The pump itself was placed in an open-bottom box that was surrounded by the backfill. Then, the need to capture fuel leaks and allow the operator easier access to the STP and its components eventually prompted the development of the tank sump, which would function as a liquid-tight isolation and secondary-containment unit that would provide a convenient means for housing a multitude of piping connections, tank fittings, valves and submersible pumps. This has led to the development of the corrosion-resistant polyethylene and fiberglass tank sumps with which we have become familiar.
Realizing that there was still more ground to be plowed in the evolution of tank sumps, the industry’s engineers continued to push the evolutionary envelope. That brings us to the stage where we find ourselves now, what many may call the “final frontier” in tank-sump development. Even though these shiny poly and fiberglass sumps can completely contain fuel and keep water out when they leave the factory, as soon as they show up on a job site, they are immediately compromised by the electricians who drill holes in them to allow electrical conduit penetrations. These non-watertight conduits and entry fittings are notorious leak points.
Hence the search for the Unicorn or the Holy Grail of petroleum containment: “The Conduit-less Tank Sump…” Well, folks, the search has ended. OPW has developed the latest in tank-sump innovation by offering the industry’s first entirely conduit-less tank sump. The new ElectroTite sump features an integrated electrical junction box that no longer requires contractors to cut holes in the sump and fabricate field-installed electrical conduit penetrations. The factory-installed, UL-listed, explosion-proof junction box allows electricians to use a single component for conduit seal-offs and wire connections for both high voltage and communication wires. The result eliminates multiple unnecessary leak points at installation and creates a tank sump that will not be susceptible to any type of fuel leakage or water intrusion, which provides the highest level of protection ever for both the fueling system’s components and the environment. The new ElectroTite sump will provide a maintenance-free and environmentally sound system for many years below ground.
About the Author:
Ed Kammerer is the Director of Global Product Management for OPW, based in Cincinnati, OH, USA. He can be reached at ed.kammerer@opwglobal.com. For 125 years, OPW has been leading the way in fueling solutions and innovations worldwide. OPW delivers product excellence and the most comprehensive line of fueling equipment and services to retail and commercial fueling operations around the globe. For more information on OPW, please go to www.OPWGlobal.com.