Introduction
The universe of industrial resins includes natural or synthetic compounds. Synthetic resins are less expensive, more stable, predictable and easier to refine than their natural counterparts. Synthetic resins are the foundation within paint and plastic production. The focus of this article is the use of positive displacement, magnetically driven seal-less internal gear pumps, which have been proven in critical resin applications.
The all-encompassing term “resin” includes thermoplastic, thermosetting, engineered resins and thermoplastic elastomers. Among the plastic resins, polyethylene (LDPE, LLDPE and HDPE) and polypropylene (PP) are ones with major demand in the United States with 16.9 million metric tons and 7.4 million metric tons, respectively, produced in 2011. Resins are further classified as polyester resins, epoxy resins, polyurethane resins, alkyd resins and acrylate resin. To further complicate things, fillers, catalysts and modifiers may be added to resins to increase their reliability and range of uses. Therefore, many resins are custom formulations, with some being heat and/or shear sensitive.
Pump selection requires an understanding of all properties as they apply to a specific resin. Other considerations should include a review of the suction and discharge piping system, operation duty cycles and flushing procedures. It is helpful to understand the historic pump selection for the resin-handling operation, along with operation costs and concerns. Most frequently, the primary need is to permanently eliminate shaft leakage.
The Challenge
Where positive displacement rotary gear pumps are common in resin service, few pump users dispute their sealing is the weak point among common pumps. Current production and handling demands require total leak-free operation. A review of historic sealing technologies follows:
-
Packing
For years, positive displacement pump manufacturers recommended packing for resin service.
Typically, this meant the use of a braided packing material that included a set of formed rings that are wrapped around the pump shaft and held in place by an adjustable gland that would control product leakage. A common operational guideline for these systems called for gland adjustment when one drop of liquid per minute per inch of shaft circumference was recorded. Finding this sweet spot in gland operation is difficult. Over-tightening the gland can close off product flow altogether, potentially grooving or damaging the pump shaft or pump sleeve surface. Because of these shortcomings, packed-style pumps are no longer accepted in most resin-manufacturing applications.
- Multiple Lip Cartridge Seals
Lip seals have found favor handling hot and/or sticky liquids, including some resins. In this design, an elastomeric lip seal includes an inner-lip diameter that is slightly smaller than the shaft diameter. Each lip is energized or loaded to a precise radial force between the lip and the shaft. Over time, however, the inner lip wears, as does the pump shaft/sleeve surface. While it is possible to monitor this condition and rebuild the seal before the remaining lips fail and a leak occurs, care must be taken to limit the pressure to the manufacturer’s pump rating in order to avoid catastrophic lip-seal failures.
- Mechanical Seals
Mechanical seals are the proven shaft-sealing workhorses in resin service where selections are endless and continue to evolve. A single mechanical seal works through the use of two very flat (generally within three light bands flat) lapped faces that make it difficult for liquid leakage to occur (though vapors may escape). One of the lapped faces is stationary while the other rotates with the pump shaft. One of the lapped faces is usually constructed of a non-galling material, such as carbon-graphite, with the other constructed of a harder material. This allows one of the lapped faces to be sacrificial; this face is commonly called the “wear nose.” In fairness to mechanical-seal manufacturers, the cards are stacked against them since light-band tolerances are not consistent with pump-shaft sleeve bearings that can register clearances in the .01 in.– .02 in. range. In addition, the traditional pump manufacturer’s design includes a cantilevered load where tests at 200 psi (13.8 bar) result in a shaft deflection of .056 in. Additionally, pumps that are designed for ease of seal replacement neglect to highlight inspection of the primary shaft-support bushing. This critical component is not easily replaced or inspected, yet it supports the entire length of the rotating shaft assembly.
Fig. 2, 3 & 4 are a few examples of what can go wrong when pump styles with inadequate product-sealing capabilities are used in resin-handling applications.
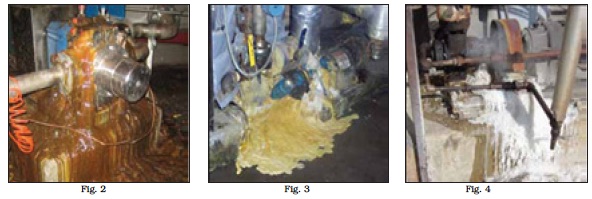
Two distinct subsets of mechanical seals include specific drawbacks when used in resin service:
- Single Mechanical Seals
Single seals are seldom used in resin service anymore. With the rotating seal component turning in the resin, viscous drag can cause the seal to distort or, in a worst-case scenario, break free from the shaft. Also, heat-sensitive resins may solidify on the seal face. Single seals control leakage but do not eliminate vapor emission.
