The integral-piston design has created a new class of diaphragms that can satisfy traditional flow-rate, suction-lift and efficiency demands while eliminating abrasion-related damage.
By Erik Solfelt, Diaphragm Pump Product Manager at Wilden and PSG
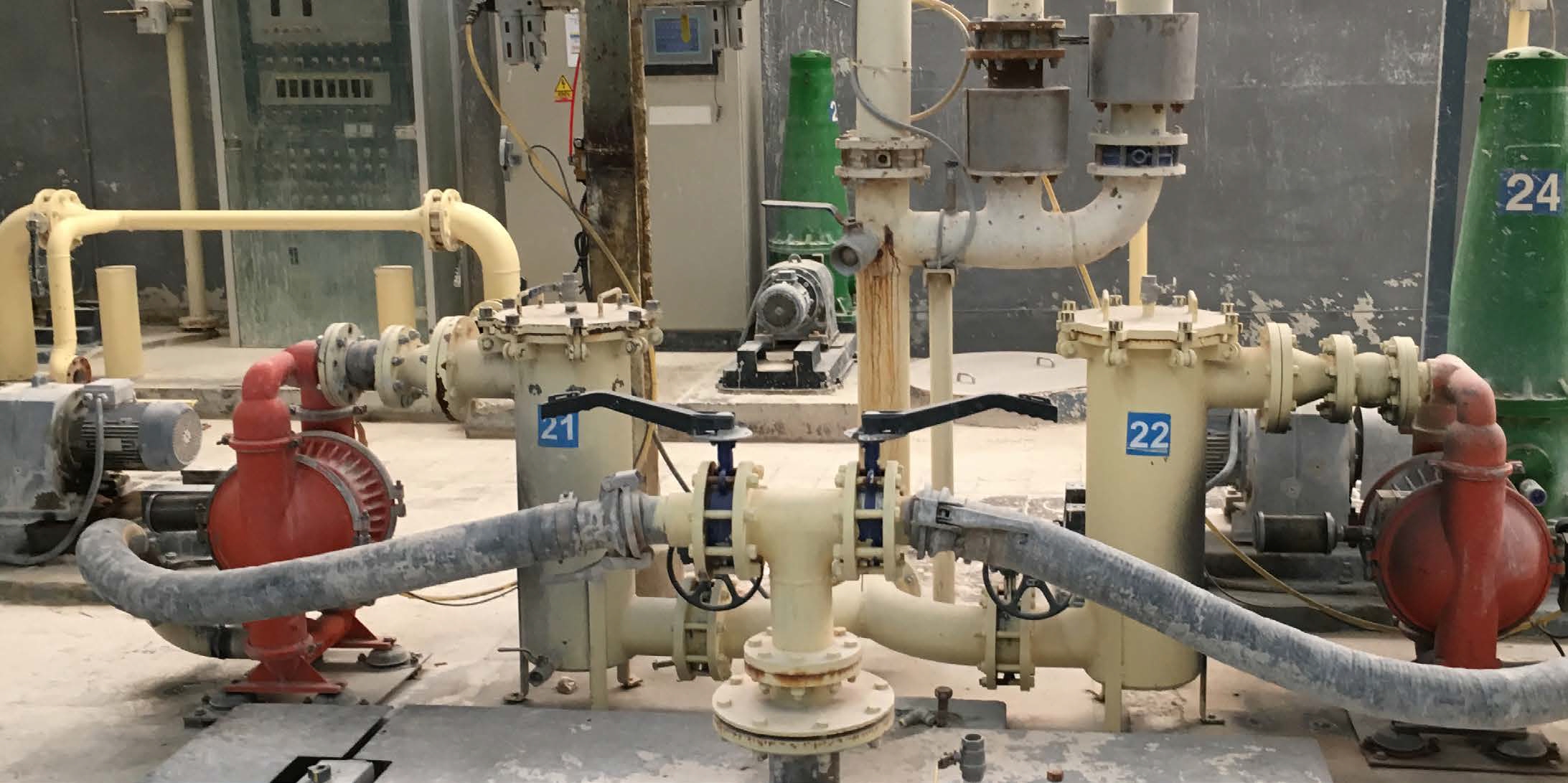
The constant motion that the diaphragms in an air-operated double-diaphragm (AODD) pump are in during a fluid-transfer operation operation puts them at risk of degradation and breakdown. However, a new integral piston diaphragm (IPD) design protects the diaphragm from failure while still delivering expected flow rates, efficiency, consistency, abrasion resistance and operational safety.
