By Replacing Injection-molded Plastic AODD Pumps With Solid-block Models, More Optimal Noise And Production Levels In Filling Operations Can Be Achieved
Langguth Chemie, based in Konigsbrunn, Germany, produces various types of cleaners, disinfectants, and detergents for commercial and industrial applications, as well as personal-care products like soaps, lotions, shower gels, and hand sanitisers. During these processes, Langguth Chemie has faced numerous challenges in attempting to optimise the cost-effectiveness of its production and product-transfer operations.
One specific area of concern was the packaging area, where finished cleaners, detergents, disinfectants, soaps, lotions, and other products needed to be pumped from 6,000L holding tanks into containers — which generally range in size from 5 to 10L – before being shipped to the end-user. This is a strict, precise process with the pumps required to transfer exact volumes while also being able to operate reliably in demanding start/stop conditions. In other words, when the employee pushes a button, the pump has to inject the appropriate volume and then stop immediately, which is any pump’s main challenge in these kinds of operations.
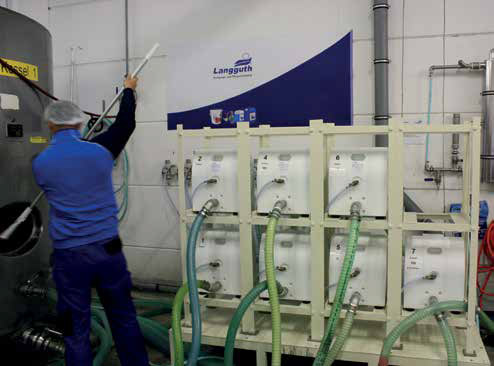
After watching a number of plastic AODD pumps fail in its continuous-duty container-filling operations, Langguth Chemie chose the E40 Series AODD pump from Almatec
For years, Langguth Chemie had been using plastic air-operated double-diaphragm (AODD) pump technology. Over time, Langguth’s CEO and managing director Klaus Langguth and his technical engineer, Roland Mordstein, had begun noticing that the pumps weren’t living up to expectations in several critical areas: pumping high-viscosity liquids against pressure, air consumption, and noise generation.
‘We needed a reliable pump system that has high suction capabilities when you pump against pressure with high-viscosity liquids and which will not get dry when pumping out of containers,’ explains Langguth. ‘We tried other pumps, but they took too much air in order to work, were too loud, which is very inconvenient, were difficult to maintain, and not very reliable.’
In fact, the old pumps needed so much compressed air during their operation that Langguth Chemie was contemplating the purchase of a new air compressor in order to handle the higher air volumes required to even operate the pumps. Instead of going for such a drastic measure, however, Langguth chose to search for a different, better technological solution.
Making a commitment
That search led Langguth and Mordstein to Almatec E-Series AODD pumps, specifically the E40 model. Part of PSG, a Dover company, Almatec is an AODD pumps provider, with its manufacturing facility at PSG’s Kamp-Lintfort site in Germany.
The E-Series pumps are a next-generation technology that has replaced Almatec’s standard-setting A-Series AODD pump line. Advancements in the E-Series include a diaphragm-sized ring on each side of the pump that allows a series of housing bolts to be tightened against the housing resulting in a more even spreading of housing-bolt force, an optimised flow pattern that decreases resistance and increases energy efficiency, and the use of less air to achieve the same level of flow.
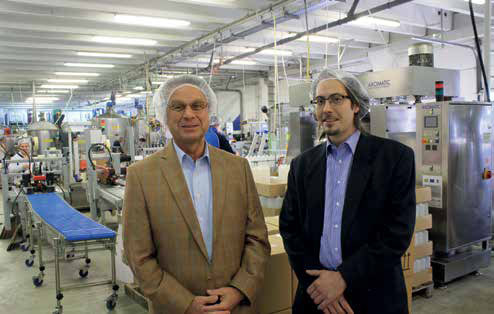
In the search for a better pumping solution, Roland Mordstein, right, technical engineer for Langguth Chemie, turned to Harald Vogl, regional sales manager for Almatec and PSG
After successfully testing one E40 pump last year, Langguth Chemie now employs eight E40 models in its container-filling operation, even though they have a higher purchase price than the old pumps that were previously being used. That higher purchase price, however, has been negated via the reduction in air consumption, maintenance, and downtime costs that were piling up as a result of broken diaphragms that needed to be replaced on the old pumps.
