By Pete Neil / OPW Fuel Management Systems
Most U.S. gas stations already sell E10 as their predominant fuel. The number of stations selling E85 increased over 300 percent from 2006 to 2016. And the number of U.S. stations offering E15 has more than doubled since 2016. Ethanol is solidifying its place in the supply chain.
The increased distribution of ethanol has given rise to one of retail fuel’s most unforgiving cautionary tales: phase separation. This in-tank catastrophe has destroyed hundreds of thousands of gallons of inventory across North America and resulted in untold losses in customer loyalty.
Making matters worse, tank-monitoring systems that produce false phase separation alarms — a common problem for fuel retailers —increase the likelihood of distributing contaminated fuel. Site operators, frustrated by the false alarms, sometimes make imprudent compliance management choices. These decisions put station equipment, customer loyalty and profits at risk.
Fuel marketers who understand how phase separation occurs and what new tools are available to help prevent the distribution of contaminated fuel will be in the best position to protect their bottom line.
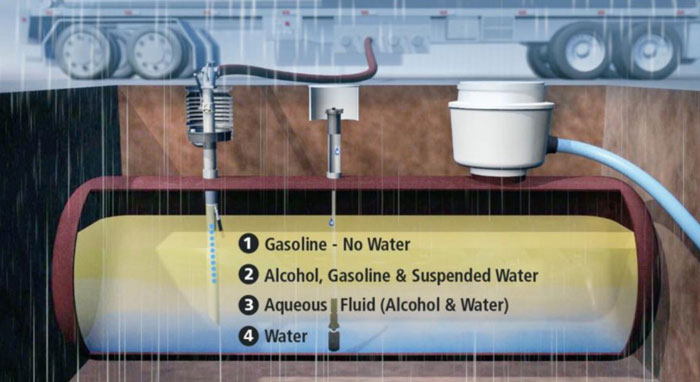
It takes very little water to cause phase separation, a process that can lead to four distinct layers of inventory inside the tank. / Image courtesy of OPW Fuel Management Systems
The Truth About Phase Separation
To skeptics, phase separation is little more than an urban legend circulating within the fuel industry. But to stations that have suffered its ill effects, it’s an indisputable source of financial regret.
Here’s what every fuel retailer who has experienced phase separation has learned the hard way: water is the enemy of fuel. Every fuel tank has some water in it. Too much water, though, can cause a reaction inside tanks containing ethanol. The reaction creates a concentrated layer of water and corrosive ethanol. If this aqueous ethanol fuel is pumped into vehicles, it can damage automotive engine components.
Ethanol is an alcohol fuel. When enough water in the tank mixes with ethanol-blended fuel, the ethanol absorbs the water molecules. The water-saturated alcohol molecules become too heavy to remain suspended in the gasoline solution. These water-laden alcohol molecules plummet to the bottom of the tank. This precipitation creates layers of different mixtures of product within the tank, including an alcohol and water (aqueous ethanol) layer.
Unfortunately, it takes very little water to cause phase separation. For instance, water can collect in the spill container during a rainy fuel delivery or water can seep in through a bad riser cap gasket or service fitting. In a tank with 10,000 gallons of E10, it takes just 40 gallons of water to cause phase separation.
When phase separation occurs, the aqueous ethanol layer is often right where the pump’s in-take tube draws fuel into the dispensing system. Not only does fuel that has completed phase separation put automotive engines at risk of failure, the aqueous ethanol can damage dispensing equipment.
Once phase separation has occurred, station operators face several short-term consequences — all of which are costly: pump down-time, inventory loss, the expense of purging contaminated fuel from the system and disposal fees. In the long-term, a station that has had an incident with phase separation will lose future sales (and credibility) when word spreads that the station distributed bad gas.
Understanding the Limitations of Floats
There are many misconceptions about the capabilities of various phase separation detection devices available today. Understanding the limitations of certain types of devices and the benefits of others can mean the difference between timely intervention and costly consequences.
In-tank phase separation detection is available in two basic styles — a weighted float or density sensor. Which style of device is inside your tanks largely determines whether or not your site experiences false phase separation alarms.
Fuel density is an indication of product quality. Obviously, water and phase separation compromise product quality. But fuel density is also affected by temperature. Floats lack the ability to account for temperature changes in the tank. They can’t distinguish between fuel that has undergone phase separation or fuel that has experienced a sudden temperature fluctuation due to a routine delivery. That is how false phase separation alarms occur.
Here’s a real-world example of how a false phase separation alarm happens in a system utilizing float-based phase separation detection:
Fuel inside an underground storage tank stays cool even when it is sweltering outside. But, on warm days fuel inside a tanker heats up. During a fuel delivery, the hot fuel is rapidly added to the cool inventory in the tank, causing density fluctuations.
