Refrigerants are an essential element of successful operations, providing the proper temperatures to keep products in an ideal state for short or long periods of time. They can be found in a variety of industrial equipment, such as refrigerators, air conditioners, freezers and dehumidifiers.
Refrigerants are specialty gas liquids produced at a dedicated manufacturing facility and are then transferred to an industrial plant that requires refrigeration. They are stored in large chillers, which must be continuously operational.
The importance of refrigerants to the world is apparent: without them, society would be unable to function at the same capacity as it does today. However, transferring refrigerants around the world is not as simple as handing it off from one person to the next. Refrigerants require the proper equipment for processing and transfer, and not just any pumping technology is capable of processing refrigerants effectively. While many different technologies can be used, a clear choice stands above the rest: regenerative turbine pumps.
Regenerative turbine pumps, like the pump shown in FIG. 1, function as a superb solution to the demands of processing refrigerants—they can maintain high pressures while handling low-viscosity fluids and are not susceptible to cavitation damage.
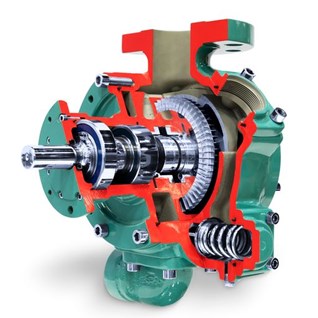
|
FIG. 1. Regenerative turbine pumps function as an excellent solution to the demands of processing refrigerants. |
This article will examine the capabilities of regenerative turbine pumps and why they work more effectively than other pumping technologies when handling refrigerants.
A closer look at regenerative turbine pumps. Though considered rotodynamic, regenerative turbine pumps have close parallels to positive displacement (PD) pumps. Regenerative turbine pumps provide multi-stage performance from a single-stage impeller designed to optimize performance. This allows the pump to create high differential pressures at low flow rates.
Regenerative turbine pumps function using a rotating, non-contact, free-wheeling impeller disc that has ~60 small cells on its periphery. When the liquid enters the suction port, the impeller captures it and accelerates it around the narrow hydraulic channel surrounding the cells. Kinetic energy carries the liquid rapidly around the channel. Within one revolution, this motion builds energy and pressure.
The pump technology's name stems from its function—the continuous regeneration of small liquid cells creates the differential pressure capability of the pump. Regenerative turbine pumps have the versatility to transfer liquids at high pressure and low flow, while also processing entrained vapors or liquids at or near their boiling point. These conditions limit most pump technologies, causing performance issues, cavitation, vibration and noise. However, regenerative turbine pumps do not falter from those conditions.
Specifically, regenerative turbine pumps can handle viscosities of 0.1 cSt–50 cSt with differential pressures up to 20 bar (300 psi) and have a maximum allowable working pressure of up to 493 psi (34 bar) to enable handling liquids with high vapor pressures.
Typical regenerative turbine pumps generate flowrates up to 200 l/min (52.8 gpm), though some variations can operate with higher flowrates. Some newer iterations of this technology can reach peak flowrates as high as (and potentially higher than) 600 l/min (158.5 gpm).
This pump technology thrives because of its design. The spiral motion and its speed diminish the chances for cavitation and pulsation by smoothing the fluid and collapsing the vapor bubbles immediately when they form. Vibration and noise problems are eliminated in most situations because the pump operates with a smooth flow and a hydraulically balanced design.
Refrigerants are not the only application where regenerative turbine pumps excel. This technology functions optimally in applications known for having low-viscosity fluids, such as aerosol filling, as well as liquefied petroleum gas (LPG) and autogas distribution. Other applications include vaporizer feed, cylinder filling, boiler feed water and ammonia transfer and distribution.
Comparison with side-channel pumps. As previously stated, in addition to their similarities to PD pumps in some aspects of performance, regenerative turbine pumps also have similarities to side-channel pumps (e.g., both pumps can self-prime and perform optimally under poor suction conditions). The differences come from the size of the pump and ease of maintenance.
Side-channel pumps are designed to have a larger footprint, mainly due to their multiple pumping stages. Side-channel pumps can have as many as four to eight stages to meet the duty parameters of a particular application. With that many stages, side-channel pumps and their large footprint become more complex to accommodate an installation’s demands.
Regenerative turbine pumps, which feature a single-stage, can match the performance of the side-channel pump while also functioning at two-pole speeds. Side-channel pumps typically operate at four-pole speed.
With a larger size and more complexity, side-channel pumps require more components to properly function. More components mean increased wear on all components, all of which are prone to eventual failure. When that happens, those parts must be replaced, adding to the pump’s maintenance and total ownership cost.
Regenerative turbine pumps do not require a large footprint or a complex design. Instead, regenerative turbine pumps have a compact footprint and up to 25 components, making them easier for operators to maintain over time. Spending less time on maintenance and components saves time and money. Also, the less-complex design means operators do not need a veteran engineer to maintain them, allowing any technically savvy associate with moderate experience to keep the technology running.
Comparison with other PD pumps. Sliding vane pumps also match up well with regenerative turbine pumps and even have some advantages. The primary advantage comes from the technology having a higher hydraulic efficiency and better effectiveness during priming.
Despite regenerative turbine pumps not sharing these traits, they have other features that make the technology effective in similar applications. With fewer moving parts than sliding vane pumps, regenerative turbine pumps can operate continuously without many drawbacks.
Operators do not have to worry about taking regenerative turbine pumps offline to replace wear parts on a frequent basis. Similar pump technologies have a variety of wear parts, each with different service and lifecycles. With fewer moving parts, operators of regenerative turbine pumps spend less time shutting down the pump for scheduled maintenance and do not have to stock as many components for eventual replacement.
Regenerative turbine pumps have two components subject to wear: the mechanical seal and, occasionally, the impeller. During scheduled maintenance, operators do not need to take them out of service. Regenerative turbine pumps have parts that can be replaced within an hour without removing the pump from the pipework or even disconnecting the motor.
Performance wise, regenerative turbine pumps can operate continuously without pulsation and cavitation. This and the ability to continuously operate relieve engineers of their concerns about frequent stops.
Sliding vane pumps might also have difficulty producing the varying differential pressures required to transfer refrigerants. Regenerative turbine pumps do not struggle with varying differential pressures.
Takeaways. When it comes to challenging applications, such as processing or circulating refrigerants, operators have many pumping choices. However, if a technology with versatility at its core is the goal, regenerative turbine pumps are their best option.
These pumps can handle a vast range of liquids under varying conditions in multiple applications. The common deterrents—cavitation, vibration, entrained vapor—that challenge most pumping technologies do not have the same effect on regenerative turbine pumps. Operators can expect longevity from this technology, as well as long intervals between maintenance.
The value of regenerative turbine pumps when handling refrigerants is clear. They have the versatility to process it optimally and effectively.