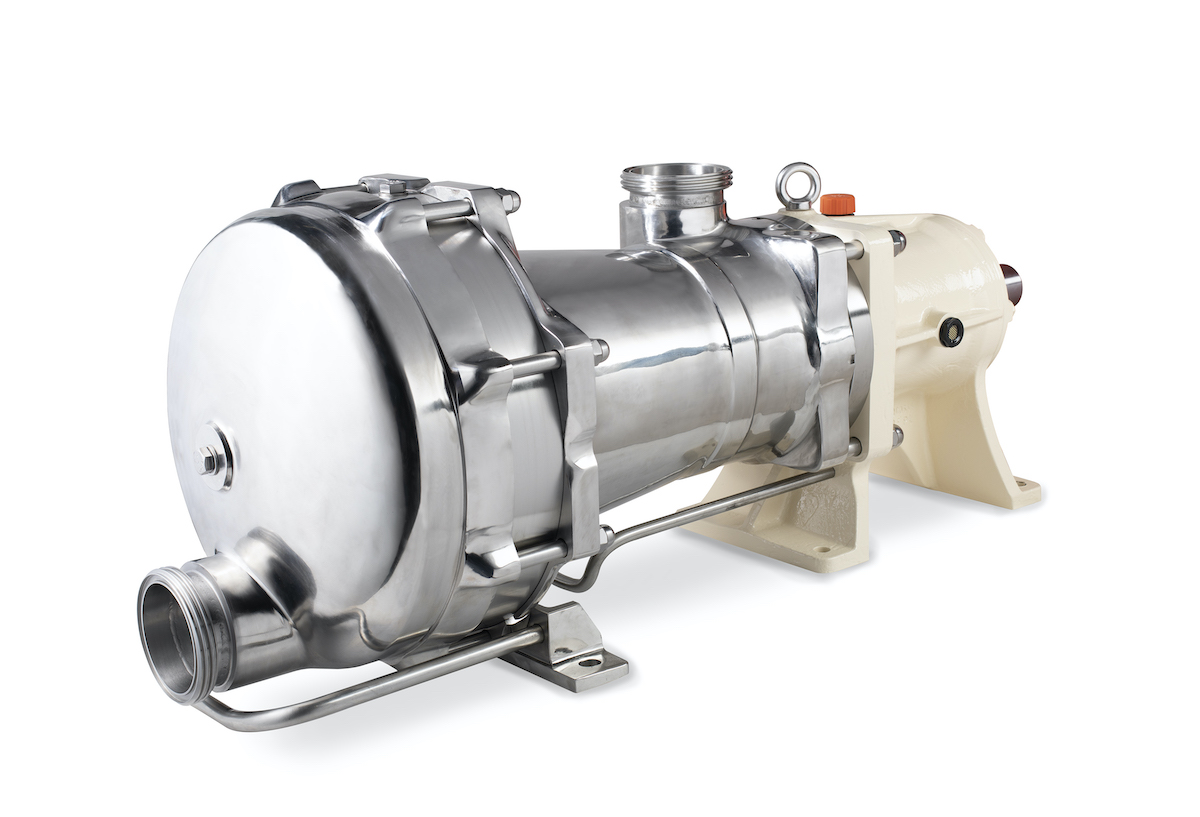
Moving industrial fluids from one point to another is essential to the health of the worldwide economy. There are a variety of methods to transfer these fluids, with the most common being by truck and rail.
The process of loading and unloading tank trucks and railcars occurs daily thousands of times at industrial sites across the world. While this is a routine procedure, it also comes with safety and cost challenges. On the safety side, the primary risks associated with fluid transfer include leakage and spillage, both of which can create catastrophic consequences. Hazards from leaks and spills range from widespread pollution to fires.
Regarding expenses, spills and leaks lead to a loss of product. When you consider the frequency of fluid transfers across the world, a small spill or leak during each of those interactions creates substantial product loss, all of which impacts the bottom line to the tune of millions of dollars. Additionally, if leaks or spills occur, then maintenance also becomes an immediate necessity on the pumping equipment, which adds to those costs. Another costly problem comes from shearing when using a non-adapted pumping technology.
