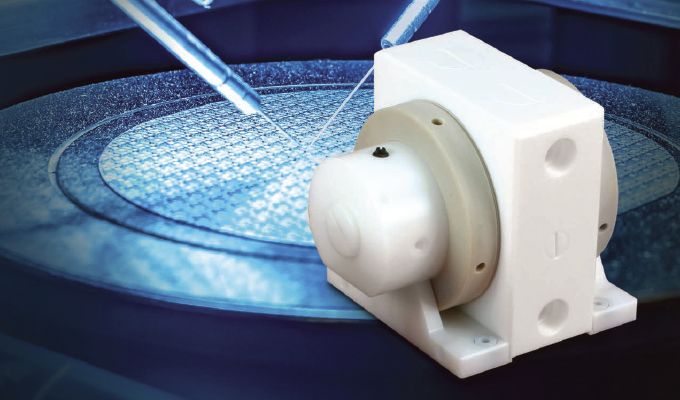
The driving force for the founding of eMAXX GmbH can be said to have been found in the saying, “Great minds think alike.” Namely, in 2017, several people who had developed a friendship while working together in the 1990s in the German semiconductor industry had the idea that they should start their own consulting, engineering, design and programming company for the industry.
That seed of an idea has grown, five years later, into a company, which is based in Dresden, Germany, that, in addition to semiconductors, now offers services that are designed to help operators in additional industries optimize the performance of their companies. These other industries include pharmaceutical, food and beverage, chemical, oil and gas, and solar.
“Our portfolio has grown to the point where we now offer design and consulting, plant engineering, plant construction, equipment commissioning and startup services, inspection and maintenance services for an expanding network of clients,” says Alexander Keßler, managing director of eMAXX and one of its founders. “Our slogan, ‘simple.solutions,’ really expresses our corporate philosophy in a single sentence and adhering to it has allowed us to currently have fifty employees and proudly enabled us to work with almost every semiconductor manufacturer in the east and south of Germany.”
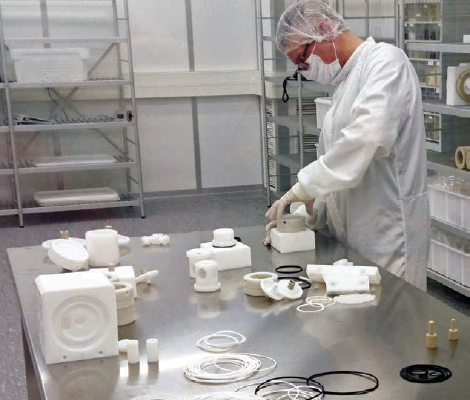
KNOW YOUR ROOTS
Indeed, while eMAXX has expanded its reach into other industries, aiding its clients in optimizing operations in the manufacture of semiconductors, which are also known as integrated circuits (ICs), remains the foundation of its business—and one that it knows intimately. The semiconductor industry—and information technology itself—is also constantly evolving, with the pursuit of enhanced automation and digitization of machines driving this constant state of evolution. At this point, reducing the semiconductor’s physical size is the focus of the product’s evolving geometry.
“Over the past five years, semiconductor chip technology has continued to change, with transistors getting smaller and smaller,” explains Keßler. “This makes it challenging to produce products that are both high in purity and quality and have long mean time before failure (MTBF).”
Because of these critical and constantly changing demands, it is incredibly important that semiconductor manufacturers identify and deploy the proper equipment at every stage of wafer production, chip design and production, and product testing.
PUMPS IN SEMICONDUCTOR PRODUCTION
Industrial pumps are vital pieces of equipment that are required in the various stages of semiconductor production. However, wherever the handling and transfer of liquids of varying viscosities, particulate sizes and abrasion levels is required, air-operated double-diaphragm pumps (AODD) have proven to be a first-choice technology.
“AODD pumps are mostly used to pump chemicals, slurry in the chemical mechanical planarization (CMP) process that smooths the IC’s surface with chemical and mechanical forces, solvents, and in the transfer of deionized water and treatment of wastewater,” says Keßler. “The pumps can be used in a range of activities, from the transfer, circulation and distribution of chemicals to the mixing of different liquid compounds.”
Knowing that its clients needed not only AODD pumps for its semiconductor-manufacturing processes, but highly reliable ones, the team at eMAXX initiated a search for an AODD-pump technology that could meet the needs of its clients in the areas of reliability, efficiency, durability and safety. That search led to Almatec®, a product brand of PSG®, a Dover company.
“When researching Almatec AODD pumps, we found that they possessed the capability to meet our clients’ demand for reliable pumps that offer high-purity performance with long MTBF,” says Kessler.
WHY ALMATEC AODD PUMPS?
