Optimizing existing AODD pumps with energy-efficient, air-distribution technology has helped Chromalloy improve its gas-turbine-engine service operations.
Founded in 1951, the technology company Chromalloy (chromalloy.com) is a leading provider of solutions that reduce manufacturing and operating costs and extend the life of gas-turbine engines for customers in the commercial-aviation, military, and power industries. One of Chromalloy’s major facilities, its 120,000-sq.-ft. site in Tilburg, The Netherlands, has been in operation since 1975. The components serviced there reflect a veritable who’s who of turbine-engine manufacturers.
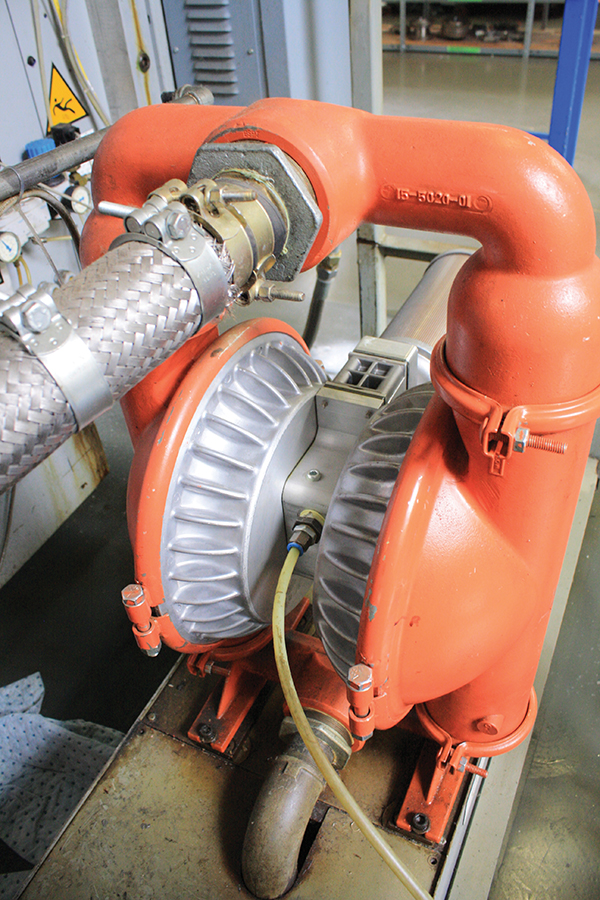
John Bollebakker is the manager of maintenance and facilities at Chromalloy’s gas-turbine-engine service operation in Tilgren, The Netherlands.
“The Tilburg facility is a repair shop for parts used on airplane engines and in other applications,” explained John Bollebakker, the site’s manager of maintenance and facilities. “If an engine needs an overhaul, certain parts will be sent here, whereupon they will be inspected and repaired, and all necessary paperwork completed. We then deliver the part(s) back to the OEM in the shortest time possible.”
The need to improve
A key stage in the engine-repair process involves the continuous transfer of cooling fluids that help keep repair and refinishing machinery operating safely. Since 1998, Chromalloy has been relying on several Wilden Original Series (clamped) air-operated double-diaphragm (AODD) pumps to reliably facilitate the process.
As Bollebakker describes the process, a press pipe in one area introduces the cooling fluid into the process and from there it runs back to the tank where the Wilden pump pulls it out and sends it to the next installation. “In another area,” he said, “we are pumping with the main pumps to the machines and the Wilden gets the fluid to the tank and back to the filter where it is cooled. After that, the main pumps remove the fluid and pump it back to the machine again.” The Wilden units are used for cooling and filtering.
Bollebakker noted that the Wilden pumps had performed admirably during the 16 years since their installation. The only maintenance seemed to have been associated with seal replacements, “once a year or so.” Still, evolving operational demands regarding air usage, efficiency, noise levels, and overall operating costs had led him to consider ways that pump performance could be improved.
Although the Tilburg site was seeking more efficiency from its pumps, it also needed to consider safety issues. “We want a healthy work environment,” Bollebakker stated. “Therefore, we were looking at where we could improve environmental issues or create cost savings by doing whatever it takes to make our ROI the right percentage. From all aspects, we try to do the best thing we can for the company. It should fit into the complete organization, but also fit into the budget.”
In 2013, to help identify pumping technologies that could improve efficiency and cost effectiveness while making operations more “green,” Bollebakker contacted Chromalloy’s pump supplier, Holland Air Pumps, Oirschot, The Netherlands—specifically its commercial director Gerrit Klaassen.
