In the 110 years since its invention by French engineer Andre Petit, the eccentric disc pump has been used in a wide variety of fluid-handling applications.
Driven by what Petit termed the “eccentric movement principle,” the eccentric disc pump design features a disc placed inside a pump cylinder with an eccentric bearing on the pump shaft driving the disc.
This setup creates four distinct pumping chambers that increase and decrease in volume as the disc rotates, producing suction and discharge pressures as the chambers move in pairs 180 degrees apart. This method of operation ensures that the fluid passes through the pump at a constant and regular flow rate.
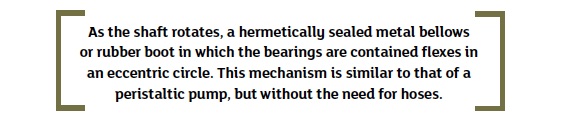
The design also means that eccentric disc pumps do not require mechanical or dynamic seals. As the shaft rotates, a hermetically sealed metal bellows or rubber boot in which the bearings are contained flexes in an eccentric circle. This mechanism is similar to that of a peristaltic pump, but without the need for hoses. This method of operation prevents leaks and enables the fluid to flow through both the pump’s inner and outer chambers without any pulsation or product slip.
The eccentric disc pump’s seal-free design and volumetrically consistent operation are ideal for distributors of raw feedstocks and the manufacturers of end products in the chemical industry. Both the raw materials used and the finished products created in chemical manufacturing can be expensive, so the loss of high-value commodities through product leaks or spills can be detrimental to the operation’s bottom line.
Safety risks also increase when dangerous or hazardous chemicals are not properly contained. Many chemicals and their raw components have unique handling characteristics that must be observed, so operators must employ a pump technology that can successfully check all of the operational boxes.
Handling high-value and specialty chemicals is a daily fact of life for chemical manufacturers. Their operations, however, only achieve the highest level of cost-effectiveness and safety when they incorporate pumping technology that can properly contain uniquely expensive or hazardous feedstocks and finished products.
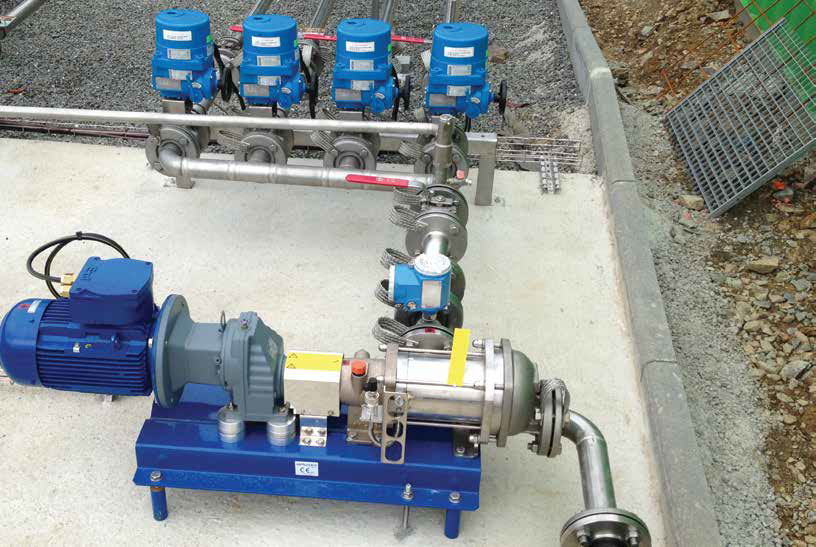
Image 1. Eccentric disc pumps can reliably transfer commodities as diverse as ethanol, pharmaceuticals, isocyanates and paints. (Courtesy of Mouvex)
After experimenting with other types of technology, many global manufacturers in a wide range of industries that rely on or produce chemicals have discovered that the eccentric disc pump is an ideal choice when searching for sealless, low-shear and volumetrically consistent operation with optimized product recovery in liquid-transfer applications.
Outlined on Page 68 are a handful of real-world examples of companies that use or produce specialty chemicals and have benefited from the use of eccentric disc pumps in their fluid-handling operations.
Mike Solso is director business development — Americas for Mouvex and PSG. He may be reached at 909-422-1733 or mike.solso@psgdover.com. For more information, visit mouvex.com or psgdover.com.
