Both fixed and flexible technologies offer distinct advantages, but only if manufacturers optimize important operational parameters.
The one constant thing about technology is that it is constantly changing and evolving. Don’t think so? In that case, ask the people who rushed out to buy the latest iteration of a smartphone, but then find themselves standing in line waiting to purchase the latest new-and-improved version just six months later.
The same is true in the world of manufacturing. Engineers in every industry must perpetually review their processes and weigh the potential benefits of implementing a new technology against the potential pit-falls. In many cases, the decision can boil down to the answer to this basic question: Stick with the tried and true, or switch to the shiny and new?
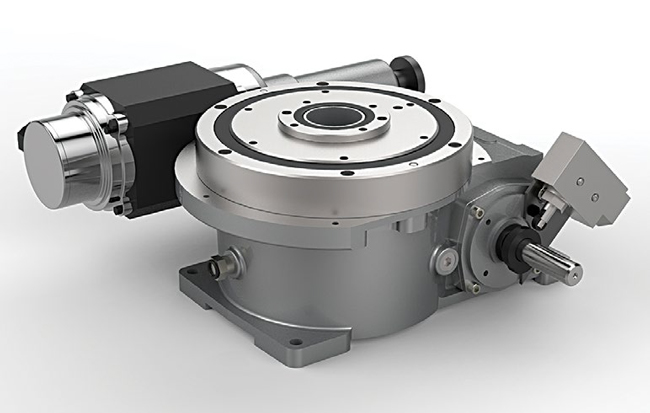
If there will be large, unbalanced loads during the dwell period, a fixed-cam system may be the best option. Servomotors can be affected by imbalanced loads. Photo courtesy DESTACO
In manufacturing operations that require automated assembly systems, the dominant motion control technology has been based on the fixed-stop indexing cam. In recent years, however, servo-driven technology, using a constant-lead cam, has grown in prominence. The constant-lead cam is giving manufacturers a flexible alternative to consider. This article will highlight the benefits (and potential drawbacks) of each system to help manufacturers make more educated decisions when reaching the answer to that vexing tried-and-true or shiny-and-new question.
Defining the Terms
Fixed-stop cams are mechanical automation components that have been machined to be used on an indexer. The cam has two distinct operating periods:
- Index period: The number of degrees on the cam that are used for moving the indexer into position.
- Dwell period: The remaining portion of the cam that is used to determine the length of the indexer’s in-station position where no movement occurs.
In other words, if the indexing operation calls for the cam to rotate 90 degrees and then stop, it is cut in such a way that those operational parameters are achieved every time. The motion cannot be changed.
By comparison, the index characteristics of the constant-lead cam are not determined by the way the cam has been cut. Rather, the characteristics are determined electronically by a programmable device—in most cases, a servomotor—instead of having the indexing and dwell times built into the cam. In this instance, constant-lead cams do have a programmable indexing period, but no true dwell period. The servo drive is always reading the motor’s encoder, comparing the current position against the programmed position and making corrections, even when the cam has ostensibly completed its movement and is stopped.
These subtle, yet significant, differences in the operation of the fixed-stop and constant-lead cams—as well as their attendant operational pros and cons—must be considered by the manufacturer before a decision is made concerning which type of technology to deploy. Often, the pro for one may be a con for the other.
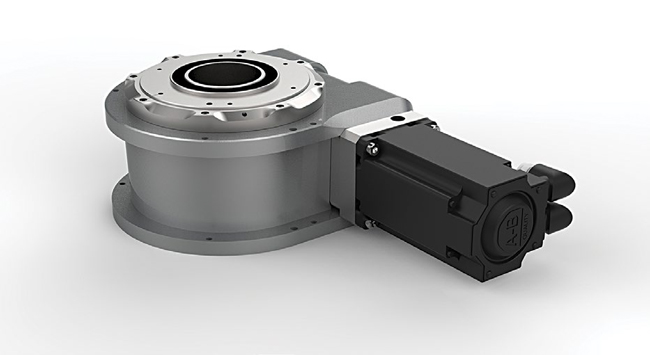
With a rotary table driven by a constant-lead cam and a servomotor, the indexing motion can be changed from 90 degrees to 120 degrees simply by changing the program. A table driven by a fixed-stop cam would have to be replaced or rebuilt. Photo courtesy DESTACO
Pros and Cons
The fixed-stop cam has been the technology of choice for indexing operations for decades. As such, it has gained a loyal following among machine builders that favor a mechanical design, and that may be, by extension, reluctant to consider a different technology.
The fixed-stop cam has many advantages:
- Since indexing systems that use fixed-stop cams are mechanical in nature, startup is less involved because the cam controls all movements. Simply power the indexer up and the cam reliably delivers what it has been designed to provide with not a lot of programming, decision-making or system debugging required.
- Because of the way the cam is ma-chined, when it comes to a stop, it is locked into that position, without the chance that any ancillary movement will occur.
