Installing Anthony’s innovative refrigeration glass door equipment can lower operating costs, increase energy efficiency and extend product life.
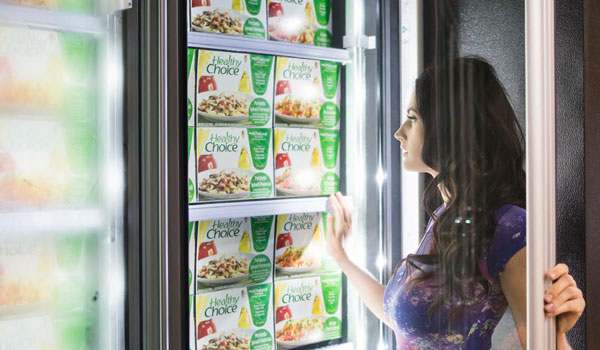
Introduction
Commercial coolers and freezers are heavy consumers of energy. A significant amount of this energy consumption is a direct result of the short life span of door gaskets and the door heat used to prevent sweating or condensate formation.
Maintaining the integrity of cooler and
freezer door gaskets is not only important in conserving refrigerated air and energy within the cases, but also in maintaining food safety and extending refrigeration equipment life, thereby reducing downtime and maintenance expenses. The relentless challenge retailers face is dealing with deteriorating, leaking gaskets that waste energy and needlessly increase operating costs.
Condensate formation on doors, which makes merchandise unappealing and can drip onto the shopping floor to become a slipping hazard and a potential costly lawsuit, is a constant factor retailers seek to avoid by using heated doors. Unfortunately, this method of preventing condensation comes at a high price in the form of significant energy usage.
This paper addresses innovations developed to greatly increase energy efficiency, lower operating costs, decrease maintenance and reduce a retailer’s carbon footprint by retrofitting their existing cooler and freezer doors with these technologies.
Gasket Life — Too Short
Problem — Frequent Gasket Replacement
Refrigerator and freezer door gaskets experience wear and tear from constant door opening and closing, customers leaning on gaskets while shopping and impacts during restocking including damage by stocking carts. Additionally, adding heat to the rails, frames and glass of refrigeration cases to prevent condensate formation also increases wear and tear and causes deformation
of gaskets.
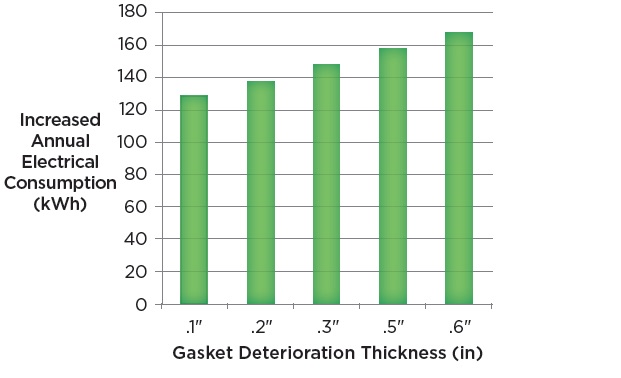
Figure 1. Annual increase in electrical consumption (kWh) for one (1) 101 Series Cooler Door with varying degrees of gasket deterioration. 30" x 75" Door Size, 26 °F Evaporator Temperature and four 32 minute defrost cycles/day.
Gasket deterioration results in a greater potential for air leakage that can compromise food preservation and drive up electrical costs. In freezers, air leakage can even lead to ice formation within the unit and on the merchandise, making the merchandise less appealing to customers. A gasket that has deteriorated merely 0.1” will increase cooler energy usage by 128 kWh annually. A 0.2” deterioration equates to wasting 138 kWh annually per door (See Figure 1).
On average, utilities estimate that extremely damaged and worn gaskets on freezer glass doors can cost retailers as much as $40 to $60 in additional energy expense due to air leakage. To promote energy efficiency and save retailers from this wasted expense, many utilities offer rebates for replacing commercial refrigeration door gaskets.
As a result, periodic refrigerator gasket replacement is an important part of case upkeep, which drives up maintenance and operation expenses. On average, gasket deterioration occurs every three to five years for commercial refrigeration and freezer doors.