Introduction
When determining the level of performance of air-operated double-diaphragm (AODD) pumps, choosing the correct air motor is generally the most important choice the user will have to make. Also significant, however, is selecting the right type of diaphragm, the operation and reliability of which will directly impact the pump’s mean time between failure (MTBF), application safety, and operational efficiency and consistency. As the parts that are constantly in motion during an AODD pump’s operation – with any breakdowns or failures resulting in undeniably costly and oftentimes hazardous product leaks – careful consideration must be taken in regard to diaphragm selection.
A number of factors must be considered before the optimum diaphragm can be selected for a specific application. Previous experience can always assist the operator in making this selection, but new or different applications will require research and may warrant the use of third-party assistance in order to determine which diaphragm will most successfully meet the application’s specific requirements and parameters.
When selecting a diaphragm, there are usually seven primary factors to consider:
• Abrasion Resistance – ability to withstand wear and friction from contact with solids and particles in the fluid being pumped
• Chemical Resistance – material compatibility with the fluid being pumped
• Temperature Ranges – capability to remain flexible in low temperatures and not deteriorate in high temperatures
• Sanitary Standards – requirements that the diaphragm comply with hygienic or sanitary standards
• Inlet Condition – capacity to pump fluid from one location to another
• Flex Life – expected longevity of the diaphragm before requiring replacement
• Cost – total cost of ownership determined by multiple factors, such as initial price, rated flex life for the application, and costs of downtime and diaphragm replacement labor
To help manufacturers become more familiar with the various materials of diaphragm construction and find the best diaphragm for their operations, Wilden® has produced a
technical article that addresses these areas in-depth.
Over the years, it had become apparent to leading AODD manufacturers that improved diaphragm design was the next frontier in relation to better, more reliable pump performance. Driven by the belief that a better diaphragm could be developed, diaphragm manufacturers have discovered better ways to build diaphragms and make it easier to satisfy their operational demands.
Concerns With Traditional Inner/Outer Piston Design
One diaphragm designer in particular – Wilden® Pump & Engineering Co. – determined that the foundational fault in traditional diaphragm design revolved around the inherent operational shortcomings of diaphragms that featured an outer-piston design. The inner and outer diaphragm pistons, often refereed to as plates, provide a means to connect the diaphragms to the reciprocating common shaft and to seal the liquid side from the air side of the diaphragm. While outer-piston diaphragms will perform admirably in many common applications these types of diaphragms have some very worrying performance characteristics.
Most significantly, the outer-piston abrasion that will occur during normal operation will eventually lead to the creation of a potential leak point. Abrasion caused by contact between the outer piston and the diaphragm is an unavoidable by-product of operation of this type of diaphragm. Abrasion is exacerbated by the presence of abrasive particles in the fluid stream that can be trapped between the piston and the diaphragm. In many cases, this abrasive wear is the primary cause of diaphragm failure, regardless of diaphragm material. This is not only expensive from lost product, maintenance and replacement perspectives, but also from a hazard standpoint if the pump is handling harmful or dangerous liquids.
The design of outer-piston diaphragms also can lead to the buildup of the pumped fluid, especially if it's an abrasive. In this case, the abrasive substance can collect on the outer piston because standard diaphragms have flat outer pistons that feature pockets or areas where abrasive-type fluids can nest or be trapped. Another potential problem can occur when the thickness of the material buildup’s “skin” reaches a certain level and it shears off during the pumping process. Any buildup that enters the fluid stream possesses the capability to damage the pump or get stuck in the production system, which can lead to debilitating breakdowns, downtime and repair/replacement costs.