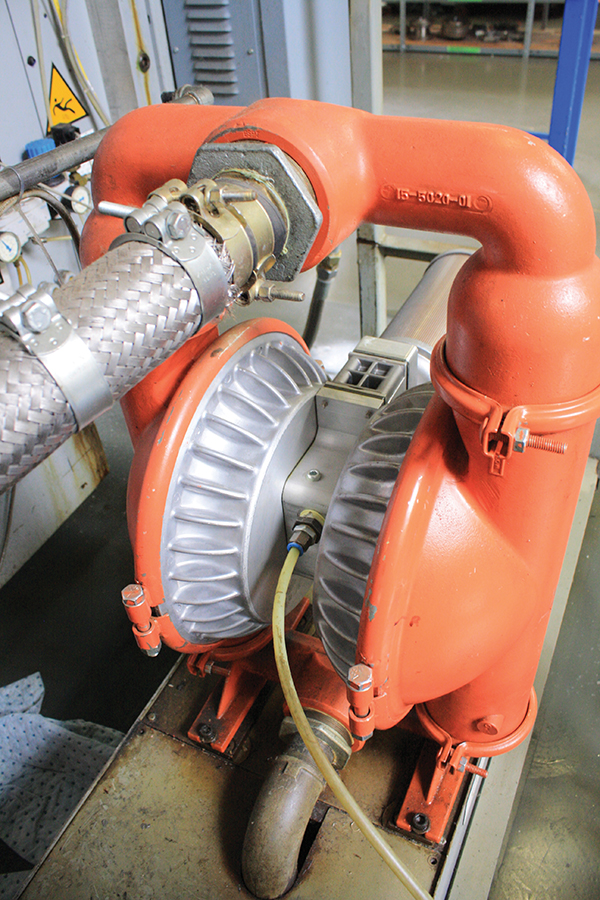
By upgrading its eight existing Wilden AODD pumps with the manufacturer’s Pro- Flo SHIFT air-distribution system (ADS), Chromalloy has been able to significantly reduce its operational costs.
Too good to be true?
Klaassen pointed out that Bollebakker’s search for a more efficient AODD pump came at an ideal time. In June 2013, Wilden introduced its Pro-Flo SHIFT air-distribution system (ADS), featuring an air-control spool that eliminates costly air “overfilling” at the completion of the pump stroke. According to the manufacturer, Pro-Flo SHIFT-equipped pumps lead to savings in air consumption of as much as 60%, while costing 50% less to operate than AODD units with traditional mechanical or electronically actuated ADS technologies.
Reports of that level of performance might have sounded “too good to be true” in some quarters. Committed to proving otherwise, Holland Air Pumps built a skid-based Pro-Flo SHIFT-equipped pump unit and transported it to actual customer sites where the technology was put to the test. Klaassen and others on the distributor’s team, including owner Leo de Haas, have fond memories of the traveling “road show” and its ability to clearly demonstrate how the new ADS worked and what it could do for customer operations. “When they saw it [in operation] for themselves and listened to the pump [as it ran],” he said, “they realized that they suddenly had 30% to 40% more capacity.”
Chromalloy’s Bollebakker was one of those customers. Klaassen conducted a test for him and a colleague at the Tilgren facility in Dec. 2013. Both were intrigued by what they saw. Later, when Wilden provided an overview projection of what the site could save by upgrading existing AODD units with the Pro-Flo SHIFT ADS, Bollebakker was convinced. At that point, he went on to convince the facility’s general manager, and the purchase was quickly approved.
The upgrade itself went smoothly. According to Bollebakker, removing the old ADSs from the site’s existing Wilden pumps and inserting the new Pro-Flo SHIFT ADSs was a simple task. In fact, there was negligible impact on the facility’s 16-hr. daily operating schedule.
“From a production point of view,” Bollebakker said, “I can’t allow myself to go without production for four or six or eight hours, because we have to run for 16. In reality, each of the eight pumps was out of production for only one or two hours. It was an easy job.”
Once the pumps with the new Pro-Flo SHIFT ADS were up and running, it wasn’t long before Bollebakker began to notice—and document—the cost savings. “We’ve taken four cents per cubic meter per hour (m3/hr.) off the operating cost, and at 16 hours per day, five days a week, we calculated that we will be saving €11,000 (US$12,020) per year for the eight pumps,” he marveled. (Translation: The Pro-Flo SHIFT ADS investment would pay for itself in 12 months.)
Seeing is believing
“The Tilgren plant has several areas where we try to improve our systems and look constantly for ways to do things quicker, better, faster,” said Bollebakker. “From the moment we rebuilt the air section on the Wilden pumps, there was an immediate reduction in air supply, but the flow remained the same. When the pump comes in and it’s working the way we want it to work, the case is closed.”
Wilden invented AODD technology in 1955. The business is now a brand of Oakbrook Terrace, IL-based PSG, a Dover company. For more information, visit wildenpump.com and psgdover.com.