By Glenn Webb
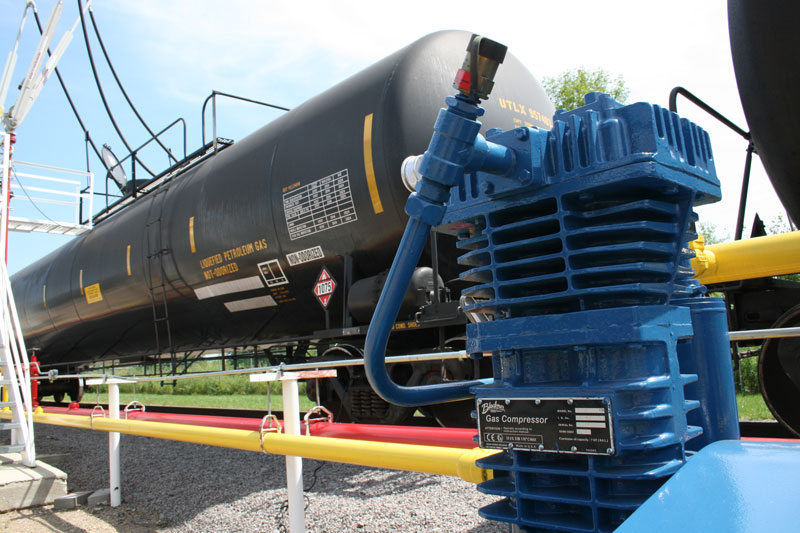
Oil-free reciprocating piston compressor technology is just like any other. It only achieves its desired affect if it is utilised in the proper applications and, then, only after the proper amount of consideration and study has been performed before the final technology choice is made. In other words, making assumptions based solely on past experience can lead to adverse consequences.
In order to ease the process of selecting the proper gas-handling compressor technology, this article will provide a general roadmap that can be used by the end user to identify and select the proper solution for every unique application.
Assess The Application
The first job of the application engineer when creating a compressor-based system for industrial gases — which can literally mean anything from ammonia to vinyl chloride — is pondering the most apparent question: Is it even a compressor application? Only after the parameters of the operation are established will the engineer know if a compressor is an appropriate technology for use in the process.
In general, there are three product-transfer-based applications that are ideal for compressors:
Vapour Recovery: Involves the capture of gases that remain in a storage vessel that would typically be vented to the atmosphere. Today, these gases must be recovered due to stricter environmental and safety regulations, or economic considerations since fugitive gases can be quite valuable.
Pressure Boosting: Consists of moving a gas from one location to another. Compressors excel in the pressure-boosting process because they can handle a wide range of pressure-boosting conditions.
Liquefied Gas Transfer: Generally takes place during the loading, unloading or transloading of railcars and can involve both liquid-transfer and vapour-recovery applications.
Contemplate The Conditions
Once the actual process is identified, the application conditions must be determined. In addition to gathering general information like the site location and elevation, and whether the equipment is located indoors or outdoors and stationary or mobile, a Data Sheet can be used to ask the end user for more specific operational parameters, which can include:
- Required inlet and discharge pressures and temperatures
- Ambient temperature range
- Atmospheric pressure (determined by the site elevation)
- Electrical-area classifications, such as NEMA 1, 4, 7, 9 or 13
- Operational noise levels that can be allowed (specified by a maximum decibel level)
- A gas analysis of the product being handled (including the molecular weight and molar percentage of the gas or liquid product(s) being handled)
- Required flow capacity
- Number of production cycles per day, knowing that high-duty cycles will require the compressor to run continuously, or on some type of load/unload cycle
- On-and-off cycle times and their duration/frequency
- Types of control switches
- What safety switches and alarms are required to protect the equipment and the process
Once these operational parameters are compiled, the application engineer can initiate the process of selecting the proper compressor for the operation. As mentioned, though, this does not mean that there is a one-size-fits-all solution available. It pays to reiterate that every compressor-model design has very concrete limits on what its operational capabilities are.
Narrowing The Focus
Let’s take a moment to survey the compressor field. While the focus here is reciprocating piston compressor technology, there are many other options for the operator to consider. Reciprocating piston compressors are positive displacement machines, as are their diaphragm cousins. There are also positive displacement rotary compressors, such as the vane, screw, liquid ring and blower types. Finally, there are axial or radial turbo compressors.
Another significant factor to consider is cost. Reciprocating piston compressors are among the most cost-effective technologies available to the market. That being said, the operation’s process parameters will play a role in the final cost of the equipment. For instance, machines that must meet API-618 design requirements will have a higher purchase price than a non-API-618 design.
Within the family of reciprocating piston compressors there are oil-free, non-lube, lubricated and oil-less designs. The transfer of crude natural gas may not require an oil-free compressor because there are already impurities in the gas itself so that any small amounts of oil carryover from the compressor will not harm the product or the process. Emission-compliance requirements, however, could mean that an oil-free design could be the best solution due to its leak-control capabilities. An oil-free machine will usually be required if the purity of the customer’s process gas must not be compromised by the compressor.
A recent environmental consideration is the new fugitive-emissions requirements that demand more comprehensive leakage control. Some lubricated compressor designs do not have a gas-sealing section (distance piece), which makes them prone to significantly higher leakage rates.
Finally, oil-free designs have very specific discharge-temperature limitations. Since the top end of the machine is designed to operate without lubrication it has non-metallic wear parts (e.g., piston rings, packing seals, etc.) that become sacrificial wear parts. By design, those parts will need to be serviced and replaced on a regular basis.
Conclusion
Reciprocating piston compressors are only effective if they are put in a position to be successful. Ideal compressor operation can be attainable by asking the right questions, performing the required research and working closely with the customer and other channel partners. If all of these steps are completed successfully, compressor selection will result in optimised operations and contented clients.
About the Author:
Glenn Webb is the Business Development Manager — Blackmer Compressors for Blackmer® and PSG®. He can be reached at glenn.webb@psgdover.com. For more information on Blackmer’s full line of pumps and compressors, please go to blackmer.com or call (616) 241-1611. Blackmer is a product brand of PSG®, a Dover company, Oakbrook Terrace, IL, USA. PSG is comprised of several of the world’s leading pump brands, including Abaque®, Almatec®, Blackmer®, Ebsray®, EnviroGear®, Finder, Griswold™, Mouvex®, Neptune™, Quattroflow™, RedScrew™ and Wilden®. You can find more information about PSG at psgdover.com.