- Fixed indexing systems are robust and can easily handle high load capacities.
- Maintenance is simpler. All the operator has to do is change the oil after a predetermined number of hours, days or months of operation, and grease the parts. That said, the fixed-stop cam has disadvantages, too:
- Fixed indexing systems rely on hard automation to operate, meaning that if the cam is designed for a certain movement, that’s the only way it can ever be used.
- If the parameters of the indexing operation need to be altered (for example, if a new part is 20 percent larger than the previous one), that can’t be done with a fixed-stop cam. The indexer will require major modifications.
- Mechanical fixed automation systems cannot provide process feedback on operational parameters, such as level of electrical draw.
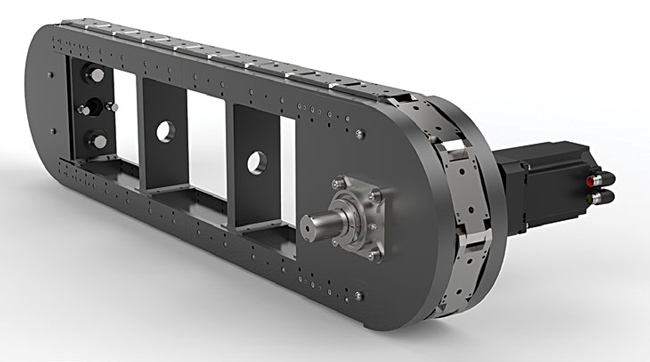
The fixed system, like this cam-driven precision link conveyor, is the best choice if the part must be rigidly held place during processing. Photo courtesy DESTACO
While many in the so-called “old guard” may be married to fixed indexing technology, the benefits of switching to the new flexible indexing systems are numerous. Again, any decision will need to be made carefully after considering all of the pluses and minuses.
The benefits of flexible automation include:
- Some automation systems require a certain task to be run constantly for a year or 18 months, but then it will need to be modified, say, from a 90-degree move to a 120-degree move. In this case, the servomotor can simply be re-programmed with the new parameters, whereas the mechanical system would have to be replaced or rebuilt.
- A flexible system can be configured to work with different parts and part sizes just by selecting a different program. The motion is controlled by the servomotor.
- The servomotor can monitor how much power is being consumed. That information can be fed to a PC that accumulates the data and can create a report on variables like power demand, uptime and downtime, displacement rate, velocity, and acceleration and deceleration time.
- The use of a central programmable controller (to control the servomotor) makes the operation of flexible systems more predictive. That may sound counterintuitive, at first. However, most machines have many axes of motion (six, eight, 10 or more). When their operation is tied to a central controller, that controller can sync and fine-tune the actions that are occurring at previous and succeeding workstations. This can’t be done in a fixed system that has no central controller.
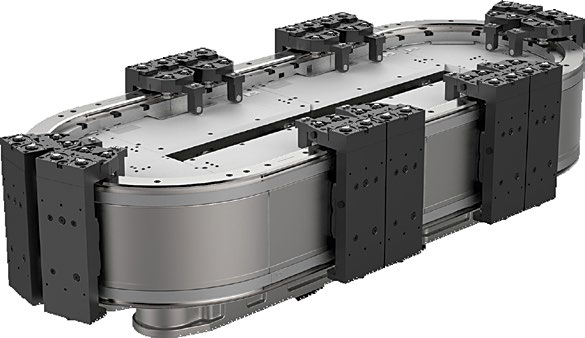
The CAMCO iQue Conveyor’s iTRAK programmable linear drive allows independent control of multiple magnetically propelled movers along straight or curvilinear paths. Movers can be moved along the conveyor in forward or reverse motion at varying speeds, and in individual, continuous, batch and asynchronous motion sequences. Photo courtesy DESTACO
There are cons to flexible automation, as well.
- Flexible indexing systems can often have a higher upfront cost than their fixed-system cousins. Fixed systems consist of an AC motor, position switch and variable-frequency drive. A servomotor is more sophisticated than the typical AC motor. Because of the flexible system’s feed-back capabilities, it requires additional hardware, including power cables, drives that send signals to the motor, a programmable logic controller (PLC) that coordinates its operation through the amplifier to the motor, and a more complex electronic system that drives the system’s flexibility.
- The technical skill level needed to set up the system is greater. Engineers must write a program that tells the cam when and for how long to accelerate, how long to stay at a certain velocity, when and for how long to decelerate, and when to come to a stop. In fixed systems, these parameters are machined into the cam.
- The programming can take several days and some trial and error to find the setup that best meets the needs of the end user.
- The servomotor’s continuous feed-back loop, which is always seeking and correcting the position of the cam, may compromise the system’s precision. In this case, a braking mechanism can be installed on the servomotor to stop any ancillary movements.
- Maintaining a flexible system can be more difficult. Any erroneous adjustment can alter the recommended operating pattern, which can have an adverse effect on production rates and even lead to a damaged indexer.