4 Real-World Examples of Eccentric Disc Pumps in Chemical-Handling Applications
Below are four examples of companies that use or produce specialty chemicals and have benefited from the use of eccentric disc pumps in their fluid-handling operations, continued from page 67.
Table 1. Example 1
Company
Global leader in the distribution of chemicals and related products
Fluid
Tall oil fatty acids
The Challenge
The application requires a pump to pull fatty acids from a railcar and transfer them to a holding tank. The pump is required to run dry for brief periods to ensure that the railcar is completely emptied and as much fluid as possible is cleared from the discharge line. By clearing the discharge line, the operator can minimize waste and disposal costs while removing weight from the line, which makes it easier and safer for plant technicians to handle.
The Solution
After considering a variety of pump technologies including progressive cavity and peristaltic, the operator chose an eccentric disc pump because of its ability to run dry and, more important, the capability to evacuate up to 80 percent of the liquid in the discharge line.
Table 2. Example 2
Company
Global producer of medicines, vaccines, biologic therapies and animal health products
Fluid
50 percent caustic solution at 60 F to 80 F (16 C to 27 C)
The Challenge
The application requires the pump to be mounted on a platform 15 feet above the storage tank, meaning the pump must have dry-suction-lift capability of 18 feet. Because dangerous chemicals are being transferred, the pump needs to be sealless so the liquids can be fully contained with no possibility of leakage through mechanical seals or packing. The actual fluid-transfer operation requires constant recirculation at 50 gallons per minute (gpm) with minimal head for 24/7/365. Additionally, for two hours each day, the pump transfers a caustic solution at a maximum flow rate of 100 gpm with total dynamic head (TDH) of 92 feet. For these two hours, the 100-gpm flow rate consists of 50 gpm of heating recirculation plus 50 gpm of caustic transfer to specific locations in the plant, with a return to the 50-gpm recirculation flow at the conclusion of the two-hour period.
The Solution
Facility technicians tried several traditional pump technologies, but the equipment could not meet the sealless and suction-lift requirements, so the operators turned to eccentric disc technology. The sealless design contains the dangerous chemicals, and the pump is capable of producing suction lift in excess of the 18 feet required for the fluid-transfer application. The pump, which has been operating for two years without incident, is also equipped with a variable speed drive in order to meet the varying gpm requirements.
Table 3. Example 3
Company
Leader in expansion-control systems for the construction industry
Fluid
Polyol and isocyanate
The Challenge
The operator needed a portable system that would allow construction crews to dispense a predetermined blend of polyol and isocyanate through a discharge line to a dispensing nozzle at jobsite locations. This required a pump technology that could provide consistent, low-shear, pulseless flow over time, even as the pump begins to wear.
The Solution
The company chose an eccentric disc pump for this in-line blending application because it provides low-shear and virtually pulseless flow. As other technologies wear, the fluid will slip back past the impeller or rotor, requiring constant adjustment to maintain desired flow rates. Eccentric disc technology eliminates fluid slip because of its unique self-compensating disc and cylinder design, resulting in consistent flow over the entire service life of the pump.
Table 4. Example 4
Company
Global paint manufacturer
Fluid
Mill-based paint pigment
The Challenge
The operator began experiencing seal failure and run-dry damage in internal gear pumps that were used to transfer abrasive paint pigment from a bead mill to a process tank. Bead mills are porcelain-lined rotating vessels that contain 3-millimeter (0.12-inch) diameter ceramic beads that aid in pigment dispersion during paint manufacture. The pumps are next to the bead mills and have a strainer at the suction end that captures any beads that escape should the bead mill’s screen develop a rip or tear. When the suction strainer becomes clogged, fluid supply to the pump shuts off, causing a run-dry condition. Additionally, sealless technology is preferred in order to contain the abrasive liquids that are being pumped, with no chance of leaks at the mechanical seals or packing.
The Solution
The internal gear pumps were not able to satisfy all of the operational requirements, so the manufacturer replaced them with a sealless eccentric disc pump, which can contain the abrasive material while operating in a run-dry condition when needed. The original eccentric disc pump that was purchased was placed in service more than five years ago and continues to provide leak- and maintenance-free operation, with all of the plant’s gear pumps subsequently having been replaced with eccentric disc models.