By: Paul Hakamaki, Vice President of Quality for
CPC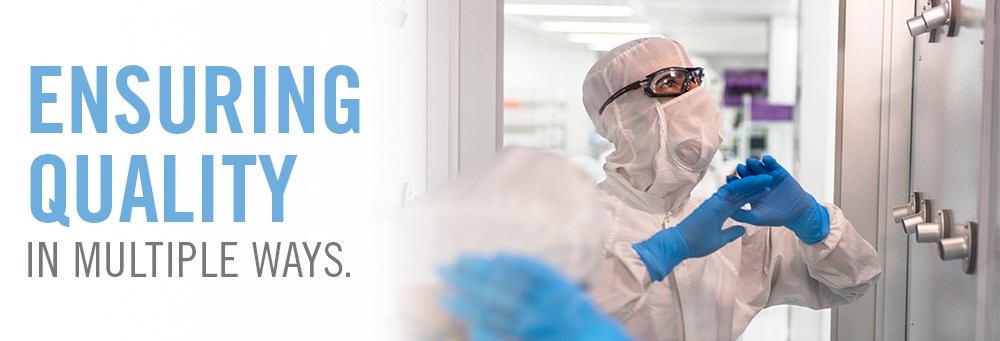
Quality is a word you hear often. In fact, you probably hear it so often, that it has lost its impact and meaning. So when we say CPC is laser-focused on quality, we want to provide you with tangible evidence, not just promises.
At CPC, quality isn’t a one-time thing, it’s a never ending process. That’s why we are ISO 9001 and ISO 13485 certified. These two quality management system standards formalize the way CPC structures its planning, processes, resources and records to ensure we meet our strict quality objectives. By specifying the requirements for good quality management practices, there is a high probability that product and service quality goals will be achieved.
Before we go any further, let’s take a look at the differences between the two ISO standards. ISO 9001 applies to numerous industries and is considered the general requirements for a quality system. ISO 13845 incorporates the majority of ISO 9001 requirements and adds additional requirements that are important to manufacturers of medical devices, who are very concerned about quality and reliability. All CPC products adhere to both ISO standards.
Another way to think about ISO standards is to think of them as building codes. Much like homebuilders all work to meet their required codes, ISO-compliance means we work to meet the required codes for building our products.
And even though the process for becoming ISO 13845 certified is demanding, the end result is pretty simple: You can rest assured that the CPC product you purchase will be up to the challenge of your application.
In addition to ISO 13845, we have a rigorous inspections program. Our 12 inspectors ensure that parts and materials received from our suppliers meet their exact specifications. We work primarily with ISO-certified suppliers because we want quality all the way through our supply chain. On the assembly floor, we have finished parts inspectors to provide final assurance of quality.
We also have a seasoned team of Quality Engineers. They are divided into three areas of expertise:
- New Products: These Quality Engineers work hand-in-hand with the design engineers to ensure that quality is a key consideration in every new product.
- Production: Another group of Quality Engineers support the production floor—making sure that the ISO requirements are adhered to at every step.
- Suppliers: A separate set of Quality Engineers work with our suppliers to help them understand the quality expectations we have regarding their product.
Our dedication to quality extends to our equipment and assembly facility. We have a ISO Class 7 cleanroom where we assemble many of our connectors and couplings. This cleanroom features a highly sensitive particulate monitor, and to ensure sterility throughout the manufacturing process, our suppliers also manufacture within cleanrooms—meaning our parts are never exposed to unfiltered air.
As Vice President of Quality, my focus is on continuous quality improvement. I have a background in quality assurance for medical device manufacturing and supply chain quality that should be an asset as we work toward providing our customers with the best performing, highest quality couplings and connectors.
At CPC, quality isn’t just a word. It’s a passion. And the focus of every employee, every day.