According to the National Fire Prevention Association (NFPA), the number of fires and explosions—which the NFPA classifies in three ways: structure, vehicle and outside/other (garbage/rubbish/vegetation)—at retail service stations in the United States have been on a significantly steady decline since 1980. There are now less than 5,000 reported incidents in any given year, a decline of more than 70% since 1980.
The downward trend in service station fires is obviously a positive one, but the cold statistics leave out a significant part of the story, mainly that every fire or explosion at a service station is its own little tragedy that adversely affects the lives of the station owner/operator and the customers, while also potentially harming the surrounding environment. In fact, the NFPA reports that service station fires and explosions annually result, on average, in two civilian deaths, 48 civilian injuries and $20 million in direct property damage.
So while the overall statistics may be rosy, ensuring the safety of service station owners, customers and the environment is still an ongoing challenge that will not be overcome until the number of incidents reaches zero.
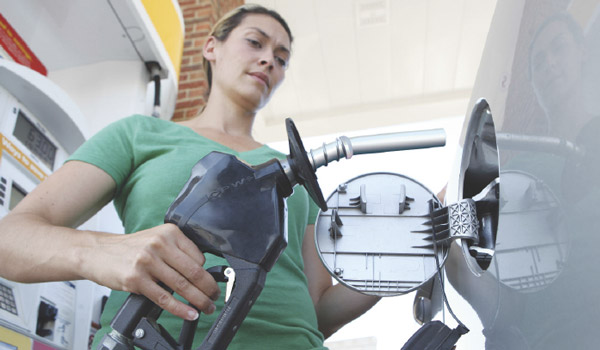
The Challenge
The biggest challenge facing service station operators and their customers is the most obvious one: every day thousands of gallons of a highly flammable, volatile, explosive and toxic liquid are unloaded, handled, stored and dispensed. Looking at it that way, it’s actually amazing that there are not more fire or explosion incidents at the nation’s service stations.
Self-service gasoline stations have been a fact of life in the United States and Canada (with a few exceptions) for nearly 70 years. Historical records show that the first self-service station in the U.S. began operation in Los Angeles, California, in 1947, with Canada’s first self-serve facility coming online in Winnipeg, Manitoba, two years later in 1949.
That means for almost seven decades a lot of motor fuels have been pumped by a lot of people who have never really been trained for the task, many of whom, in the old days, would actually hold the nozzle in one hand and a lit cigarette in the other as they filled the vehicle tank. Besides the obvious safety concerns, there are many potential distractions when filling up, from the rambunctious kids who are acting up in the backseat to the cell phone that will not stop ringing to the commercials that are playing on the TV on top of the dispenser.
All of these distractions can lead to a mistake, whether leaving the nozzle in the fill pipe while driving away or spilling fuel on the pavement. Human error, unfortunately, is one thing that will never be totally eradicated.
There is potential for human error on the operator end of the fueling equation as well. Service station fueling systems are a complex mix of pipes, hoses, fittings, monitors, sensors and tanks, all of which must be installed, observed and maintained properly. Even the smallest, seemingly inconsequential leak in a fitting or from an underground storage tank (UST) can eventually result in a catastrophic incident, whether it be a fire or explosion or toxic product release to the environment, which can harm the soil and groundwater of surrounding communities.
Keeping all of this in mind, owners and operators of service stations should know that when they get into the business, their first priority should be keeping the gasoline or diesel fuel out of the ground and out of the air where it can lead to a fire incident or environmental contamination. Helping to achieve this end result are any number of federal, state or local regulations that must be followed. If they are not, the owner/operator can be subject to fines, remediation costs and, in the worst-case scenario, closure.
The Solution
Riding shotgun with service station owners/operators in their quest to make the fueling experience as safe as possible for the consumer and environment (and themselves) are the manufacturers of above ground and underground equipment, components and systems for use at service stations. The manufacturers of service station equipment have readily risen to the occasion; the technologies used to ensure the safe transfer, storage and dispensing of motor fuels have evolved more since the dawn of the new millennium than in the previous 50 years.
These advances have come in two distinct equipment realms: underground and above ground. Let’s look at each segment individually.
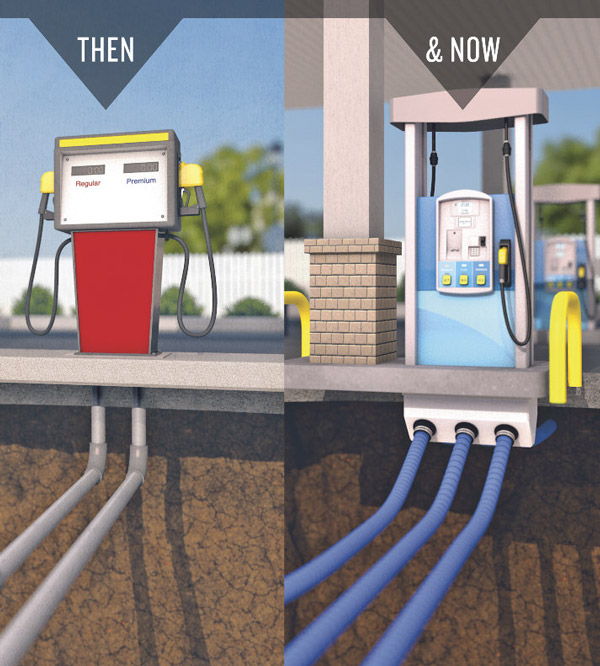
Underground
The work below grade takes place before the service station is in operation. It consists of all of the equipment and components that will enable the fuel to be dropped at the site and stored in the USTs before eventually finding its way into the vehicle’s fuel tank. The goal of manufacturers of this type of equipment is to make it smarter than the least, ahem, “accomplished” person who will be installing it. In other words, the manufacturer can create a “bulletproof” system that meets all Underwriters Laboratories (UL) and U.S. Environmental Protection Agency (EPA) requirements, but that system is only as good as the
“worst” contractor installing it.
