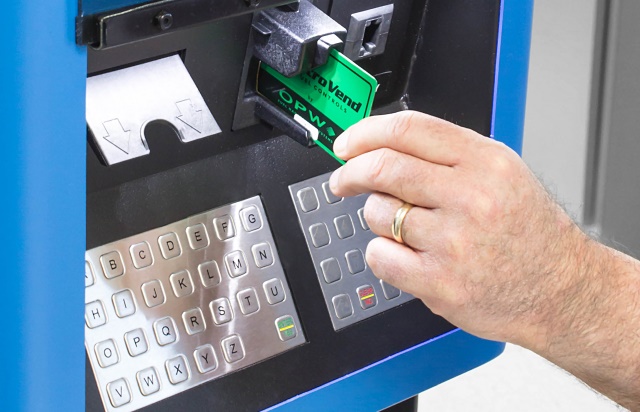
Updating from a traditional key-based cardlock to a system that supports modern activation devices expands a government fuel site’s automated
These days, most public sector fleets that manage their own fuel supplies have some form of fuel management in place to track fueling. As such, determining how to advance an existing system — whether through a minor upgrade or a major overhaul — is the challenge facing many of today's government-operated fuel sites. Should the fuel site replace its outdated cardlock with a new fuel island terminal? Or perhaps update the site controller? Or maybe invest capital to improve the site's communications infrastructure?
There are many equipment investment choices facing government fuel site managers. Here are a few strategies that will allow public sector fuel operators to increase security, improve accountability, streamline operations and enhance their bottom lines.
1. Invest in a cardlock system that supports modern activation devices.
Upgrading from a key-based cardlock to a contemporary cardlock system that supports modern activation devices provides many benefits to fuel site managers. Today's activation devices range from magnetic stripe cards to proximity devices. They also open up an expanded world of automated authorization and data collection possibilities.
Newer activation devices usually require investment in a compatible fuel island terminal and often require the support of a fuel site controller. In most cases the new terminals and site controllers can simply “do more” — collect more fueling data from more users — than their key-based predecessors. For instance, OPW Fuel Management Systems’ Petro Vend 200 (PV200) Fuel Island Terminal, which will be released later this year, is part of a family of fuel control solutions from OPW Fuel Management Systems that support future adaptability. When operated in conjunction with OPW’s FSC3000™ Fuel Site Controller, the PV200 will provide users access to a wide selection of media devices including magnetic cards, chip keys, proximity badges and keys. In many cases, it's even possible to utilize a fleet's existing badge that they use for building access to complete fueling authorization at the fuel island terminal.
2. Increase accountability.
Tracking how much fuel a driver is putting into a vehicle by asking the driver to swipe a card and/or enter a PIN through a cardlock system is a good start. Utilizing a fuel control system that also verifies vehicle information is better. This way the system tracks the amount of fuel being dispensed by a specific user and which vehicle it goes into for increased visibility — and accountability — of fuel usage.
3. Automate data collection and analytics.
Today's fuel management software does much more than track "fuel in, fuel out." For instance, Phoenix SQL® and Phoenix SQL Lite™ fuel management software from OPW Fuel Management Systems interfaces with tank gauging systems to streamline compliance reporting management and automate reconciliation. It also interfaces with fleet maintenance and back-office software. Phoenix's powerful metrics enable government fleet managers and fuel site operators to enhance many facets of their operation.
4. Maximize odometer data.
False or inaccurate odometer entries undermine the efficacy of a fleet's preventive maintenance programs. Many fuel management solutions providers, including OPW Fuel Management Systems, offer odometer reasonability controls that detect inaccurate odometer entries. In addition, OPW's Phoenix SQL® and Phoenix SQL Lite™ fuel management software interfaces with most fleet maintenance programs, enabling fleets to optimize their fueling data in their preventive maintenance programs. In this way, an automated fuel management system helps fleet directors monitor fuel economy and directly maximize the uptime and life cycle of fleet vehicles.
5. Invest in training.
Fuel management is more information-based than ever before and will become increasingly so moving forward. This represents a big change for many people in the fuel industry who are accustomed to manual-driven, hands-on processes. In fact, more and more fleets are hiring analysts to help them leverage their data. Your site may already have the tools it needs to improve operations, but not the experience to capitalize on them. Take advantage of programs available from equipment distributors and manufacturers to ensure your staff is utilizing both their hardware and software components to the fullest extent.
With a long history of helping fuel site managers better control their fueling operations, OPW representatives can help government fleet and fuel site operators craft a fuel management investment strategy that accommodates both immediate budget concerns and long-term fiscal responsibilities.
About the Author
Bobby Hayes is the Domestic Sales Manager at OPW Fuel Management Systems in Hodgkins, IL. He can be reached at (770) 605-9611 or robert.hayes@opwglobal.com.