Taking into account the problems that abrasion wear and material buildup can cause, the industry worked diligently to develop the integral piston diaphragm, or IPD. Within the IPD design, the piston that is used to move the diaphragm laterally during the pumping stroke is encapsulated into the interior of the diaphragm itself. IPDs also have a smooth finish with an angle of operation that enhances fluid flow and suction lift while reducing the propensity for material buildup on the outer piston.
The Next Generation Of Diaphragms
While Wilden did not invent the IPD, its engineers have been able to develop a unique IPD design that uses the same hardware as standard full-stroke diaphragms, which means there is no tradeoff in performance when using a Wilden IPD, something that can’t be said for other IPD-diaphragm designs
(see illustration below).
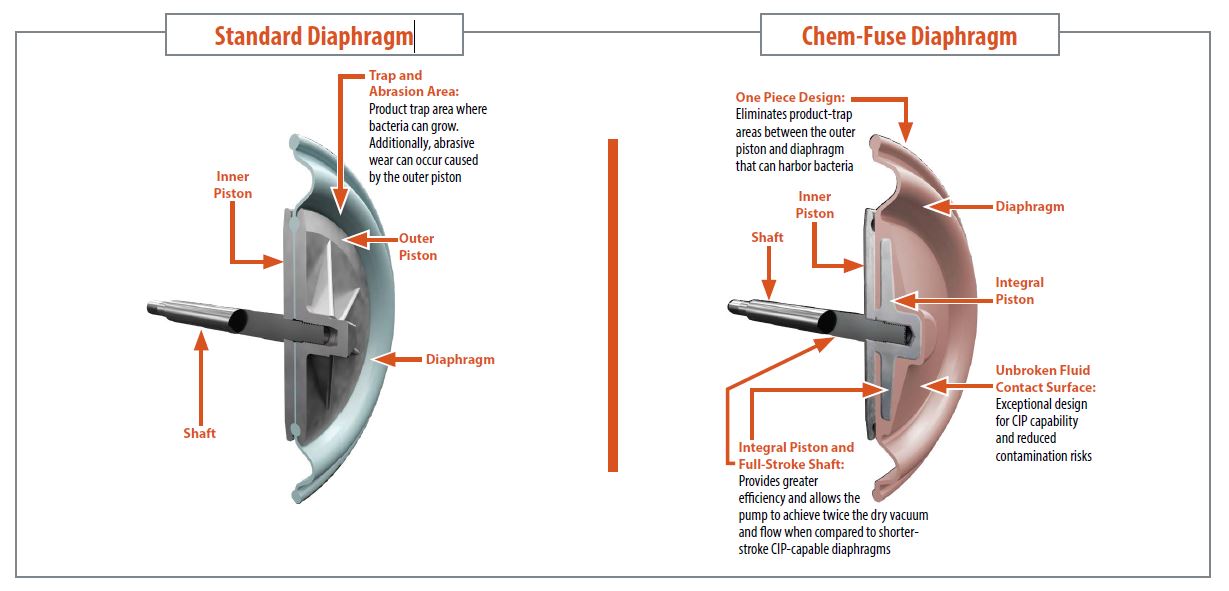
Specifically, Wilden has designed two new models of IPDs, both of which can achieve a traditional stroke length that will optimize flow rates, suction lift and efficiency.
Wilden’s Chem-Fuse Diaphragms deliver an elevated level of pumping performance, which makes them ideal for high volume chemical and industrial liquid-handling applications. Most significantly, elimination of the potential leak point at the outer piston makes Chem-Fuse diaphragms the best choice when the application involves the transfer of critical, dangerous or hazardous liquids.