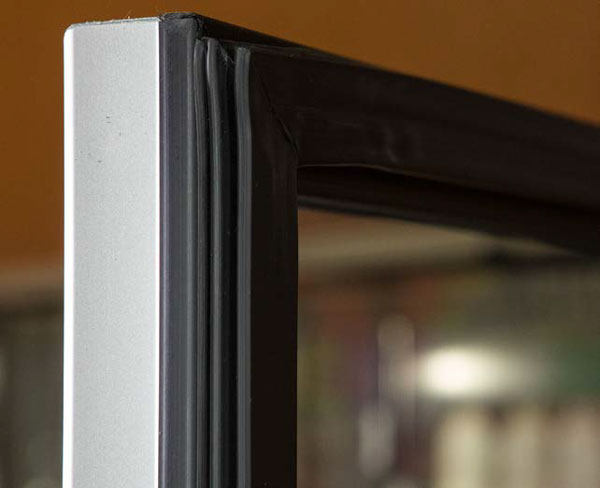
Figure 2. Anthony’s new LifePlus Gasket, installed on a 101 Series Door, has optimal sealing capabilities.
Solution — Improved Gasket Material
Anthony has recently developed a new gasket material, LifePlus Gasket™, with superior sealing performance and life compared to standard PVC gaskets (See Figure 2). Made of a subset of thermoplastic elastomers (TPE), LifePlus Gasket has outstanding elastic and thermosetting properties similar to rubber and excellent molding properties akin to plastics to retain tight sealing performance throughout numerous thermal changes and door closings. LifePlus Gasket is now approved for refrigerator use by the NSF, FDA and has obtained UL and RoHS certifications.
During a Shore Hardness Test by a third-party laboratory, LifePlus Gasket maintained its shape 13% more than PVC gaskets at temperatures reaching -4°F for a more uniform and airtight seal between the cooler door and frame (See Figure 3).
Over 2 years of field-testing of LifePlus Gasket at grocery stores and retail outlets has shown that Anthony’s LifePlus Gaskets maintain excellent sealing qualities under the harshest commercial freezer environments.
Stop the Slam!
Problem — Repeated Impacts
Door gasket deterioration results primarily from repeatedly opening and closing of doors, which occur on average 140 times per day. In addition, the closing of doors weighing
100-200 lbs. can inflict significant force on door gaskets. Current torque rod technology causes doors to shut quickly with a loud
“bang”, sometimes bouncing 3-4 times before coming to rest and causing severe wear on gaskets and mullions. As these parts deteriorate, they allow increasing quantities of refrigerated air to escape, resulting in higher refrigeration energy expenses.
Solution — Advanced Closing
Anthony developed Cloze Control™, an advanced door hold open technology that softly closes doors to reduce gasket wear. Figure 4 depicts Anthony’s Cloze Control installed on a 101 Series door. Its patented dampener reduces the door’s inertia from 100 lbs. force to 20 lbs. force.
Field and laboratory tests of the Cloze Control demonstrate that, when coupled with Anthony’s LifePlus Gasket, the life of door gaskets increases by 100%, from 250,000 to over 500,000 cycles.
Door Retrofit
Problem — Door Heat is Costly for Freezers
A large energy consumer within the commercial refrigeration industry is door heat used to prevent door sweating or condensation. On average, a single freezer door with door-heat consumes approximately 3.3 kWh per day in electricity, amounting to $145 per year in added energy costs annually per door (assuming $.12 kWh cost). In addition, for the freezer to maintain proper temperature (because of the heat generated by door heaters) additional refrigeration load is required to compensate for the heat that is introduced within the freezer. This refrigeration load equates to 1.7 kWh per day, or an additional $73 annually (assuming 1.96 freezer COP). In total, a single freezer door with door heat consumes $218 annually in electricity. Like other door parts, door heat technology is another door component that can fail over the service life of the door and add to maintenance costs.
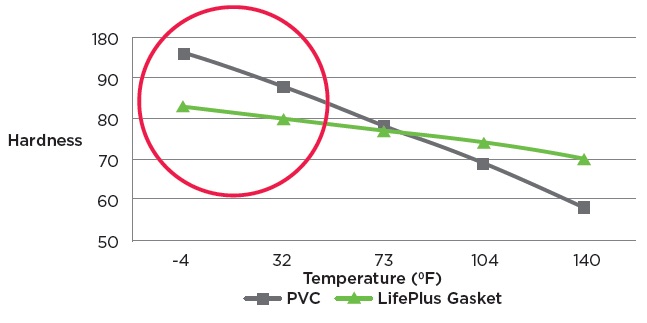
Figure 3. Measurements of material hardness, clearly showing the benefits of LifePlus Gasket versus PVC gaskets: greater flexibility vs. PVC at colder temperatures (see red circle) allows for tighter door seals when applied to coolers and freezers.