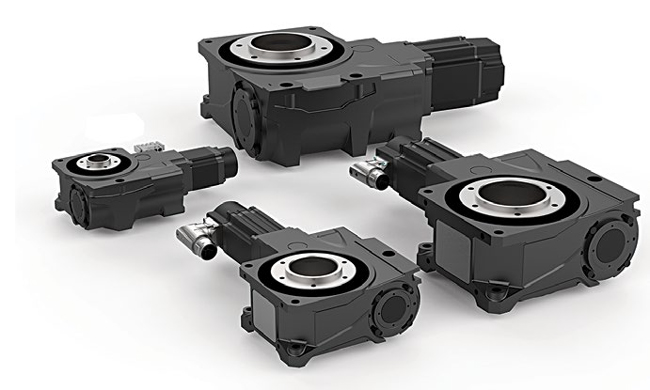
The GTB series of servo-driven rotary indexing tables is available in four center distances: 40, 63, 80 and 100 millimeters. Photo courtesy DESTACO
Rotary or Linear?
Automation systems are typically available in two types of configurations: rotary indexing tables or linear conveyors. Today, both rotary and linear systems can be outfitted with either fixed or flexible automation systems.
Again, there are specific considerations that must be weighed before choosing fixed or flexible automation for each.
A typical rotary indexing system might consist of a six-position dial plate. The first station loads a part. The second might perform, say, a gluing task. The third performs a welding task. The fourth drills a hole. The fifth inspects the assembly, and the sixth offloads the product. This has traditionally been the sweet spot for fixed automation systems. However, such a system can perform equally well with a servomotor—and offer some level of flexibility, as well.
In processes that are more involved, the linear conveyor system has been the first choice for manufacturers. Advances in technology now enable the movement of the conveyor to be controlled by either traditional fixed cams or servomotors. In fact, both automation technologies can be used together, say, for an operation that requires a part to be moved 6 inches one day, but 12 inches the next.
The introduction of flexible systems into the operation of linear conveyors also forces the operator to consider a new parameter: whether the production process needs to be synchronous or asynchronous. A linear system with synchronous movement—which can employ either a fixed or flexible motion system—may consist of 10 processes, nine of which take 4 seconds to complete before a final 20-second inspection process. In a fixed system, the inspection process would be conducted on a one-by-one basis, with subsequent parts waiting in line. With asynchronous movement, three or four finished parts can move into the test bay at the same time and be tested simultaneously. An asynchronous movement—again, which can feature either fixed or flexible automation—allows more products to be completed in a faster time and allows it to be done with one machine rather than four chain-link conveyors.
Asynchronous movement is accomplished by the new magnetic conveyor systems that have been designed to replace the chain-link operation with magnets that can more accurately control the conveyor’s movement. The benefits of the magnetic systems—which, again, can feature either synchronous or asynchronous automation—are that they can produce faster line speeds, are more predictive, require less frequent maintenance, are significantly smaller than traditional chain-link conveyors, are able to be programmed around the process, and have push-button changeover capabilities that eliminate the need for change parts.
Final Thoughts
Manufacturers that are deciding between fixed and flexible automation systems would be wise to consider some specific questions and criteria concerning the design and expectations of their operations. These include:
- Will there be stations that have different processing times on the same equipment? An asynchronous motion system might be best for that operation.
- Will there be more than one type of part processed that requires different motion parameters? This sounds like a servomotor process.
- Is there a likelihood of processing additional or different parts on the same machine in the future? If the machine is only ever going to make one part during its lifetime, fixed is the way to go. If it’s a project where the parameters will be changed at some point, flexible is probably the better choice.
- Does the part need to be rigidly held or locked in place during processing? The fixed system is the best choice if the part needs to be locked firm, though a flexible system can be considered if the servomotor is outfitted with a braking system.
- Will there be any large, unbalanced gravity loads while in the dwell period? This is an area where fixed systems shine because they can handle heavier loads and the operation of servomotors can be affected by imbalanced loads.
- Does the process require displacement, velocity or acceleration feedback during movement? If the accumulation of feedback by a central controller is required, then a flexible-based system is the best choice.
- Is there value in being able to more precisely control or restrict movement while in the dwell period of the cam? With fixed systems, the dwell period is the dwell period, with no chance for ancillary movement to occur. Some operations, though, may require the dwell time to be sped up or slowed down at certain times, which makes it ideal for a flexible system.
- Will there be technical support avail-able in the field to program, reprogram, adjust and troubleshoot if a servomotor controls the system? If technical support is not readily available, a fixed mechanical system is the better option.
Of course, there are many more questions to consider since every manufacturing operation is unique. Rest assured, though, that either the “tried-and-true” fixed system or “shiny-and-new” flexible system will meet the needs of the operation if thoughtful, diligent deliberation has preceded the ultimate decision.
For more information, call 888-DESTACO or visit www.destaco.com.