Additional features of Chem-Fuse diaphragms include:
• Elimination of outer piston abrasion for longer diaphragm life, especially when pumping abrasive fluids
• Easy cleanability for faster changeovers between product
• Up to 100% increased flow and suction lift compared to other reduced-stroke IPD diaphragms
• Wil-Flex construction, which makes them 50% less expensive than PTFE-laminate diaphragms
• Compatibility with Pro-Flo® SHIFT bolted metal and plastic pump models
• Size availability from 25 mm (1"), 38 mm (1.5"), 51 mm (2") and 76 mm (3")
• Temperature ranges from -40ºC to 170ºC (-40ºF to 225ºF)
• Availability of high-pressure models for use with Wilden H800 model pumps
From The Field
Talking about the concepts behind the improvements in diaphragm construction and performance is one thing, but real-world examples are another. Since they have been introduced to the market, the Chem-Fuse IPDs have gained rapid acceptance from their users. Here are several examples:
• A U.S.-based paint manufacturer was using 2" Wilden AODD pumps with standard Wil-Flex diaphragms to move a titanium dioxide (TiO2) paint slurry in its manufacturing operation. The Wil-Flex diaphragms were wearing out every three to six months because of the TiO2 slurry’s abrasiveness. However, since switching to Chem Fuse IPDs, the pumps have been running for more than three years without needing to be replaced, an increased life span of 6 to 12 times the original diaphragms.
• A U.S.-based company that manufactures a polishing compound for glass and plastics – which is twice as abrasive as TiO2 – was using 1" plastic Wilden AODD pumps for the operation. After experimenting with numerous diaphragms, the company switched to Chem- Fuse IPDs in early 2016 and has not had a diaphragm fail since.
• A U.S.-based glass manufacturer that produces large telescopic lenses for use in aerospace applications uses an abrasive silica to polish the faces of the lenses. To
facilitate this polishing process, the customer utilizes Wilden 2" ductile-iron AODD pumps. After experiencing failures with standard rubber diaphragms, the manufacturer turned to Chem-Fuse IPDs, which provide the flow rates and suction lift that are necessary to successfully perform the silica-pumping process while protecting against harmful leaks.
• A company that develops nutritional ingredients that are used in the production of animal feeds uses approximately 90 Wilden pumps in its manufacturing operation. The pumps were initially equipped with Teflon® diaphragms, but switched to Wil-Flex diaphragms. However, the abrasive nature of the liquids that were being handled was causing premature failure to the Wil-Flex diaphragms. As a solution, all 90 pumps
have been converted to Chem-Fuse IPDs and the user has experienced increased diaphragm life, while eliminating any chance that product-to-product cross contamination will occur.
Conclusion
Over the years, the diaphragms that play such an important role in the operation of AODD pumps have undergone some very meaningful revisions in their designs and materials of construction. The most recent has been the development of integral-piston diaphragms that can eliminate the wear and product-containment concerns that have hampered standard diaphragm models, but do it while producing a stroke length
that can optimize flow rates, suction-lift capabilities and efficiency. Wilden has contributed to this “path for the diaphragms of the future” by creating the Chem-Fuse IPDs, which have already begun to leave their mark on many critical liquid-handling applications in the chemical and industrial markets.
About the Author:
Erik Solfelt is the Diaphragm Pump Product Manager for Wilden® and PSG®. He can be reached at (909) 422-1741 or erik.solfelt@psgdover.com. Based in Grand Terrace, CA, USA, Wilden is the global leader in air-operated double-diaphragm (AODD) pumps and a product brand of PSG, a Dover company. Headquartered in Oakbrook Terrace, IL, USA, PSG is comprised of several of the world’s leading pump brands, including Abaque™, Almatec®, Blackmer®, Ebsray®, Griswold™, EnviroGear®, Mouvex®, Neptune™, Quattroflow™ and Wilden®. For more information on Wilden or PSG, please go to wildenpump.com or psgdover.com.