Solution — Energy Free Doors
To eliminate the enormous energy drain of door heat yet still prevent door sweat in cooler and freezer applications, Anthony developed the energy-free Eliminaator Renu™ door — zero door heat required. Utilizing advanced door rail design and insulating materials the energy free Eliminaator Renu prevents door sweating without the use of door heat, all while meeting ANSI/ASHRAE Standard 72-2014 for Freezers.3 In addition, for cooler applications not requiring door heat, Anthony also offers a number of Energy Free Cooler doors, such as its Vista C and Infinity 090 doors.
Results — 2 Year Payback
The following compares costs of a retailer maintaining a standard heated freezer door vs. retrofitting such a door with an Eliminaator Renu door, LifePlus Gasket and Cloze Control over a ten-year period.
Maintaining a heated freezer door requires a total cash expenditure of $2,817 over the ten-year period. This includes annual door heat electrical costs, air leakage due to gasket degradation and gasket replacement every five years.
The total cash flow for retrofitting a freezer door with an Eliminaator Renu, LifePlus Gasket and Cloze Control over ten years would be $515. All cash expenditures for the Eliminaator Renu occur the first year alone and include only the purchase price of the door and installation costs. There are no additional expenditures during the remaining ten years. The result is a payback on the investment in 2 years and a total savings of over $2,302 per door! For a 100 freezer door line up the savings add up even quicker: $230,200.
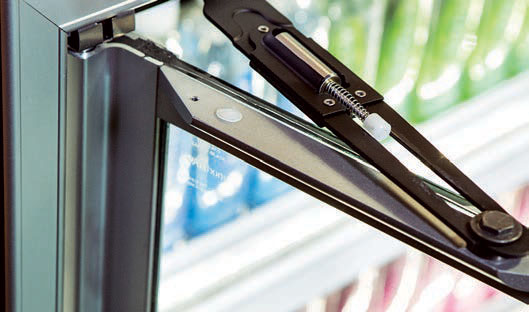
Figure 4. Anthony’s newly developed dampening hold open, Cloze Control™, installed on a Vista B Door.
Conclusion
For years the commercial refrigeration industry has been plagued with refrigeration cases that heavily consume energy via door heat, gaskets that degrade quickly, rising energy prices and ever more stringent Federal Department of Energy requirements.4 Recently, Anthony has innovated new technologies to combat these issues including the LifePlus Gasket, a gasket material that maintains tight door seals at cold temperatures and lasts longer for less maintenance and energy waste; the Cloze Control, advanced door hold open technology that softly closes cooler and freezer doors, further reducing gasket wear; and the Eliminaator Renu that can operate in freezer applications without door heat saving significant energy costs without sacrificing condensation prevention. Combining all three technologies within a door retrofit can provide a retailer over $2,300 in savings during the life of the door.
On a larger basis, it is estimated that there are 2.2 million freezer doors aged 5-15 years in need of service in the U.S. Retrofitting these 2.2 million doors with energy-free doors would save the U.S. commercial refrigeration industry over $480 million in electrical costs and eliminate over 6 billion lbs. of carbon emissions in the form of CO2 based on EPA calculations.5 Retrofitting freezer and cooler doors with new technology can be a long-term investment to decrease operating costs as well as cut energy use and help to green operations.
For more information on Retrofitting your Refrigeration Glass Doors please contact:
MARKETING CONTACT:
Uri Rainisch, Senior Marketing Manager
marketing@anthonyintl.com or +1 818-837-2967
References
- Anthony, I., Annual Operating Cost Comparison. 2015 [cited 2015 5/7/15]; Door Energy
Comparison Calculator].
- Biron, M., Thermoplastics and thermoplastic composites. 1st ed. PDL handbook series. 2013, Oxford ; Waltham, MA: William Andrew. xxvii, 1044 p.
- ASHRAE, ANSI/ASHRAE Standard 72-2014, in Method of Testing Open and Closed Commercial Refrigerators and Freezers. 2014, ASHRAE: Atlanta, GA.
- United States Department of Energy., New Energy Efficiency Standards for Commercial Refrigeration Equipment to Cut Businesses’ Energy Bills and Carbon Pollution. 2014.
- United States Environmental Protection Agency, U.E.P.A. Greenhouse Gas Equivalencies Calculator. 2015 4/16/2014 [cited 2015 4/9/2015]; Available from: http://www.epa.gov/cleanenergy/energy-resources/calculator.html