‘The mechanical parts are more stable in the Almatec pumps, they hold the air pressure better and longer so the air consumption is lower,’ says Mordstein. ‘It’s a theoretical level of 50% less air consumption and I think in practical usage we are receiving, without any effect on flow rates, a 30% to 50% increase in sealability.’
‘The problem was air. The old pumps needed too much of it, about double the amount that the Almatec needs,’ Langguth adds. ‘That resulted in much higher costs for air and energy. Now, in our system, we are pretty safe and have reserves of air capacity. With the old pumps we were probably going to need a new compressor.’
Efficiency and noise reduction
In terms of operational characteristics, the E40 pumps feature solid-block polyethylene (PE) construction (as opposed to the moulded-plastic construction of the older pumps), a 38mm port size, dry-suction lift of up to 4m, wet-suction lift to 9.5m, and maximum operating pressures of 7 bar. They can handle fluid temperatures up to 70ºC. Standard diaphragms are PTFE (Teflon), but after several months of use, Langguth Chemie has determined that the same, if not higher, level of pump performance can be achieved with the incorporation of EPDM diaphragms. With that in mind, the company is in the process of changing out the PTFE diaphragms and replacing them with EPDM models.
‘When handling soaps and other cleaners, oftentimes the ingredients are surfactants that can crack plastic, which is something we always had to watch out for,’ says Mordstein. ‘The EPDM diaphragms are working well so far.’
The most noticeable advantage of the E40 pumps is apparent in the filling room — namely that one can hear oneself think or comfortably carry on a conversation.
‘If the pumps are noisy and you have eight or ten pieces of equipment running, it is really loud, and all of our people start getting mad,’ says Langguth. ‘Everyone is happy with the quieter pumps.’
‘The noise is reduced by 300%,’ Mordstein adds. ‘There’s about seven pumps running at one time and one of the previous pumps made so much more noise than the seven Almatec’s running at once.’
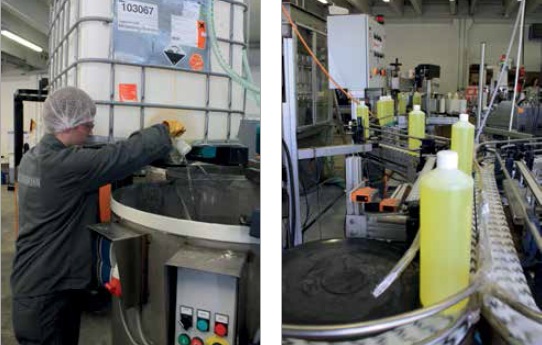
From the time a technician doses the ingredients into a mixing vessel until the end-product is bottled and sent down the packaging line, Langguth Chemie relies on AODD pumps to ensure that its manufacturing process is efficient, cost-effective, and less noisy
Conclusion
Helping Langguth Chemie achieve its status as a producer of high-quality goods have been the Almatec E40 Series AODD pumps. By replacing an underperforming competitive model with the E40 pumps, Langguth Chemie has been able to realise new levels of operational performance, reliability, and cost savings in its container-filling applications.
‘I made the choice to go to new pumps because the old pumps were having problems and the Almatec pumps have solved all those problems,’ says Langguth. ‘They are much easier to handle and cost less in the long run, that’s why I chose them.’
For more information:
This article was written by Harald Vogl, regional sales manager — Germany for Almatec and PSG. Visit: www.almatec.de or www.psgdover.com