In recent years, a number of technological advancements have helped make that goal easier to achieve, with many of these now considered to be industry-standard technologies, including:
Loop Systems — Completely integrated, environmentally secure underground fuel-delivery systems that, by design, employ pre-fabricated, factory-assembled components that result in dramatically less field labor and lower associated installation costs and the potential for installation errors. They eliminate the need for time-consuming and costly field fabrications, such as installing entry fittings or welding or gluing joints that will be buried in the ground. The less field fabrication needed, the less potential for contractor error.
Vapor-Tight and Testable Overfill Prevention Valves — Vapor-tight two-stage valves designed to prevent the overfill of USTs by providing a positive shutoff of product delivery when the liquid level reaches 95% to 98% of the UST’s storage capacity. In addition to being vapor-tight, these new valves are testable from the surface so maintenance personnel do not have to remove the valve from the UST. The EPA is also now recognizing the fact that this equipment needs to be tested more often than just at initial installation.
Double-Wall Spill Containers — Installed in the same space as single-wall spill containers, but significantly improved reliability, monitoring, leak containment and serviceability. Marketers are required to install double tanks and piping, so it only makes sense to have double-wall spill containers. More fuel is introduced into the ground at the fill point than with any leaking tank or piping. The interstitial space on the double-wall bucket also makes it easy to
test the integrity of the bucket by using a vacuum versus filling the spill bucket with water that will then be contaminated and must be disposed of properly. Again, the EPA now recognizes the need to test this equipment periodically instead of just at initial installation. Double-wall spill containers will be much easier and less expensive to test.
Replaceable Single-Wall Spill Containers — Affordable, easy-access spill containers that do not require concrete to be broken during their installation and meet all requirements of the 1998 and 2015 UST regulations in the United States.
Rigid Entry Fittings — Have minimal exposed rubber and the sealing redundancy throughout the fitting provides maximum containment and protection from water intrusion, even after ground shifting. No longer do retailers have to deal with the cost and unreliability of fiberglass or steel piping and joints that need to be glued. This fitting can be repaired, replaced or maintained from inside the sump versus a welded or glued joint that would require replacing the entire containment sump. The glued or welded entry fittings provide no relief from shifting ground and simply provide a shear or break point for the product piping.
In addition to the physical improvements to underground equipment, there has also been a huge leap forward in smart technologies that are giving service station operators a mobile access point to their sites at all times via smartphone and other evolving communication technologies.
These technologies provide the capability for the operator to review and access information instantly, letting the operator know if a UST system is not working properly or even if it has been installed correctly. This fingertip information in real time will help operators identify and correct leaks, spills and overfills before they can even occur, which creates an added level of safety for both the consumer and the environment.
Above ground
This is truly where the great unknown enters the service station safety equation: consumers with their various degrees of aptitude and that long list of distractions that we touched upon earlier. Once that fuel moves into the dispenser, it is at the mercy of the person operating the nozzle. To improve the safety of the fueling experience, as well as to protect against driveaway incidents, equipment manufacturers have developed a number of landmark solutions in recent years, including:
No Flow, No-Pressure Devices (B-Cap) In Automatic Nozzles — These have been designed for use in retail and commercial fueling applications as a way to help prevent fuel spills. This iteration of fueling nozzle will not open until the dispensing system is pressurized and will close automatically when the pressure is removed, which cuts off the flow of fuel before it can be spilled. UL now requires any nozzles at a self-service station that wants to use hold-open latches to be equipped with this safety feature.
Emergency Shutoff Valves — These highly sensitive shutoff valves protect against the hazards of undetected shear groove leaks that may have been caused by low-impact incidents, such as a driver backing his vehicle into the dispenser, or a more dangerous pulled over or dislodged dispenser. They also prevent damaged shear grooves from allowing fuel to leak into dispenser sumps, which reduces the risk of fire, explosion, personal injury, property damage, product loss, environmental contamination and cleanup costs.
Dry Reconnectable Breakaways — These dispenser components have been designed to deliver an increased level of safety and security in the event of a driveaway incident. Not only are they fast and easy to reconnect, but their method of operation delivers the greatest peace of mind that the breakaway has been securely reconnected. When separation occurs at a designated pull force, the breakaway’s dual valves seat automatically, stopping the flow of fuel and limited spillage, while simultaneously protecting the dispensing equipment.
Conclusion
While a goal of zero fires or explosions at service stations is commendable, it is highly unlikely that level of safety will ever be realized, mainly because accidents will always happen and the human element cannot be taken out of the equation. But the level of service station safety has undoubtedly been improved over the past 15 years, thanks to the efforts of manufacturers who have designed, engineered and marketed both underground and above ground equipment and systems that have helped make the fueling experience a better one for site operators, consumers and the environment. The ultimate trick is to educate marketers about these technological advances and any new industry regulations. The even bigger challenge is getting the marketer to pay the few extra dollars that may prevent a catastrophic event.
About the Author
Ed Kammerer is the director of global product management for OPW, based in Cincinnati, Ohio, USA. OPW is a leader in fueling solutions and innovations worldwide. OPW delivers product excellence and a comprehensive line of fueling equipment and services to retail and commercial fueling operations around the globe. Ed can be reached at ed.kammerer@opwglobal.com. For more information on OPW, please go to www.OPWGlobal.com.