Since 1984, Almatec has been developing AODD-pumps that have proven to be ideal for the handling of high-purity chemicals, abrasive slurries, acids and solvents, even at high temperatures. Possessing these capabilities is paramount in semiconductor manufacture, which is why eMAXX has chosen to recommend the following Almatec AODD-pump models to its customers for use in critical and sensitive semiconductor-production applications for many years.
FUTUR Series AODD Pumps
eMAXX recommends Almatec’s FUTUR Series pumps for use in high-purity liquid-handling applications because they excel in this area. They feature a design that allows liquids to flow straight through the product chambers within the center housing. This design ensures that only one side of the housing comes in contact with the liquid, which reduces the number of flow bends to only two, resulting in minimized surface area while eliminating the need for sliding parts in the product chambers, along with O-rings in the wetted area.
FUTUR pumps also feature no fastening elements, such as tie rods or lamps, with contactless cascade sealing between the product chambers improving the pump’s structural integrity. All of these design enhancements work to minimize the generation of particulate matter as the pump operates.
The FUTUR Series pumps are available in four models that have been designed for use in different types of applications:
- FUTUR T: Corrosion resistance and higher tensile strength for handling acids and caustics
- FUTUR H: For high-temperature applications involving acids and caustics
- FUTUR E: Abrasion-resistant for handling semiconductor polishing slurries and CMP
- FUTUR S/SH: Constructed of solid-block 316L stainless steel for use with solvent mixtures and strippers, as well as being ATEX-certified
All models feature a compact, simple design with few parts and small footprint, and solid-block construction for long-life operation with the all-plastic FUTUR T, H, and E models containing no metal. Also standard on all models is the PERSWING P® air-control system that requires no lubrication or maintenance. Additionally, separate pulsation dampeners are available for all models and sizes, and they can be retrofitted onto existing installations with no disassembly of the pump and piping needed. Operationally, all models are self-priming with low-shear liquid handling and produce low noise levels when running. The FUTUR H model has a temperature range of up to 392 degrees Fahrenheit (200 degrees Celsius).
E-SERIES AODD PUMPS
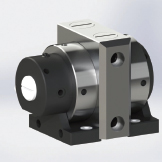
For more utilitarian liquid-handling duties, eMAXX suggests E-Series AODD pumps. The advancements within the E-Series’ design include an innovative ring-tightening structure that works against a diaphragm-sized ring, which spreads bolt force out and allows higher bolt torques, increased flow capacity via an optimized flow pattern, decreased air consumption, reduced noise levels, and a pulsation dampener suitable for flanged connections.
All of these capabilities combine to make E-Series pumps ideal for use as a drain pump in supply applications and a chemical-handling pump in water/wastewater treatment.
The E-Series pumps feature solid plastic-block construction in PE/PE conductive or PTFE/PTFE conductive with diaphragms constructed of EPDM, PTFE/EPDM compound, PTFE Modified, NBR, or ATEX variations, and ball valves constructed of EPDM, PTFE, NBR, or stainless steel. The standard PERSWING P® air-control system requires no lubrication or maintenance and the pump has no drives, rotating parts, or shaft seals while providing self-priming and low-shear operation. The pumps are compatible for use in temperatures up to 248 degrees Fahrenheit (120 degrees Celsius) and offer expansion compensation so they can be used in applications with fluctuating temperatures.
CONCLUSION
On average, eMAXX has been delivering twenty-five to fifty new FUTUR or E-Series AODD Pumps to its clients per year since 2019, along with more than 600 parts kits annually. To Keßler, the reasons for this impressive volume are obvious.
“We like that all of the models deliver reliable and solid performance even when handling high-purity chemicals in which no product contamination is allowed,” he said. “Almatec pumps are also easy to maintain. There really is no reason for our semiconductor clients not to use Almatec AODD pumps.”
FOR MORE INFORMATION
Kai Röhrig is the product manager for Almatec® and can be reached at kai.roehrig@psgdover.com. PSG® is the global pump, metering and dispensing-solution expert, enabling the safe and efficient transfer of critical and valuable fluids that require optimal performance and reliability in applications where it matters most. Additionally, PSG is a leading provider of flow meters designed to reduce waste and downtime while accurately measuring, monitoring and controlling the distribution of fluids. Headquartered in Oakbrook Terrace, IL, USA, PSG is comprised of several world-class brands, including Abaque®, All-Flo™, Almatec®, Blackmer®, Ebsray®, em-tec®, Griswold®, Hydro™, Malema™, Mouvex®, Neptune®, PSG® Biotech, Quantex™, Quattroflow®, and Wilden®. PSG products are manufactured on three continents – North America, Europe and Asia – in state-of-the-art facilities that practice lean manufacturing and are ISO-certified. PSG is part of the Pumps & Process Solutions segment of Dover Corporation. For additional information on PSG, please visit psgdover.com. PSG: Where Innovation Flows.