Source: Dover's
CPC (Colder Products Company)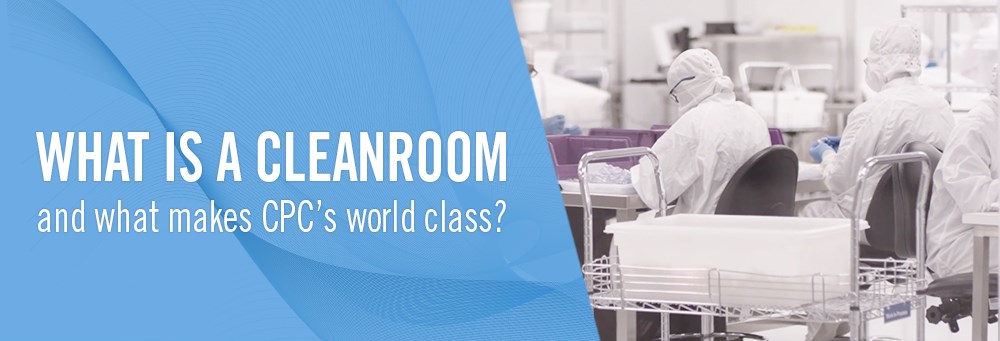
Biopharmaceutical manufacturers worldwide rely on CPC for high-quality connectors and couplings. The key to ensuring our products are clean is having robust procedures and monitoring programs that meet and exceed ISO Class 7 cleanliness requirements.
What is a cleanroom?
Before we discuss the specifics of CPC’s cleanroom, let’s do a quick refresher on the basics. A cleanroom is a controlled environment where pollutants like dust, airborne microbes and aerosol particles are filtered out in order to provide the cleanest area possible. Particulate contamination inside a cleanroom is kept within tightly controlled limits by forcing clean HEPA filtered air into the cleanroom. This creates an internal air pressure greater than the ambient pressure, which reduces particulate intrusion around doors and other unsealed areas. Additional variables that are controlled are: temperature, air flow and humidity.
Understanding the ISO Class 7 rating
Cleanrooms are rated based on the number of non-viable particulates allowed. CPC’s cleanroom is certified to meet the ISO Class 7 standard. The particulates are classified as either viable or non-viable. Viable particulates are organisms such as bacteria, yeast and molds. Non-viable particulates are categorized by sizes: 0.5 microns and 5 microns.
Maintaining our ISO Class 7 rating
To maintain our rating, monitoring our particulate load is essential. We use a real-time particulate monitoring system to verify levels of non-viable particulates in our cleanroom. If the count exceeds the alert limit, alarms will sound and key CPC personnel will be notified automatically, so the issue can be immediately addressed. Other key metrics observed by our real-time monitoring system are: differential pressure, temperature and humidity.
To monitor viable particulates, CPC utilizes two techniques; active and passive sampling. The first is a hand-held monitoring device that draws cleanroom air across an auger plate where any microorganisms are collected and cultured. We also do passive sampling where we set auger plates in the cleanroom to collect and culture any bacteria that falls from the air and settles on the plate. In both cases, criteria are set to verify acceptable viable limits.
Controlling particulate contamination is a process, not an event. Contaminants are continuously generated by people, processes and equipment so they must be continuously removed from the cleanroom.
Designed to be clean
CPC’s cleanroom uses a hard-walled design versus using plastic draping to create a soft-walled enclosure. Hard-walled cleanrooms offer several significant benefits:
- It’s very unlikely to be breached.
- It enables higher differential air pressure.
- It allows for precise control of temperature and humidity levels.
- Cleaning and maintenance are easier.
Keeping it clean
Even a cleanroom needs to be cleaned. We have different cleaning protocols that take place at intervals of daily, weekly, monthly, quarterly and annual. These systematic cleanings help to further ensure that our cleanroom meets the ISO Class 7 criteria.
Employees who enter CPC’s cleanroom not only wear gowns, they wear hairnets, hoods, face covers, gloves and shoe covers. Then, before entering the cleanroom, they pass through an air shower that utilizes high-pressure HEPA filtered air to remove dust, fibrous lint and other contaminants. This forceful cleansing of surfaces prior to entering the cleanroom greatly reduces the number of airborne particulates introduced.
On an annual basis, CPC has an outside firm audit and re-certify the cleanroom. Calibrated equipment is used to check our non-viable particulate levels and to confirm:
- The operation of all HEPA filters.
- The number of room air changes per hour.
- The differential pressure between inside and outside of the cleanroom.
These procedures verify that our cleanroom is continuing to operate within the ISO Class 7 cleanroom standard.