It took nearly four years, but the OPW employees in Smithfield, North Carolina, were up to the task. They created eight teams of employees to tackle the regulatory requirements and held monthly updates with OPW leadership to keep them apprised of the progress. In the end, the team succeeded in making Smithfield the first Dover site to earn the Carolina Star or the federal government’s VPP Star equivalent.
“Once you get this status, the North Carolina Department of Labor removes the site from the routine scheduled inspection list, which is great, but I believe the biggest benefit of this status is how you get there. You can only get there by the involvement of all of your employees and management, working together for one goal, ZERO accidents,” said Steve Brinchek, Safety Manager for OPW Retail Fueling in Smithfield. “We all are looking for ways to develop, implement and continuously improve our safety management system here at Smithfield. We all are trying to be our brothers and sisters keepers of safety; we all watch out for others.”
OPW’s Retail Fueling facility in Smithfield, NC, was publicly recognized today by the North Carolina Department of Labor for achieving Carolina Star status. Several North Carolina state dignitaries attended the event held at OPW’s Smithfield facility, including North Carolina Commissioner of Labor Cherie Berry who spoke at the event.
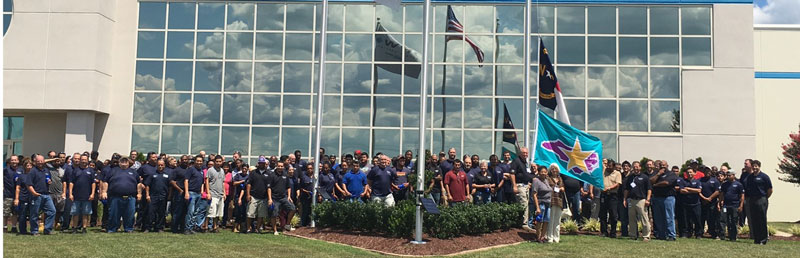
OPW Retail Fueling's Smithfield, North Carolina Staff and Facility
The Carolina Star Program is designed to recognize and promote effective workplace safety and health management systems. The Carolina Star status is equivalent to the federal government’s OSHA VPP award and is awarded to workplaces that demonstrate self-sufficiency in their ability to control hazards at their sites. Smithfield is the first Dover site to earn VPP status or the STAR equivalent.
Mike McCann, vice president and general manager for OPW’s Retail Fueling business said, “The Smithfield employees have put hard work and dedication into creating a safe and healthy manufacturing environment. I am proud of our employees and the time they spent to make this a great place to come to work each day.”
Several North Carolina state dignitaries attended the event held at OPW’s Smithfield facility, including North Carolina Commissioner of Labor Cherie Berry who spoke at the event.
“I am so proud of OPW and the safety culture the employees have developed in their company through the voluntary Carolina Star program,” said Berry. “Congratulations! Well done!”
There are five main elements that sites need to demonstrate to apply for Star status:
- Management Commitment and Leadership
In addition to holding regular meetings with OPW leadership, the Smithfield team hired a new safety coordinator — Luis Mirabal (click here to hear Luis’ personal safety story). The site also begins every quarterly town hall meeting with a message about safety; kicks off monthly Key Performance Indicator meetings with a safety message; has management attend all Safety Huddles & Training; and Greg Kennedy, Director of Operations, signs off on all safety policies.
- Employee Involvement and Participation
Nearly half of all Smithfield employees are active on one of the eight safety-focused teams; all employees attend weekly safety huddles; and employees provide suggestions for safety improvements through the Find it, Fix it program and the Safety Kaizan Boards.
- Hazard Identification and Evaluation
The site instituted an Annual Chemical Inventory and Ventilation Survey for Fibrelite & Plant Site; launched Annual Audiometric Hearing Tests for employees in the Hearing Conservation Program; conducts yearly Industrial Hygiene Surveys; holds Ergonomics Teams Evaluations; analyzes job hazards; holds Safety Audit Team inspections of entire site monthly; and instituted a Safety Concern Team and Incident Investigation Team. Finally, the site management ensures that 90% of all Safety Kaizens are closed in 30 days or less.
- Hazard Prevention and Control
To prevent accidents and near misses the team enforced that safety glasses be worn while on the production floor, safety shoes be worn in all production cells, and hearing protection (earplugs) are required in roto and welding booths. The team also monitors the Contractor Safety Program and takes time to review near miss reports from across all OPW sites.
If an accident does occur, the First Aid Team covers all shifts and is available to provide medical assistance quickly. The teams also coordinate an annual visit from the fire department and holds annual tornado and fire evacuation drills.
Additionally, the employee-led Wellness & Health Team holds an Annual Health Fair for all employees, where they’ve had 82% employee participation in personal health screening.
- Safety and health training
To achieve Carolina Star status, Smithfield managers, supervisors and team leads completed a 10-hour OSHA training course.
Additional training sessions held at the site include:
- Admin Monthly Safety Huddles
- Production employees Weekly Safety Huddles
- Annual training on blood borne pathogens, HazCom, fire prevention, fire extinguisher use
- Safety Team Start-up Training
- Contractor Safety Training
- New Employee Training
- Forklift Train-The-Trainer Training
- NC STATE Training of Trainers
For those sites looking to capture VPP statuses of their own, the attached PowerPoint lists key contacts for each of the eight safety teams, as well as best practices they instituted to capture Carolina Star status.
“When I first saw what was required to be VPP, I was overwhelmed. But Linda Townsley, Director HR/Global Safety — OPW, asked me, ‘How do you eat an elephant?’ Answer, ‘One bite at a time!’ So this is how you approach it. This process takes three to six years to complete, depending on where you are now. But it is well worth the time to complete,” said Steve.