Source: CPC
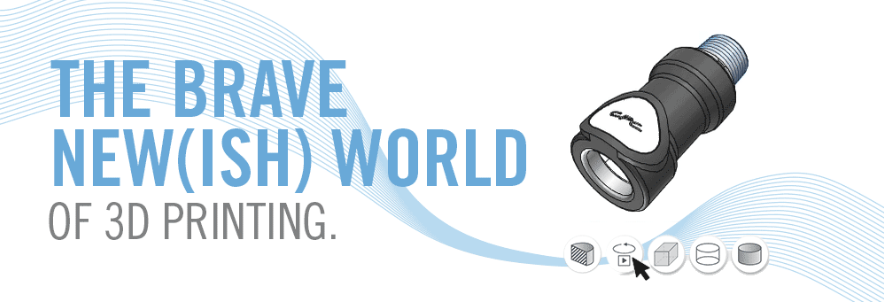
3D printing is used extensively among manufacturers worldwide, including here at CPC. We run our 3D printers every single day, all over the world, to better our business and to help our customers.
Being able to fabricate a concept within a day shortens the design process from a few months to a matter of days. We can converge on the right design quicker while allowing our customers to give feedback quickly. This gives our engineers the opportunity to make design tweaks earlier in the process when it’s relatively inexpensive leading to better products.
Another benefit of physical prototypes is that CAD drawings don’t communicate how a fluid connector looks and feels. A 3D printed prototype gives you the opportunity to hold the product in your hand, so you can get a sense of the way it feels and how it will look in your system or application.
A recent example of the role 3D printing played in the development of a new product was with our LQ2 product line. Our thermal management engineers went through a few iterations with 3D printed prototypes which allowed them to dial-in high flow capacities and make geometry changes to the valve that would result in maximum flow and minimal pressure drop. This allowed our engineers to cut weeks from the development timeline. If our engineers would have used regular injection molding, it would have taken roughly 12 to 16 weeks. But, with 3D printing, the development cycle was cut to about four weeks.
3D printing allows your ideas to be developed and refined faster. Connect with a CPC engineer to see how 3D printing can get your product to market faster.