With more ethanol entering the supply chain, false phase separation alarms pose a particular challenge for Canadian fuel retailers. Unfortunately, false alarms sometimes provoke operators to make short-sighted compliance management decisions that ultimately put station equipment, customer loyalty and profits at risk. Thankfully, new equipment solutions are making false alarms a thing of the past.
Understanding Ethanol’s Role
When enough water mixes with ethanol-blended fuel, the ethanol absorbs the water molecules. The water-saturated alcohol molecules become too heavy to remain suspended in the gasoline solution. They drop to the bottom of the tank, creating layers of different mixtures of product, including an alcohol and water (aqueous ethanol) layer. This process is known as phase separation, and needs very little water to occur. Although Canada only requires gasoline to contain an average of 5 percent of ethanol, 10 percent ethanol-blended gasoline is widely available. The more ethanol, the greater the opportunity for phase separation.
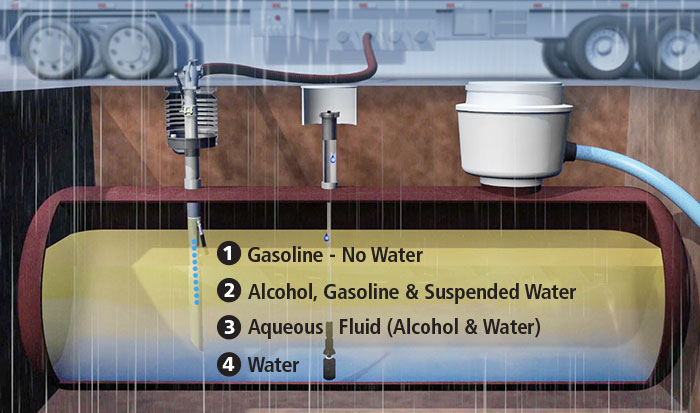
Phase Separation Layers: It takes very little water to cause phase separation, a process that can lead to four distinct layers of inventory inside the tank. Image courtesy of OPW Fuel Management Systems
Phase-separated fuel damages automotive engines, dispensing equipment and a station’s reputation. When phase separation occurs, the aqueous ethanol layer is often near the pump’s in-take tube, putting it in prime position to be dispensed. In the short-term, stations lose revenue due to pump downtime, inventory loss and the expense of purging contaminated fuel from a fueling system and then disposing of it. In the long-term, stations lose sales when word gets out they sold bad gas.
Battling the False Alarm
Some in-tank monitoring devices only use a float to detect phase separation. This weakness results in false alarms. Here’s why: Fuel density is affected by temperature, and floats can’t accurately account for this.
For instance, fuel inside a UST is subject to temperature swings during deliveries. On warm days, fuel inside a tanker heats up. When that warm fuel is added to the cooler fuel in the UST, this temperature fluctuation frequently triggers an alarm. In most cases, the fuel quality is actually within an acceptable range, but the monitoring system can’t make the distinction. As a result, the system shuts the pump motor down.
Inoperable pumps lead to irritated customers and frustrated site operators. Some vexed operators disable the system’s safety checks to prevent the false alarm from triggering a motor shut-down. This is an extremely risky stop-gap that should be avoided. Inevitably, a system stripped of its safeguards will pump bad gas into a customer’s vehicle.
Monitoring Advancements
Early detection is critical to counteracting phase separation. Thankfully, smarter phase separation monitoring devices that are based off of density readings are being introduced.
New aqueous ethanol float-sensor solutions measure water levels as early as 8mm (5/16") (traditional devices don’t detect water until 19mm (3/4"). These new devices also utilize a sensor to continuously monitor fuel quality, which provides real-time, thermal-corrected density readings that accurately account for temperature changes inside the UST. In addition, compatible tank gauges can be programmed to activate an alarm at specific density thresholds. These innovations not only eliminate false phase separation alarms, they enable operators to intervene in a time frame that provides maximum operational uptime in the event that phase separation does occur.
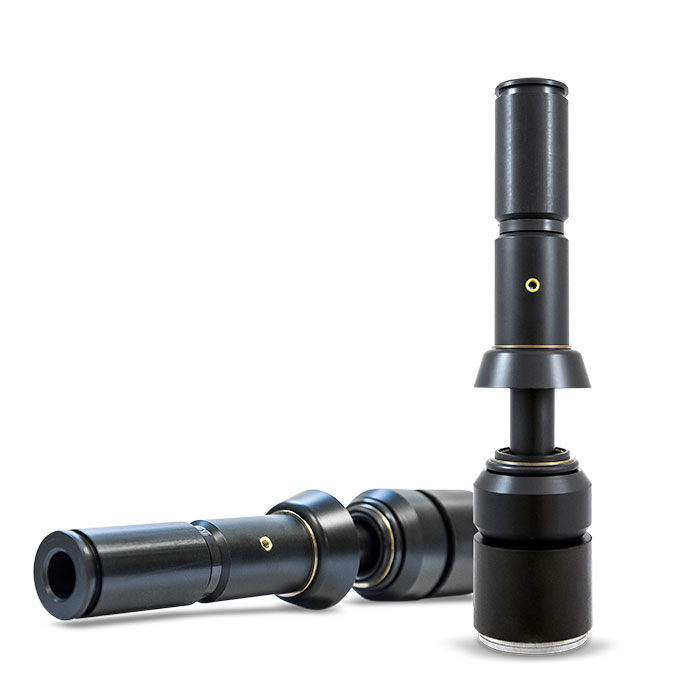
Aqueous Ethanol Float Sensor: OPW's Aqueous Ethanol Float Sensor continuously monitors fuel quality, providing real-time, thermal-corrected density readings. Image courtesy of OPW Fuel Management Systems
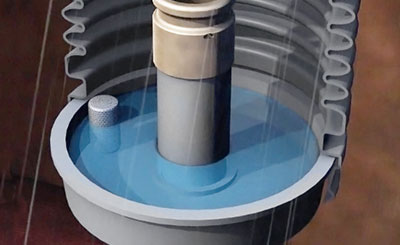
Water Entering Spill Container: Water can enter the tank through the spill container during fuel delivery. Water intrusion in tanks containing ethanol can lead to phase separation. Image courtesy of OPW Fuel Management Systems
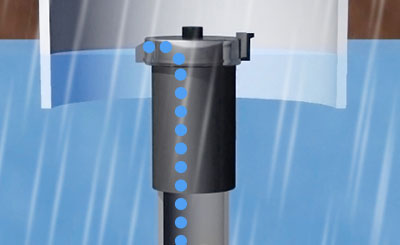
Water Entering Riser Cap: Water can enter the tank through a bad riser cap or service fitting. Water intrusion in tanks containing ethanol can lead to phase separation. Image courtesy of OPW Fuel Management Systems.
Pete Neil is the Global Product Manager at OPW Fuel Management Systems, based in Hodgkins, IL. Neil has considerable expertise in tank monitoring equipment solutions. He can be reached at pete.neil@opwglobal.com. OPW is leading the way in fueling solutions and innovations worldwide. OPW delivers product excellence and the most comprehensive line of fueling equipment and services to retail and commercial fueling operations around the globe. For more information about OPW, please visit OPWGlobal.com.