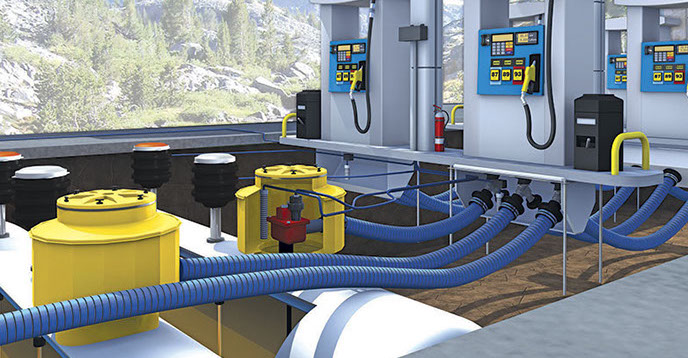
Most people are familiar with Oscar Wilde’s saying that “imitation is the sincerest form of flattery.” For owners and operators in Canada’s retailing-fueling industry, however, imitation can be the sincerest way to improve forecourt safety while alleviating any concerns in meeting regulatory-compliance demands or limiting the liability associated with product releases.
In July 2015, the United States Environmental Protection Agency (EPA) finalized new regulations regarding the inspection, testing and maintenance of underground storage tank (UST) systems at the country’s retail fueling sites. While Canadian fuel retailers are obviously not governed by regulations created by the EPA, many of the provisions in EPA regulations can be beneficial if implemented by Canadian retailers. Additionally, they can often foreshadow future laws that will be created by Canada’s counterpart to the EPA, Environmental and Climate Change Canada (ECCC).
Canadian retailers can also benefit because many new EPA regulations can prompt the companies that develop and manufacture the equipment, components and accessories found in UST systems to enhance their product offerings, whether by redesigning existing products or creating innovative new ones. In the case of the 2015 EPA regulation, new rules were created for, most significantly, the inspection, testing and maintenance of spill-prevention, overfill-prevention and release-detection equipment, along with containment sumps that are used for interstitial monitoring.
Armed with the demands of these new regulations, the manufacturers of UST systems and their components have responded with the following improvements that have been designed to optimize both performance and the ability to meet the new testing and inspection guidelines:
Spill Containers. Next-generation spill containers have been designed so that any damaged or compromised units can be quickly repaired without needing to disrupt the forecourt in order to access them. They are fully grade-accessible with no need to employ jackhammers or heavy equipment to break concrete and, subsequently, no need to refill with concrete.
Double-Wall Spill Containers. These spill containers satisfy the new EPA regulations because they can be inspected by testing the interstitial space between the two walls of the container as a way to ensure that no product leaks have occurred. The double-wall design also helps shorten the test cycle as what used to be an hour-long testing process becomes a five-minute operation.
Overfill-Prevention Valves. Traditional overfill valves needed to be pulled out of the tank in order to be inspected, but newly developed technology allows the valve to remain in the tank during inspection. This lowers the time and cost of the inspection process, while also eliminating the need to deconstruct the system in order to remove the valve from the tank.
Composite Multiports. Multiports are installed over the top of tank sumps to allow access to the tank top. Newer units feature a stainless-steel sealing ring and easy-latch system at the sump lid to help prevent water from entering the tank sump. The composite construction eliminates the shortcomings associated with steel covers, such as corroded sealing surfaces and unsightly appearance.
Sump Entry Fittings. Next-generation entry fittings create a positive and secure seal to the sump wall by using rigid composite materials instead of the rubber materials that were used in the past. The rubber entry fittings of old were susceptible to dry rot, cracking and leaking. Most dispenser-sump designs now feature a conduit-less fitting option that enables the conduit to run along the side of the sump, which removes a common water-intrusion point.
While none of these innovations must be implemented by Canadian fuel retailers (yet), they do represent the next stage in the evolution of the best practices that can be utilized to help ensure the safety of the forecourt. Being proactive and introducing these innovations to their UST systems can also help illustrate that the retailer has the best interests of the customer and the environment in mind.
About the Author: Ed Kammerer is the Director of Global Product Management for OPW, based in Cincinnati, OH, USA. He can be reached at ed.kammerer@opwglobal.com. OPW is leading the way in fueling solutions and innovations worldwide. OPW delivers product excellence and the most comprehensive line of fueling equipment and services to retail and commercial fueling operations around the globe. For more information on OPW, please go to www.OPWGlobal.com.