Float-based phase separation detection devices are weighted to the density of aqueous fluid (800 kg/m3). When hot fuel is added to a tank, sometimes the fuel density will rise above 800 kg/m3. This causes float-based systems to issue a false phase separation alarm because, unlike detection devices with a density sensor, the floats cannot provide temperature-corrected density readings. Although the fuel quality is actually within an acceptable range, the monitoring system can’t make the distinction between product that is undergoing a temporary temperature swing and product that has completed phase separation. As a result, the false alarm then triggers the pump motor to shut down.
Unfortunately, many site operators frustrated by invalid stoppages have disabled their system’s safety checks to prevent service interruptions. This choice puts the fuel site at an even greater risk of distributing contaminated fuel, a much longer service interruption and more costly consequences.
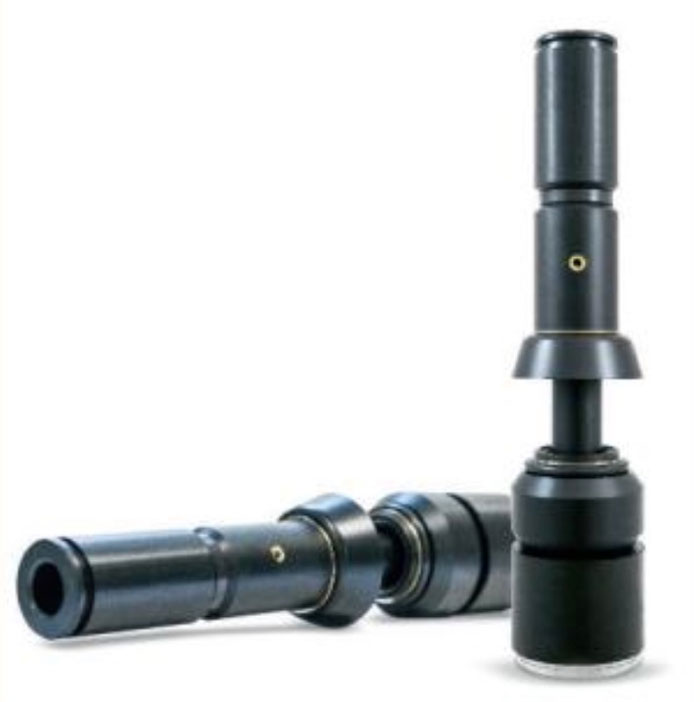
OPW’s Aqueous Ethanol Float Sensor continuously monitors fuel quality, providing real-time, thermal-corrected density readings. / Image courtesy of OPW Fuel Management Systems
How Density Sensors Prevent False Alarms
Phase separation detection devices that include a density sensor are able to account for temperatures changes inside the tank. This capability eliminates false phase separation alarms. OPW’s Aqueous Ethanol Float Sensor, for instance, constantly monitors the fuel density inside the tank and net-corrects for thermal changes. Readings are continuously streamed to the tank gauge.
Detection solutions that include density sensors offer the benefit of being able to issue a warning in addition to an alarm. Float-based monitoring solutions are unable to do this because they are weighted to a specific density. Either the float has risen enough to trigger an alarm or it has not, there is no in-between. Because float-based devices do not continuously monitor fuel quality, they do not offer the operator an indication that phase separation is nearing; they simply issue an alarm.
Tank gauges from OPW can be configured to issue a warning and then an alarm at user-defined thresholds. This ability to be notified early that conditions inside the tank could lead to phase separation empowers operators to initiate corrective actions before contaminated fuel is dispensed and causes a catastrophic engine failure. If a potential phase separation problem is occurring, operators utilizing a modern density-sensor based system can delay a delivery, which would stir up the contents of the tank and increase the potential for phase separation. The operator can then remove as much product from the tank as possible before further saturation happens. Then a new load of fuel can be dropped. For this operator, the situation becomes more about inventory management than crisis intervention.
The Ethanol Age Is Here
As the automotive fleet continues to turn over, more vehicles approved to fuel higher ethanol blends will hit the highways. Attracted by the price break that higher ethanol blends provide, consumers will be empowered to take advantage of the savings. Fuel marketers need to address this shift in their fueling equipment.
A tank-monitoring system that includes modern phase separation detection is essential to meeting the quality assurance needs of the ethanol age. Fuel site operators who leverage the benefits of a density sensor in their phase separation detection will prevent costly inventory headaches from crippling their forecourt. They will also realize more efficient daily operations, know they are dispensing quality fuel and win with customers in the long-run.
About the Author:
Pete Neil is Global Product Manager at OPW Fuel Management Systems. Contact him at pete.neil@doverfs.com. For more information about OPW Fuel Management Systems, visit www.opwglobal.com/opw-fms.