SI Group puts safety first in transfer and containment of extremely hazardous material
By Dave Morrow, OPW Engineered Systems
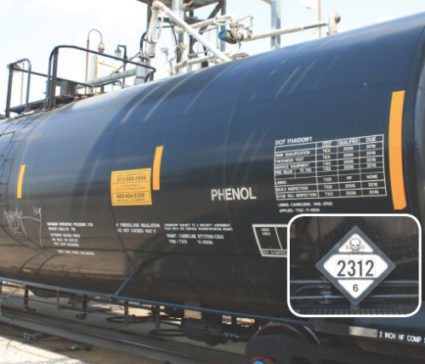
In any type of manufacturing operation where numerous and varied components come together to create a finished product, there is one basic rule: there are some components you just don’t take any chances with.
One of these is the organic compound commonly known as Phenol. At room temperature it is a white, crystalline solid, but when heated to 130ºF (54ºC) and higher it becomes a highly viscous liquid that is used in the production of alkylated Phenols. These compounds are then used in a variety of rubber, industrial resin, adhesive resin, fuel and lubricants, and plastic additives production applications.
In its liquid form, Phenol is classified by the U.S. Department of Transportation as a “Class 6.1 (poisonous) material.” It is highly toxic and can cause severe burns, while its vapors are corrosive to the eyes, skin and respiratory tract. Phenol may cause second and third degree burns. Inhalation of Phenol vapors can cause fluid to collect in the lungs, resulting in a condition known as edema. Prolonged exposure to Phenol can have harmful effects on the central nervous system and heart, resulting in dysrhythmia, seizures and even coma.
These extreme characteristics are why the Occupational Safety and Health Administration (OSHA) has established a permissible exposure limit (PEL) to the skin for Phenol of 5 parts-per-million (ppm) over an eight-hour work period. Additionally, the Centers for Disease Control and Prevention’s National Institute of Occupational Safety and Health (NIOSH) has determined that Phenol is immediately dangerous to life or health when exposure reaches 250 ppm.
In addition to its hazardous characteristics, Phenol is the lifeblood of the SI Group, Inc., of Schenectady, NY, one of the world’s leading developers and manufacturers of Phenolic resins, alkyl Phenolic resins and alkylated Phenols. The SI Group has operating facilities on six continents and works closely with clients that are situated in more than 90 countries around the globe. One of the SI Group’s operating facilities in the United States is known as SI Group Manufacturing and is located in Freeport, TX, USA, about 60 miles (95 kilometers) due south of Houston on the state’s Gulf Coast. SI Group manufacturing receives a steady supply of liquefied Phenol via pipeline, railcar and, on rare occasions, tank truck.
“We are a leading producer of alkyl Phenols and our products serve a vital role in a variety of markets, from surfactants to lubricants, engineered plastics, and paint and fuel additives,” explained Doug Wright, Manager-Quality Assurance for SI Group Manufacturing’s Texas-based operations. “Phenol is one of our raw materials, and one of the key building blocks. We react it with other materials to create these alkylated Phenols. We make 17 to 20 unique products or grades of Phenols, and we’re a 24/7 operation that has to maintain pace to keep up with business.”
Handle With Care
All of this means that Wright and his staff are constantly performing a balancing act: on the one hand, producing Phenol-reliant products at a rate that satisfies the production schedule and end-users, but on the other, doing it in a safety-first way that does not endanger plant personnel or the environment through accidental-release incidents. If the raw Phenol were able to be delivered to the plant solely through a pipeline, Wright’s concerns would be greatly reduced, but that mode of transfer is not always the first choice of Phenol shippers, or even available to them.
“Our preference is to get the Phenol by pipeline, which we do when we can because it takes all of the human touch out of it,” he said. “When we can’t, rail is our next preference. Truck unloading is the least-preferred method because it’s a smaller volume, plus the safety mechanisms are not as redundant.”
Within railcar deliveries, Phenol is typically unloaded from the top of the car. In terms of safety, Wright prefers top unloading, which utilizes the pressure created by a transfer pump and eductor tube to force the Phenol from the railcar.
