Source: Dover's
SWEP Vestforbraending is one of the largest waste management companies in Northern Europe. The company owns and operates a combined heat and power producing waste-to-energy plant with an annual capacity of 600,000 tons of waste. All the heat produced is utilized as the plant is interconnected with the regional district heating system in Copenhagen, Denmark.
SWEP, a word leader in the manufacturer of brazed plate heat exchangers ("BPHE"), has been closely involved in this project and has provided eight fully loaded B649 BPHE units in parallel design, meaning four lines with 2 x B649 in series with the maximum number of plates shown in the illustration.
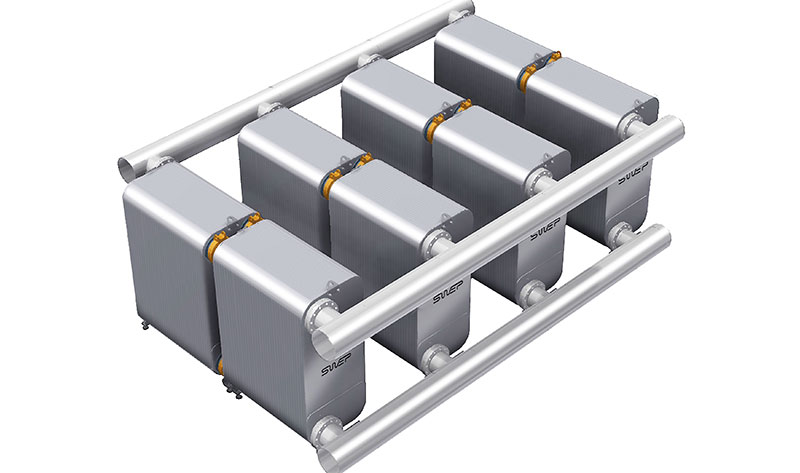
The units normally run with 1-2 lines in operation, but can take a full load of up to 51 megawatts with all four lines in operations. The units transfer heat from Vestforbraending I/S to Lyngby Kraftvärme A/S for distribution, via the storage tank, into the DTU – Danish Technology Institute – area. It is also possible to run the system in reverse mode, meaning that Lyngby Kraftvärme is able to sell surplus energy back to Vestforbraending I/S.
Of the energy produced from waste incineration at Vestforbrænding, 80% is turned into district heating and 20% becomes power. District heating generated through incineration of waste causes much lower CO2 emissions than most other heating forms.
In the time since the market was shared between natural gas and district heating 30 years ago, many assumptions have changed. There is now much more energy from waste and saving CO2 emissions is of high priority. Therefore, Vestforbraending asked Ramboll to prepare a heat plan strategy to identify a low-cost solution for Vestforbrænding and for the Danish society. The strategy showed that it would be very profitable to replace large natural gas boilers with district heating, in total around a 350,000 MWh/year increase. The profitability of the project for Vestforbræding corresponds to an internal rate of return of more than 20%, which is far more than the loan interest rate of around 4%.
Ramboll’s aim was to design a system that provides the most efficient and environmentally friendly energy solution. SWEP BPHEs were a sound choice for inclusion in the project. As well as being very cost-effective thanks to their high efficiency and very small footprint, they also minimize the use of raw materials whose extraction and processing have a high environmental impact.