- Double Mechanical Seals (dual-pressurized)
Double seals are utilized in viscous, abrasive or thermosetting resin applications. Properly maintained double seals eliminate process-vapor loss. In this design, all four sealing faces operate within a pressurized barrier-fluid system. In addition to its premium price, this system can be expensive and challenging to maintain. Monitoring of the barrier fluid is essential since if the inner seal were to fail the barrier fluid could enter the pump’s wetted path and contaminate the production process. Should the outer seal fail; the barrier fluid will escape and also allow the inner seal to open. Some positive displacement pumps require two and even four stuffing-box seals, which further complicates maintenance and repair.
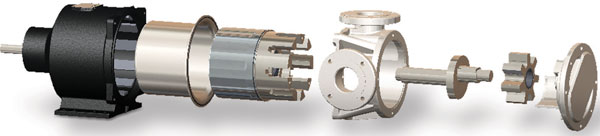
Fig. 5: Maag Industrial Pump’s EnviroGear® Seal-less Internal Gear Pumps are designed with only seven primary parts for ease of operation and maintenance
The Solution
The solution includes a magnetically driven seal-less EnviroGear® resin pump. EnviroGear® pumps are manufactured in Grand Terrace, CA, USA, and part of Maag Industrial Pumps division of PSG®, a Dover Company, which is headquartered in Oakbrook Terrace, IL, USA.
EnviroGear Internal Gear Pumps are ideal for resin-handling applications and feature a patented “between-the-bearing” support system that eliminates the cantilevered-load issues that can plague other types of positive displacement pumps.
The innovative between the bearing support system allows the pump to support the rotor and idler gears at three locations through the incorporation of:
- A patented Eccentric Spindle that is supported in the head, the crescent location and the back of the containment canister, eliminating much of the effects of cantilever load. Because there is only 0.005 in. of shaft deflection in an EnviroGear pump it has 11 times less shaft deflection than competitive technologies.
- Large, long radial bushings that support the entire length of the rotating element, which spreads out the hydraulic forces and allows the bushings to last longer. The bushings include premium-grade carbon-graphite that will last up to eight times longer than more common bushing materials.
- Larger diameter materials that provide more rigid support for less shaft deflection and bearing wear. For example, a traditional 3-inch seal-less pump will have a shaft that is 1-7/16 in. in diameter; the diameter of the EnviroGear eccentric spindle is 2 in.
As the use of seal-less internal gear pump technology continues to grow in resin service, due diligence is still required in pump selection, along with the understanding that although most resin applications are ideal for seal-less pumps, some are not, particularly those resins that include heat-sensitive materials or may include highly abrasive fillers.
The EnviroGear pump is a proven affordable technology over the life of the pump. The Hydraulic Institute reports that as much as 50% of the cost of owning a pump is spent after the pump is bought, due to maintenance issues. Still, initial purchase costs are important. In most cases, EnviroGear pumps are competitively priced when compared to double-sealed pumps, and priced below traditional magnetically sealed offerings.
Although seal-less internal gear pumps should not run dry for extended periods, the same can be said for mechanically sealed pumps. Seals allow small amounts of liquid to pass across their faces in order to provide lubrication. Mechanically sealed pumps do not like running dry, which is why they must be closely monitored when sealing environmentally sensitive products. Where centrifugal pumps operate at 1,750 rpm and even 3,450 rpm, internal gear pumps operate at much slower speeds. This is a crucial consideration since eddy-current heat is generated exponentially to speed, making heat buildup in an internal gear pump less of an issue.
Still, running dry, dead heading of the pumps or lockups associated with nuts and bolts, etc., are a shared worry for centrifugal and internal gear pumps. In these instances, a power-monitoring device or the installation of a temperature monitor within the pump offers protection.
EnviroGear seal-less internal gear pumps are designed with only seven primary parts. While many seal-less pumps must be returned for factory repair, the simple design of EnviroGear pumps makes them field serviceable. Should replacement parts be needed, they are typically available the same day with EnviroGear maintaining a complete pump and parts inventory at its headquarters facility. These pumps have also been designed to be interchangeable dimensionally and hydraulically with many brands of mechanically sealed pumps, with installation upgrade costs minimal.

Fig. 6: The EnviroGear® Series offers a complete family of Seal-less Internal Gear Pumps
Conclusion
The design of the EnviroGear Seal-Less Internal Gear Pump makes it an engineered solution for environ-mentally conscious fluid-handling that lowers maintenance costs and eliminates environmental costs-all of which are primary concerns when manufacturing, handling and transporting resins. The EnviroGear pump does away with the operational shortcomings that helped stigmatize past seal-less-pump designs while delivering the totally leak-free operation that resin manufacturers demand. EnviroGear pumps are truly the best choice on the market today for a wide variety of resin-handling applications, and they reliably deliver the peace of mind that operators crave.
For more details, please contact:
PSG®, a Dover Company
Website: www.psgdover.com