Complicating fluid transfer is the fluid itself. Each liquid brings its share of unique challenges when it comes to loading and unloading. In the chart above, are a few examples of liquids that are transported by road or rail. If there is at least one “yes” in the product line, an adapted pumping technology must be used for loading and unloading applications.
Hazards
Leaks from pumping equipment typically come from the mechanical seal. A truck uses an unloading pump intermittently, meaning that its intervals are not continuous or steady. Those circumstances can prove problematic for products that dry or polymerize when static, especially when a mechanical seal has a leak. Those products will leak rapidly from the compromised seal.
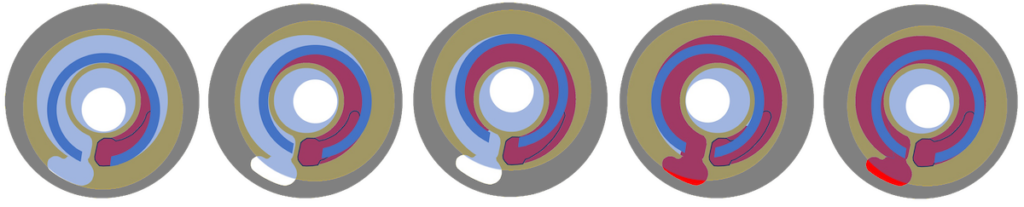
Spillage is nearly impossible to avoid. During those thousands of routine transfers, the hose between the truck tank and the pump must be disconnected. Regardless of the liquid, there will always be some left inside the disconnected segments. This requires recovery protocols and protective measures for staff.
Costs issues
Outside of the high expenses that come from safety issues, the main costs associated with loading and unloading pumps are maintenance, downtime and product loss.
Regarding maintenance, it’s almost inevitable that a mechanical seal will eventually leak. Complications arise even further when considering some applications feature pumps that run continuously, such as with isocyanates. These low-molecular weight chemicals cannot be left in a static state. When they are not moving during loading and unloading functions, they are kept active through continuously running pumps.
Under this scenario, a failed mechanical seal will cause a serious leak, resulting in severe costs, including lost product, maintenance on the seal, product cleanup and halted production. All of these costs accumulate to create an unnecessary and harmful financial burden.
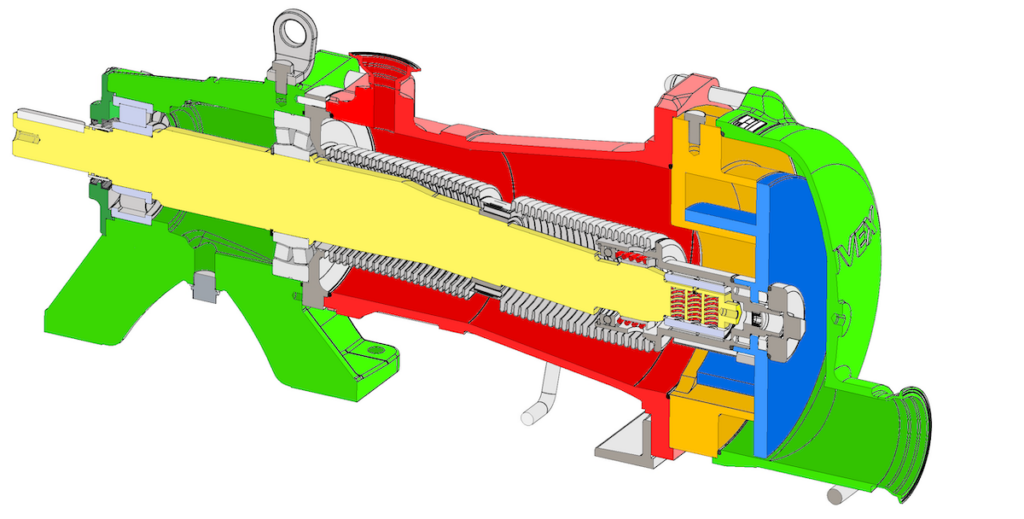
Downtime results from these complications. If liquids cannot be transferred, it amounts to lost time on both ends and also affects the downstream process. The longer the downtime, the more detrimental the costs.
