New line designed to handle sour gas
For years, Blackmer kept hearing a similar question from its customer base, which wondered if a larger gas compression offering was being considered. The company, known for its vertical reciprocating compressors, found an answer to that question in the form of its NGH100 series of horizontal oil-free reciprocating gas compressors.
“After years of continually hearing this question, we began some heavy VOC (voice of the customer) to see what was really needed and desired,” said Ron Crouch, product manager — compression, Blackmer. “The result was the NGH100 series.”
The new compressors complement Blackmer’s vertical line, albeit with more flow and high-pressure capability. The series features a horizontally opposed configuration, increased power-frame rating and the ability to handle sour gas that contains up to 8% dry hydrogen sulfide (H2S), Crouch said.
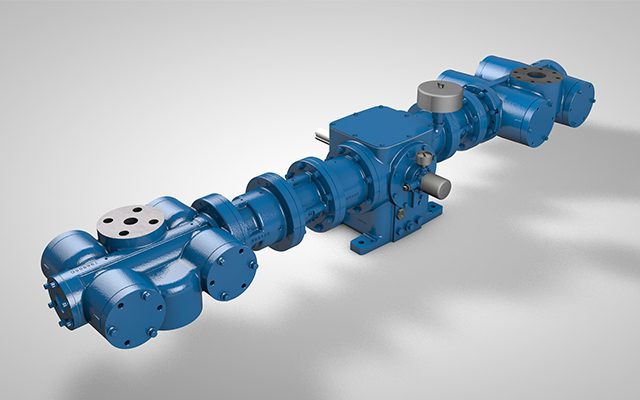
Blackmer’s NGH100 series of compressors feature flow rates of 3000 cfd (85 m3/d).
The NGH100 series is designed for use in vapor recovery, wellhead annulus reduction and artificial lift applications in the upstream oil and gas market, as well as the liquefied petroleum gas business.
The series comes in heavy-duty, single-stage (NGH1013) and two-stage (NGH1023) configurations with flow rates up to 3000 cfd (85 m3/d) and motor speed up to 1800 rpm. The NGH1013 comes in cylinder configurations of 6 x 6 in. (152.4 x 152.4 mm) and 3.25 x 3.25 in. (82.5 x 82.5 mm), both with a 3 in. (76.2 mm) stoke. This model has a maximum allowable working pressure up to 1500 psia (103.4 bar) and weighs 1300 to 1500 lb. (590 to 680 kg), depending on the variation.
The NGH1023 comes in a 6 x 3.25 in. (152.4 x 82.5 mm) cylinder with a 3 in. (76.2 mm) stroke with maximum allow-able working pressure of 1500 psia (103.4 bar). It weighs 1400 lb. (635 kg).
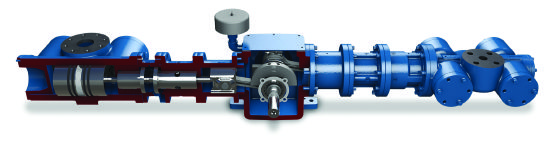
The NGH100 series includes a forged-steel crankshaft and PTFE/PEEK piston rings and rider bands.
Both models are 100 bhp (74.5 kW) rated with a maxi-mum rod load of 7000 lb. (3175 kg) and a maximum dis-charge temperature of 350°F (177°C).
The NGH1013 has a piston dis-placement of 5.3 to 19.2 cfm (9 to 32.6 m3/h) at 100 rpm; 48 to 172.9 cfm (81.6 to 294 m3/h) at 900 rpm; 64 to 231 cfm (109 to 392 m3/h) at 1200 rpm; and 96 to 345.8 cfm (163 to 588 m3/h). The NGH1023’s piston displacement is 9.6 cfm (16.3 m3/h) at 100 rpm; 86.4 cfm (147 m3/h) at 900 rpm; 115.3 cfm (196 m3/h) at 1200 rpm; and 172.9 cfm (294 m3/h).
The NGH100 series also sports a non-lubricated design and ANSI compatible flanged connections. All casted parts are ductile-iron construction, and the crankshaft is made from forged steel. The piston rings and rider bands are made of PTFE/PEEK. In order to handle sour gas, the series incorporates steel wrist pins that ride on steel needle bearings. Also, yellow metal is not used, Crouch said.
“They (the oil and gas sector) really frown on technology that features yellow metal components as often times the fields they serve are ever changing,” Crouch said. “These dynamics can wreak havoc on materials not suited for the harsher conditions and gas components, especially sour service.”
With one question finally answered, it didn’t take long for another to crop up for Blackmer. The latest question is why the company is bringing this compressor offering to the market-place now.
“Our response has been — what better a time to focus on a new product in a cyclical market that is near or at the bottom,” Crouch said. “We felt the continued investment would bring a great option to this and other markets when the tide begins to turn.”