“The suppliers of the Phenol have their railcars configured in a certain way because of the toxic nature of the material,” he said. “If Phenol was unloaded from the bottom of the railcar, it would require the technician to get under the car to make connections and that would make them more vulnerable if there was a leak because the path of egress is more difficult. The ability of the technician to get out of harm’s way is easier with top unloading.”
Another danger with bottom unloading is that if an unloading line fails, the effects of gravity will allow whatever amount of Phenol remaining in the railcar to escape until the tank car’s valves can be completely closed. By comparison, if there is any type of line failure in a top-unloading operation, the flow of Phenol can be interrupted by simply turning off power to the pump.
Another thing that Wright is constantly aware of is that many of the top-unloading Phenol railcars that arrive at SI Group Manufacturing are equipped with a pressure-assisted unloading system. In these types of systems, the introduction of pressurized nitrogen is used to maximize the flow rate. When the unloading is completed a closed vapor-balance operation is performed to equalize the pressure inside the railcar. Even then, however, there is still a limited amount of pressure inside the railcar, creating the opportunity for a pressure blowback or blip when the fittings are released, meaning that any residual Phenol in the railcar may be released onto the technician or the ground, putting them at risk and necessitating the need for a cleanup procedure.
The Containment Plan
The combination of Phenol’s hazardous characteristics and the potential for product releases when unloading railcars means that the fittings and disconnects used in the handling of Phenol must be highly reliable and capable of total Phenol containment. Since 2007, SI Group Manufacturing has relied on Drylok™ Dry Disconnect Couplers from OPW Engineered Systems, Lebanon, OH, USA, for use in its Phenol-handling applications.
“We’ve had these couplers on our Phenol vapor and liquid lines since 2007 because we were looking for something that would give us as close to total containment of the Phenol as possible,” said Paris Watson, Maintenance Technician at SI Group Manufacturing. “With the toxicity of Phenol you can’t have any spills, so we had to make certain that we didn’t lose anything.”
According to Watson, the dry disconnect couplers meet the needs of SI Group Manufacturing, and handlers of toxic or hazardous materials worldwide, because its design features an interlocking handle that averts accidental spills by preventing uncoupling while the valve is open. It is designed for high-pressure applications since it can be opened and closed against 150-psi maximum head pressures, while its easy-flow interior optimizes the flow rate in high-pressure or high-viscosity applications. Repairs can be performed without the coupler being removed from the piping, and the unit is designed with a flat face allowing less than 1-cc of fluid loss fluid loss.
“The couplers have worked very well. Even on the pressure-assisted railcars they close off any remaining pressure, so there’s less of a concern that something can be sprayed back at you,” said Doug Wright. “With the nature of this material and the dangers associated with it, we’ve trained all of our employees on what precautions to take. They know that if they even get a drop of this material on them they need to get in a safety shower as soon as possible; they have a high level of awareness of the dangers of Phenol. With that said, we don’t want any leaks of this material at all and having the dry disconnect couplers adds a level of security for our technicians. It’s a much cleaner operation. They take some of the worry out of doing the job — and remove some of the fear, as well.”
SI Group Manufacturing worked out some initial kinks with the couplers by heat-tracing and insulating the supply lines, which keeps the Phenol in a liquid state and keeps it from plugging the lines, and using PTFE (polytetrafluoroethylene) encapsulated O-rings. According to Watson, since 2009 the couplers have performed without incident.
Conclusion
The hazardous characteristics of Phenol are so severe that SI Group Manufacturing requires any personnel charged with handling it to wear a PPE (Personal Protective Equipment) suit consisting of a slicker, face shield and gloves at all times.
“We have a lot of respect for that material and we want to minimize the direct contact our personnel has with it as much as possible,” said Wright. “We require them to wear a full PPE when handling it and the couplers offer another reliable level of safety. They give a second layer of protection and added peace of mind when handling this extremely dangerous material.”