Product loss affects costs because of the expensive nature of the transferred liquids. Whether it be through a major spill or a slow mechanical seal leak, any loss of product will impact expenses. Over time, those expenses become more pronounced and harmful. Additionally, the loss of the product isn’t the only issue. That lost product, especially during spills, needs to be cleaned up, which raises costs.
Addressing the challenge
Mouvex eccentric disc pumps can mitigate all of the challenges that come from liquid transfers. This technology consists of a cylinder and pumping element mounted on an eccentric shaft. As the shaft rotates, the pumping element forms chambers within the cylinder. This increases the size of the cylinder at the intake port and draws fluid into the pumping chamber. The fluid moves to the discharge port, where the pumping chamber size decreases, squeezing out the fluid.
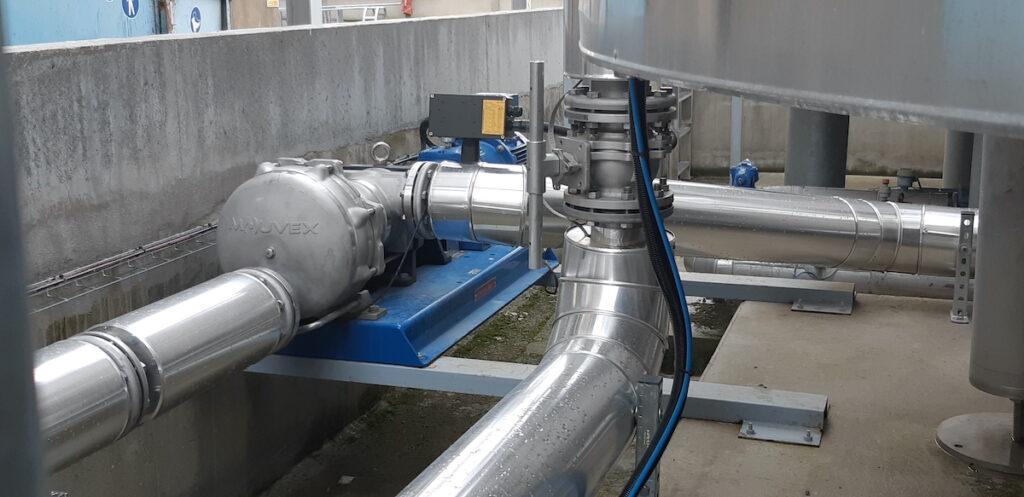
During loading and unloading, this unique design provides the following:
- Line stripping that leaves a minimum amount of product inside the hoses on the suction and discharge sides after transfer, which ensures cleaner and safer operation and reduces the opportunity for product spillage. This is crucial, especially when transferring a dangerous chemical.
- Self-priming from underground tanks. This is necessary to start the pump and creates a strong vacuum to lift the liquid.
- No mechanical seal, which ensures no maintenance and no leaks, and thus no downtime.
- Limited regular maintenance. The only maintenance needed is a transmission oil change every 24,000 hours, which equates to every 2.7 years. This is for a pump that runs continuously year-round.
- Constant flow rate vs. variable viscosity – Loading and unloading applications are generally located outside with significant ambient temperature variations between winter and summer.
- Constant flow rate vs. variable pressure – When filling a tank from the bottom, the discharge pressure will increase while the level rises.
- Low shear on fragile products.
- Can run dry for up to five minutes even in ATEX zones.
- Up to 300 gpm (70 m3/h).
Proven performance Mouvex seal-less eccentric pumps have proven their performances and reliability on many loading and unloading applications.
This article is published by Mouvex:
Mouvex®, part of PSG, was established in 1906 by the engineer André Petit when he identified the challenges that gear and lobe pump users were facing in optimizing their process and invented the eccentric disc pump as a result. His successors have all followed in his footsteps, including his son Albert, who ran the company from 1938 until it was taken over in 1998 by Blackmer®. With the help of Blackmer, Mouvex transitioned from a highly successful company in the French marketplace into a truly global organization, expanding its product offerings to include rotary vane and screw compressors, and peristaltic hose pumps. Mouvex became part of PSG® in 2008, and now has operations on five continents with a global network of distributors and original equipment manufacturers. Today, Mouvex is a global corporation focused on developing new products and conquering new markets to ensure the company’s future throughout the century to come.